Cooling of Additive Manufactured Turbine Blades
Cooling of Additive Manufactured Turbine Blades
Project director: | Prof. Dr.-Ing. habil. Ronald Mailach |
Research Associate: | Dipl.-Ing. Andreas Türke |
Funding: | DFG |
Duration: | 05/2023 - 04/2026 |
Funding code: | MA 4922/12-1 |
As the availability and applicability of additive manufacturing technologies increases, novel designs and an extended parameter space for cooling systems in gas turbine blades, which are exposed to high thermal loads, can be explored. With the knowledge obtained from numerical and experimental investigations, design guidelines for future cooling systems shall be improved. Therefore, the influence of various design parameters on heat transfer, flow field and thermal performance is assessed in a model test rig of a single passage cooling channel with turbulators.
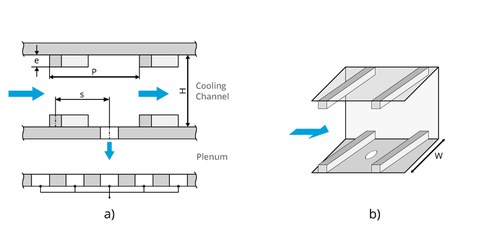
a) Diagram of cooling channel with rib turbulators und b) perspective view
An important aspect in the additive manufacturing of turbulators is the increased surface roughness, which can be influenced by varying process parameters. This can be beneficial for heat transfer, but also increase pressure loss. From the experimental investigation, correlations for heat transfer and thermal performance for rough cooling channels, rib turbulators with small pitch and blockage, as well as the effect of film hole extraction shall be derived.
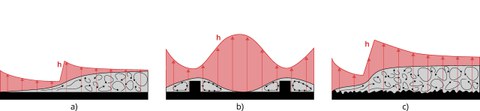
Distribution of heat transfer coefficient h at a) smooth channel, b) channel with turbulators and c) rough channel
Besides experimental investigations, numerical simulations are an important tool in the design process of cooling systems. By solving the Reynolds-averaged Navier-Stokes equations (RANS) to determine heat transfer, major deviations between experiment and simulation can be observed compared to Large Eddy Simulations (LES). On the other hand, LES is usually not applicable for extensive design studies and automatic optimization due to tremendous computational effort. By comparing the results of both methods, the strengths and weaknesses of RANS models shall be assessed and suggestions for improvement derived.