Vehicle Inertia Measuring Machine
Table of contents
VIMM - Vehicle Inertia Measuring Machine in cooperation with CFM Schiller
As part of a research cooperation between the TU Dresden and the CFM Schiller GmbH, a modern, fully automated measuring machine for determining mass, center of gravity and moments of inertia of motor vehicles and individual components is now available. The aim of the cooperation is the further development of the measuring machine by conversion to a modified motion method. This shall further increase efficiency while reducing the measurement effort. With the integration of VIMM into the parameterization process (the so called “Parametrierstraße”), a powerful tool for the complete vehicle and component parameter identification is available.
VIMM - Vehicle Inertia Measuring Machine in cooperation with CFM Schiller
Construction and functional description
The VIMM is used to determine the center of gravity and moments of inertia of motor vehicles and components. Both variables have a decisive influence on dynamic wheel loads and wheel load changes as well as the natural vibration behavior of a vehicle. Movements of the vehicle body can have a negative effect on the driving stability. Furthermore, frequency ranges of the body vibration must be avoided, which can lead to nausea for the passengers.
The VIMM consists of a base frame on which a platform is attached by means of a spherical joint. This platform is the core of VIMM. The VIMM has three hydraulic actuators that perform the roll, pitch and yaw motions. The actuators are attached to the base frame by adjustable bearings. Load cells, which measure the forces introduced during the measuring process, are integrated at the connection points of the actuators. The tilt angles of the platform around all three axes are measured by three incremental angle sensors.
The specimen is moved on the platform with a crane and a special lifting frame. During the measurements the suspension is blocked and the vehicle is fixed to the platform. The determination of the center of gravity takes place in X-Y-plane statically by evaluation of the measured forces. The center of gravity height is determined by a quasistatic rolling motion. The inertia parameters are determined by dynamic measurements around the roll, pitch and yaw axes.
VIMM - Vehicle Inertia Measuring Machine in cooperation with CFM Schiller
Main topics
-
- Determining the position of the center of gravity of the entire vehicle
- Determination of mass and inertia characteristics of entire vehicles
- Analysis of the influence of different loading conditions
- Measurement of individual components or subsystems (for example engine-gearbox assembly)
Key facts
-
- Fully automated measuring system for the determination of the inertia parameters in just one measurement operation
- Time efficient measurement and fast result delivery
- Various loading conditions possible
Downloads and technical data
- Max. Total mass of the test piece: approx. 2600kg (depending on the center of gravity height)
- highest accuracy with center of gravity heights up to 800 mm above the central joint
- Max. Wheelbase: 4.350 mm
- min. Track Width: 1,200 mm
- min. Driving height 80 mm
- maximum angle of inclination:
- roll angle +/- 20 °
- pitch angle +/- 6 °
- yaw angle +/- 6 °
ENG: Documentation
Contact
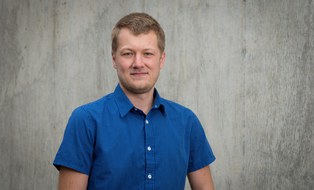
Research Associate
NameMr Dipl.-Ing. Philipp Ulbricht
Vehicle Dynamics, Driving Comfort, Tire Behavior
Send encrypted email via the SecureMail portal (for TUD external users only).
Visiting address:
Jante-Bau, JAN 35-D George-Bähr-Straße 1b
01069 Dresden