Wood moulding
Idea
It is a widespread opinion that wood is an easy material to process. The opposite is true, however! In fact, you can easily saw, plane and shape wood with little force and energy. The cutting material treatment is, however, far less economic in comparison to non-cutting manufacturing technologies, such as rolling, casting, shaping, deep drawing and extrusion. This procedure requires a high elongation at break, which can be increased applying heat. Wood with an elongation at break of only about one percent is too brittle for this process.
Moulded wood technology is based on a new understanding of the material: It considers wood as a cellular substance that can be compressed by heat (140 °C) and pressure (5 MPa), whereby the cell walls fold together. Of no less importance, but currently of no technical use, is the fact that the cell structure, given an appropriate process regime, can be pulled apart and be fixed completely. Thus, an elongation at break of 100% can be achieved, representing an increase of two orders of magnitude.
The cell structure of the wood allows a new approach as "foam-like" material, which can now easily be treated. Coniferous and deciduous trees are equally suitable. The procedure has been developed by the Institute of Steel and Timber Construction and has been patented. It has a unique selling proposition worldwide.
Manufacturing process
Image video IKU-Award © Fraunhofer
Based on these considerations, massive boards made of densified spruce are produced at the Chair of Timber Engineering and Construction Design, which are then formed into profiles, under the influence of heat and humidity. The folding of the cell walls is thus reversed. The radius of curvature of the profile depends on the previous densification. At a densification ratio of 50%, the inner radius of curvature must not be lower than the wall thickness of the profile. In principle, all kinds of developable forms in any longitudinal and transverse dimensions can be produced.
Moulded wooden tubes can subsequently be reinforced with high-performance fibres. This compound opens up new opportunities for wood in civil engineering and architecture but also in the lightweight and plant construction. In order to improve the environmental properties, synthetic fibres can be replaced by natural fibres. The tensile strength of the wood's inherent cellulose fibre is almost comparable with that of glass fibre. In further process steps, it can even be converted into a carbon fibre.
Areas of application
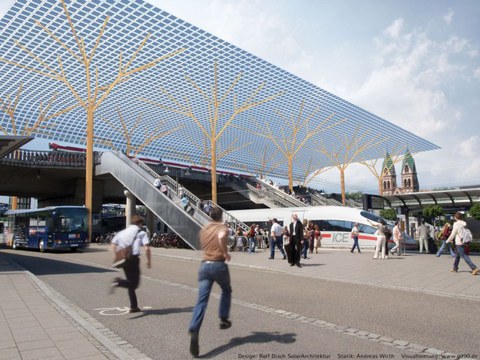
Projektentwurf Solardach Freiburg mit Formholz-Verbundrohren
The moulded wood tubes cannot only be used in a load-bearing but also in a leading function, especially for the transport of aggressive media. In view of the high strength of the fibres, construction tasks can be realised, which are nowadays still reserved to energy-intensive materials. Synthetic fibres, as for instance carbon fibres, have a higher strength than metals: With only one fifth of the mass they achieve the twentyfold material strength. In combination with the inexpensive, but nevertheless firm wood, construction units are developed, whose price and functional characteristics are suitable for all construction tasks. Apart from reinforcement, textile armouring represents an effective protection against atmospheric conditions, so that outdoor applications show a significant improvement of durability and the life cycle analysis turns out more favourable. For the better evaluation of the load-bearing capacity, please note the following example: The load-carrying capacity of a tube support made from moulded wood (length: 260 cm, diameter: 30 cm, wall thickness 2 cm) amounts to about 600 kN (which corresponds to a mass of 60 tons). An additional glass fibre reinforcement of only 750 grams (!) increases the load-carrying capacity to 1200 kN, namely the double! The materials value of the moulded wood tube amounts to about EUR 15, with a net mass of 30 kilograms. These numbers underline the technical potential, but also the economic efficiency, which the resource wood displays in alliance with high technology. For a sustainable development, it is essential to expand the technical usage of wood beyond the boundaries of architecture and construction industry to other areas. Examples include lightweight construction and interior works, furniture, plants, masts, towers, machines, containers, packaging, drums and reels, transport and automobile and yacht construction and many others.
Ecology and environment
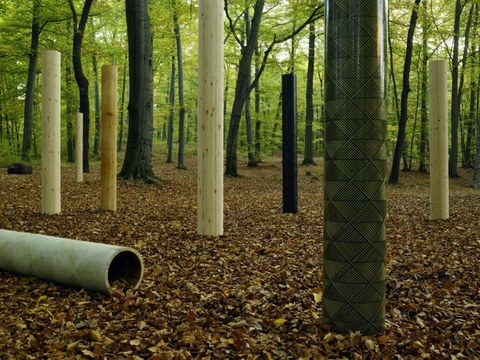
Formholzrohre mit textiler Bewehrung
With view of the eventual output, the one-dimensionality of the sawing technology favours linear tree species. In the course of reforestations, this gave preference to coniferous woods in relation to location-typical deciduous tree species, whose large crowns are used for inferior industrial wood and firewood. Moulded wood demands little forest mass and thus supports the near-natural silviculture. All indigenous tree species can be used, even parts of the crowns. Also densely wooded developing countries can profit from this development, since their deciduous forests have remained near-natural and feature bent trunks, which can serve as load-bearing parts and substitute energy-intensive materials.
Fast-growing tree species, such as poplar, which are harvested after only ten years in short rotation plantations, are perfectly suited for the production of large sized moulded wood tubes. Economic and ecological criteria of agro forest plantations are presently the subject of complex investigations. The processing of wood into moulded wood tubes opens new sources of income for farmers.
The use of energy during the moulded wood production is – compared to other materials – so small that necessary costs are practically negligible. The heat value of the saved wood and the process energy are a clear proof of the potential of moulded wood technology. Contrary to the irreversible mechanical defibration in the production of timber materials, for which electric energy of low efficiency from primary energy must be made available, in the moulded wood production, the process heat can be recovered via heat exchangers. Used moulded wood can materially and thermally be recovered and recycled.
Savings regarding waste and profile formation alone amount to up to 80% of the initial raw wood. The efficiency improvement of moulded wood can be calculated as follows: Avoidance of waste in the sawmill - factor 2; profile formation - factor >4; Use of densified wood - factor >2; Use of flawless wood - factor >2. If all these factors are summarised, it results in a quadruple load-carrying capacity, even without reinforcement and with only an eighth of material employment.
Honours and awards
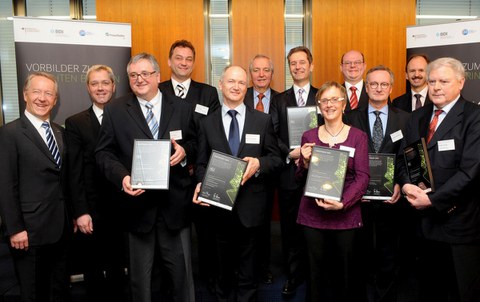
Innovation Award for Climate and Environment - winners 2009
The moulded wood technology was honoured several times with renowned awards. Here is a selection:
- GHTC-Award 2013 - Category: Light-Weight Design
http://www.research-in-germany.org/en/campaigns-and-activities/ghtc-award/2013-lightweight-design-v2/haller.html - MATERIALICA Design & Technology Award 2011 - category: CO2-Efficiency
http://www.materialica.de/index.php?id=333&L=0%2Fhtml%2Fprogramm.html - “Selected Landmark in the Land of Ideas” 2011
http://www.land-der-ideen.de/365-orte/preistraeger/extrastabile-formholzprofile-tu-dresden - Innovation Award for Climate and Environment (IKU-Award) 2009
http://www.iku-innovationspreis.de/iku-innopreis/preistraeger/2009/kategorie-3-2.php - NoAE innovation Award 2008
http://www.noae.com/fileadmin/inno2008/wag_inno_29.pdf - Collano – Innovation Award 2007
- Wilhelm Klauditz Award 2006