Datenreduktion in 3D-Tagebaumodellen
Laufzeit | 31.10.2013 – 31.03.2015 |
Finanzierung | BMWi gefördert im Rahmen des AiF- Programmes ZIM |
Bearbeiter | Dr.-Ing. Matthias Klaus (ehem. Mitarbeiter) |
Motivation
Tagebaubetreiber setzen in den letzten Jahren zunehmend Systeme zur ganzheitlichen Betrachtung bergbaulicher Produktionsprozesse ein. Wesentliche Funktionen sind die permanente Erfassung und Zusammenführung der relevanten Betriebsdaten und die zeitnahe Bereitstellung der aktuellen Gelände- und Geräteinformationen in aufbereiteter Form für vielfältige Zwecke wie Leistungsberechnungen, Sicherheitsprüfungen oder Instandhaltungsplanung. Server verwalten zentral die von vielen Stationen gelieferten Daten, erzeugen die Visualisierungsdaten und stellen sie auf Anforderung von Clients bereit. Hier existieren aktuell Probleme, da zunehmend Drahtlosnetze und mobile Endgeräte auf Clientseite benutzt werden. Mangelnde Bandbreite bzw. zu große Datenmengen limitieren momentan die Einsatzmöglichkeiten der Monitoringsysteme.
Zielsetzung
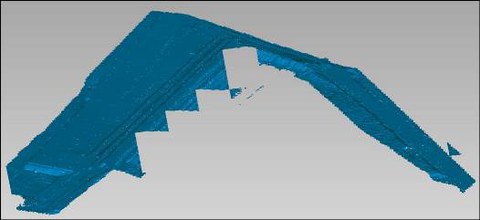
Abb. 1: Oberfläche Tagebau (Beispiel)
Die 3D- Informationen der Tagebauoberfläche stammen aus verschiedenen Datenquellen (Überflugmessungen, Scanner an Arbeitsgeräten, Berechnungen aus Geometrie und Bewegung der Schnittwerkzeuge).
Das in Abb. 1 gezeigte Beispiel deckt eine Fläche von ca. 5 km x 5 km ab und weist Höhenunterschiede von ~140 m auf. Die Auflösung in der Ebene beträgt ~30 cm, Abb. 2. Die Rohdatenmenge beläuft sich auf ~114 Mio. Punkte und ~228 Mio. Dreiecke.
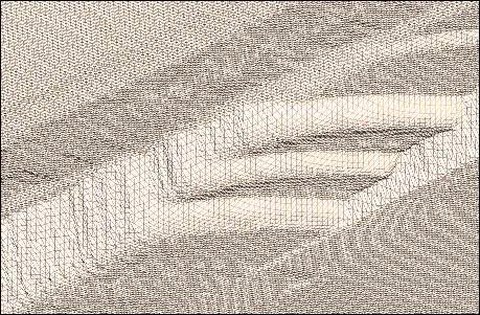
Abb. 2: Ausschnitt Tagebau (Beispiel)
Für die Datenreduktion ist ein Verfahren entwickelt worden, das ausschließlich im 2D- Bildbereich arbeitet. Dazu wird das 3D- Modell segmentweise in Höhenbilder konvertiert, Abb. 3.
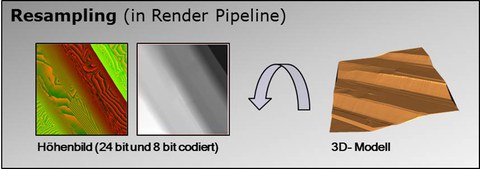
Abb. 3: Konvertierung der Datenbasis 3D-> 2D
Ziel ist es, lediglich Punkte hoher Krümmung zur Erzeugung des reduzierten 3D- Modells zu verwenden. Dazwischen liegende Bereiche werden durch die Triangulation der Punkte abgedeckt.
Projektinhalt
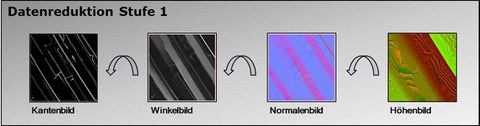
Abb. 4: Datenreduktion Stufe 1
Das Verfahren selbst arbeitet zweistufig. Zunächst werden für jedes Tagebausegment markante Punkte extrahiert, Abb. 4. Die Beschreibung der Tagebauoberfläche ausschließlich durch diese Punkte führt üblicherweise zu einem sehr ungenau reduzierten Modell. Daher werden in einem zweiten Schritt dem reduzierten Modell gezielt weitere Oberflächenpunkte hinzugefügt, Abb. 5.
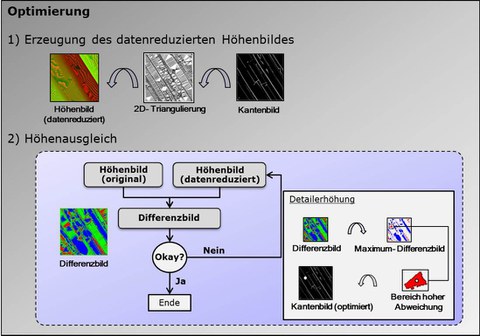
Abb. 5: Datenreduktion Stufe 2
Ergebnis
Durch das Verfahren konnten Reduzierungen auf ~2% der originalen Datenmenge erreicht werden. Der dabei akzeptierte Fehler in den Höhenwerten beträgt ±10 cm.