Multiscale Material Modeling
Fiber-reinforced composites still offer opportunities for considerable improvement of their properties. A better understanding of the interaction between their constituents by means of multiscale methods can be used to realize their full potential in saving weight, resources and energy as well as to introduce them to new areas of application.
Any material is composed of structures on different length scales, its macroscopical properties governed by lower scales. Typically the characteristics of fiber-reinforced plastics are influenced by the properties of the fiber, the polymer and the interface between them as well as the arrangement of the fibers. These effects can be studied on three length scales.
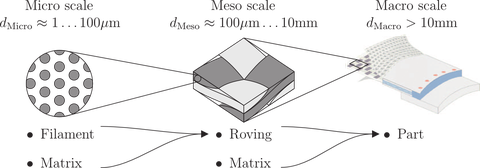
Three length scales typically investigated for fiber-reinforces composites
Local Material Modeling
On the microscale the interaction between filaments and polymer matrix is investigated. Nonlinear and inelastic effects are of interest especially in the polymer matrix. At higher loads also damage has to be accounted for, especially in the fiber-matrix interface. The choice of the utilized material models and the identification of their parameters is done according to experiments.
When studying failure using representative volume elements, attention should be paid to the boundary conditions used. They might induce or inhibit the localization of damage at certain points of the volume element, resulting in different predictions of the effective material properties.
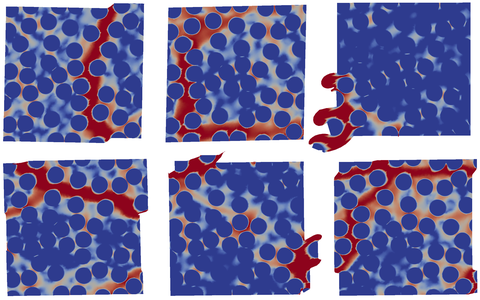
Distribution of the continuum damage parameter in six volume elements with different boundary conditions but otherwise identical conditions
In addition to investigations concerning the pure composite material, the failure of composite-metal joints is of interest during the development of innovative lightweight hybrids. The comprehension of the interactions between adhesive failure of the polymer-metal interface and the cohesive composite failure enables the design of a load-optimised surface structure. Based on a developed model of a representative interface element, the effects of different interface geometries on the effective interface behaviour are studied.
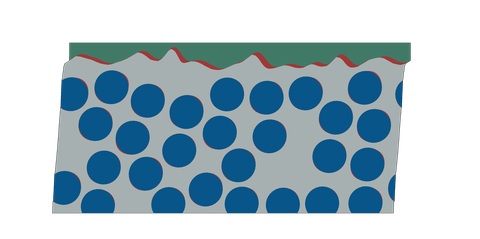
Respresentative interface element composed of a metal and a composite phase. Depending on the pre-treatment of the metal surface, the resulting interface may have a certain geometric structure.