Process chain for knowledge-based construction and design of movement elements for the manufacturing of individual orthoses (sub-project)
Runtime |
01.09.2019 – 31.08.2021 |
Overall Project | Entwicklung einer wissensbasierten Prozesskette zur Fertigung integraler patientenindividueller und lastangepasster Orthesen (IndivO) |
Funding | BMWi promoted within the framework of the AiF-program ZIM |
Project staff |
Dipl.-Ing. Lydia Mika |
Partners | Orthopädie- und Rehatechnik Dresden GmbH (ORD) |
Professur für Numerische und Experimentelle Festkörpermechanik (NEFM) |
Motivation
Orthoses currently available on the market are often unable to fully meet the required functions, such as patient-specific adaptability and the associated increased comfort. In addition, there is an increase in product demand, as is to be expected due to demographic developments in Germany, and there is not enough qualified personnel to meet this demand satisfactorily. In addition, production is very complex and not easily reproducible, especially in the short term, and it requires lengthy iterative manual rework by specially trained personnel. Furthermore, the transfer of the necessary know-how is difficult, as the production is very dependent on the experience of the orthopaedic technician.
The aim of this cooperation project is to develop a solution that partially automates the manufacturing process of the orthosis and makes the orthosis properties targeted, defined and reproducibly adjustable. Beyond current research, the properties of the resulting orthoses in particular will meet patient-specific requirements to a greater extent and provide the orthopaedic technician with a manageable tool for creating them. With the implementation of a continuous, closed process chain that can be described, from the indication through defined parameters to the type selection and the exact dimensioning of the desired end product, the orthopaedic technician can thus be relieved. In this way, the technician can produce orthoses of high quality despite increasing demand. Above all, the expectations of support and comfort as well as the satisfaction of the patients can be fulfilled and also secured in the future.
Objectives
The aim of the (sub-)project is to develop a process chain for the partially automated production of patient-specific, load-adapted lower leg orthoses using a digital model of the patient's leg. This is accompanied by the provision of predefined and mechanically designed movement elements that can be individually selected to suit the patient. These allow a targeted movement or deformation of the orthosis without additional joints, e.g. made of metal. Generative manufacturing processes are to be used to integrate these and other functional elements such as perforations, connection elements for buckles and other design elements into an integral orthosis component. A knowledge-based approach using a neural network will be used to design the movement elements. This will provide the necessary geometry parameters based on patient-specific input variables and simulation data.
Project content
The project structure with central work steps is shown in the following figure:
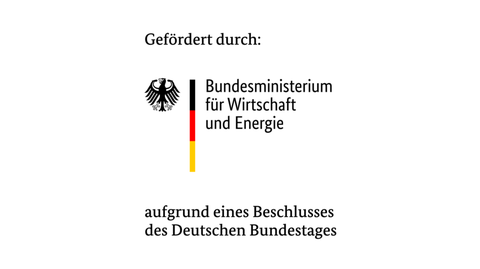
© BMWi
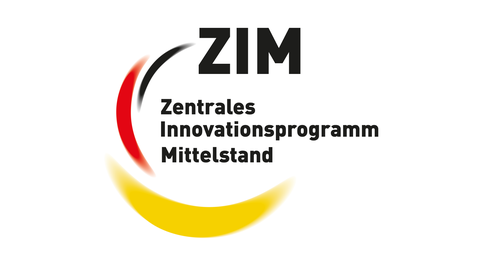
© ZIM