Constructive aspects of the generation of essential surgical templates and functional implant structuring (sub-project)
Runtime | 01.10.2020 – 31.12.2021 |
Overall project | Design and additive manufacturing of surface- and structure-optimised knee implants and associated surgical templates (OptiKneeBM) |
Funding | BMBF |
Project staff | |
Partners |
Dornheim Medical Images GmbH |
Engelke Engineering Art GmbH |
|
FIT AG |
|
Institut für Bioprozess- und Analysenmesstechnik (IBA, Heiligenstadt) |
|
Universitätsklinikum Freiburg, Klinik für Orthopädie und Unfallchirurgie |
Motivation
The cost-, time- and quality-appropriate production of individual knee implants can only succeed if problem-oriented and tailored CAD/CAM processes are established. For this, suitable software solutions with common interfaces between the sub-competences must be developed and established. The current procedure for individual implant fitting is characterised by extensive manual steps in data processing and is therefore only used in individual indications. In the preliminary project EXPERTEB a consortium from different fields has dedicated itself to these tasks. CAD solutions for a parameterised design of individual knee implants were developed. This was done on the basis of individualised computer tomography data (CT data), which are the starting point of every medical history. From these discrete image data, suitable parameters were first extracted within the project consortium, which on the one hand describe the individual knee and consequently could be used for implant construction and design. This procedure, the parametric approach, should reduce the previous process times for individual fitting by 70% and make the process safer and more sustainable overall.
Objective
In the previous project, the establishment of an interface between the doctor (orthopaedist/surgeon) and the designer was seen as an innovative approach to a solution. This interface was successfully established and is now to be supplemented by further innovative functions. This initially concerns support in the generation of individual surgical aids in the form of templates, but equally the functionalisation by means of porous structures.
The necessity of considering a largely automated generation of individualised templates results from the theses listed below:
- The process for generating individual knee implants from the predecessor project EXPERTEB is designed in such a way that the models are generated (partially) automatically with little user interaction. It is therefore essential that the necessary tools such as surgical templates are also generated as automatically as possible, as otherwise the creation of the templates would represent the bottleneck in the entire process chain in terms of time, accuracy and costs.
- At present, templates usually have to be redesigned for the respective individual patient case, as the template models sometimes have different geometric and functional properties than the implant and therefore do not arise immediately during implant construction.
- Individual surgical templates improve the surgical process by assisting the surgeon and shortening the operating time.
- Individual surgical templates enhance the idea of an individually adapted implant, in which precisely fitting incisions and drillings are made.
- The incisions, drillings etc. to be made must be adapted to the geometry of the developed EXPERTEB implant. A new design for the templates must therefore be created.
Project content
The contents for the sub-project are defined as follows:
- Development of parametric geometry models of surgical templates for individual adaptation to the patient case on the basis of patient-specific input variables
- Development and expansion of existing software solutions for preoperative planning to achieve a holistic process for the production of individual knee implants and associated templates as well as the testing of the surgical templates developed under 1.)
- Development of procedures for the design-side integration of open-porous structures into the implant models according to medical and structure-optimised specifications as well as their practical implementation
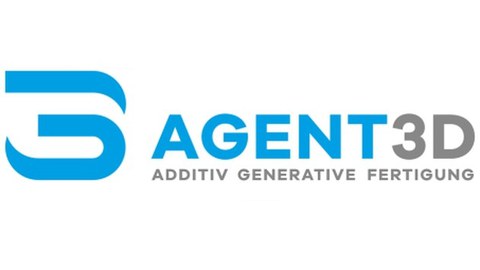
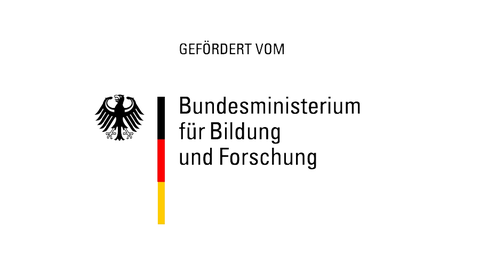
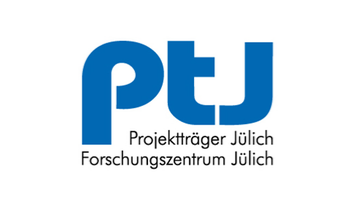