Strukturentwicklung (CAx)
Laufzeit | 01.09.2016 – 28.03.2019 |
Gesamtprojekt | Funktionale Geometriestrukturen (FunGeoS) für generative Fertigungsverfahren |
Finanzierung | BMBF |
Projektleitung | Dr.-Ing. habil. Christine Schöne (ehem. Mitarbeiterin) |
Bearbeiter | |
Dr.-Ing. Matthias Klaus (ehem. Mitarbeiter) | |
Partner | Citim GmbH |
S.K.M. Informatik GmbH | |
Fraunhofer Institut für Fertigungstechnik u. Angewandte Materialforschung | |
Fraunhofer Institut für Keramische Technologien und Systeme | |
Fraunhofer Institut für Werkstoff- und Strahltechnik | |
Fraunhofer-Institut für Werkzeugmaschinen und Umformtechnik | |
Laserinstitut Hochschule Mittweida | |
3D Microprint GmbH | |
CIM-TTS GmbH Wismar | |
FKT Formenbau und Kunstsofftechnik GmbH | |
Institut für Luft- und Kältetechnik, gemeinnützige GmbH | |
Volkswagen AG | |
Robert Bosch GmbH | |
LASERVORM GmbH | |
Mathys Orthopädie GmbH | |
SITEC Industrietechnologie GmbH |
Motivation
Das Anliegen besteht in der Etablierung einer Prozesskette für den konstruktiven Entwicklungsprozess, die es Konstrukteuren in ihrem Umfeld erlauben soll, funktionale Geometriestrukturen zu erzeugen und zu berechnen und wiederum zu modifizieren. Adressiert werden dabei lasttragende und fluidführende Strukturen, die mittels generativer Verfahren hergestellt werden sollen. Dabei soll auf etablierte Konstruktionsprogramme und Simulationswerkzeuge mit den bekannten Schnittstellen im CAx-Umfeld Bezug genommen werden.
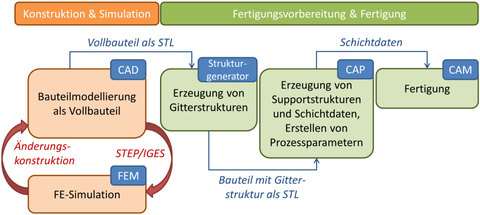
Gegenwärtiger Stand der Technik bei der Strukturerzeugung
Zielsetzung
Für den Werkzeug- und Formenbau gilt es insbesondere die Hybridbauweise aus konventionell hergestellten Grundkörpern mit additiv-generativ gefertigten Einsätzen zu ergänzen, die mit Strukturen zur konturnahen Kühlung ausgestattet werden. Eine Erhöhung der Standzeiten der Werkzeuge soll damit erreicht werden. Dazu sollen im CAD-Umfeld Softwarewerkzeuge zur automatisierten Ermittlung der Trennebene und zur effektiven Konstruktion von Kühlkanälen konzipiert und umgesetzt werden.Gitterstrukturen werden heute fertigungsnah generiert. Diese gilt es künftig bereits im Konstruktions- (CAD)- und Simulationsumfeld (CAE) zu berücksichtigen um Bauteile gerade belastungsgerecht zu konstruieren und auslegen zu können. Neben regelmäßigen Gitterstrukturen für technische Bauteile (Greifer-Demonstrator) bei denen eine Volumen- und Gewichtsminimierung um 50% favorisiert werden, sind gradierte Strukturen aufzubauen um bei medizinischen Produkten (hier Implantatdemostrator) eine individuelle (Patientenspezifische) Anpassung der Steifigkeit zu erhalten.Um die o.g. Ziele zu erreichen gilt es geeignete Softwarewerkzeuge zu konzipieren , umzusetzen und zu erproben. Da diese Softwarewerkzeuge sind weder für CAD noch für CAE und CAP (Arbeitsplanung) bisher etabliert sind, sollen diese nun für den gesamten Produktentwicklungs- und Herstellungsprozess erarbeitet und umgesetzt werden und bilden das Gesamtziel des Teilprojektes.