Modelling and experimental analysis for optimizing a heat exchanger in two-phase passive cooling systems
Motivation:
The storage of nuclear fuel in active cooled water pools is the standard practice for nuclear power plants. A promising approach to enhance the reliability of the nuclear power plant safety are two-phase passive heat transfer systems. This concept works even in conditions beyond design basis, e.g. station black out. The heat transfer capacity of such a system depends among others on the heat exchanger performance. Therefore the cooling system would benefit from the reduction of the resistance of the heat exchangers.
Objectives:
The main focus of the project is an optimization of the heat exchanger located at the heat sink. Inside this heat exchanger the fluid is condensed and heat is transferred to the ambient. The substantial heat resistances of this heat exchanger are the condensation heat transfer on the tube inside and convective heat transfer to air. The wettability inside the tube surface can be reduced by a hydrophobic nano-coating. In this case condensation process changes from film-wise condensation to dropwise condensation, which increases the condensing heat transfer coefficient considerably. To increase the heat transfer on the air side, the heat transfer surface can be increased by fins. To enhance the heat transfer coefficient to air, different fin tube designs were analyzed.
Methods and results:
A surface modification needs to be very thin, so the flow cross-section will not be reduced and highly stable to functionalize the heat transfer surface over a long operating time. Furthermore, it must be possible to modify the inner surface of a tube having small diameter. To achieve these requirements of the surface modification, a novel monolayer coating technique was developed and employed. An experimental analysis for surface treatments on stainless steel surfaces was done to create low wettability heat transfer surfaces.
A preliminary design of an air cooled fin tube was made and assessed by CFD-simulations. A CFD-based optimization of geometry, e.g. fin height, fin thickness, fin pitch, was made. On the basis of these results a new fin design was developed. This design will be analyzed experimentally also under application conditions. Different parameters of the finned tube and the flow channel were studied and optimized for operating and accident conditions of the nuclear power plant.
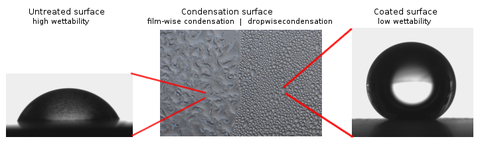
Influence of untreated metal surface (left) and nano-coated metal surface (right) on condensation (center)
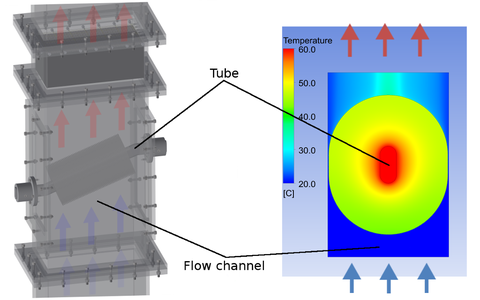
CAD-drawing of the test section of the flow channel and the test tube (left). CFD-simulation of the temperature profile of an air cooled finned tube (right)
Publications:
S. Unger, D. Sarker, U. Harm, U. Hampel
Enhanced drainage during condensation in passive safety systems for spent fuel pools by SAM coating
Proceedings 47th Annual Meeting on Nuclear Technology (AMNT), 10.-12.05.2016, Hamburg, Germany