Units
Metallographic Laboratory
Diverse polished samples are prepared in the metallographic laboratory for investigation in optical and scanning electron microscopes. However, the main focus of the microstructure characterisation is on metallic materials (Fe-, Cu-, Al-, Ni-, Ti-basis). Extensive experience has been developed for the handling of materials that pose difficult challenges with regard to preparation and microscopy (e.g. thin films, foils, powder metallurgic preparations, various composites). The picture acquisition and analysis software in the laboratory facilitates the qualitative as well as quantitative analysis of the microstructure. Microstructure preparation has at its core the interrelation of material, technology and microstructure properties.
Head
Ms Dr.-Ing. Veneta Schubert
Head of the Metallographic Laboratory
Send encrypted email via the SecureMail portal (for TUD external users only).
Professor for Material Technology
Professor for Material Technology
Visiting address:
Berndt-Bau, Room 217 Helmholtzstraße 7
01069 Dresden
Equipment
- Wet separation grinder - ATM
- Cold mounting with vacuum impregnation and / or pressure vessel hardening
- Warm mounting press - Jean Wirtz, Struers
-
Various sanding and polishing machines - Jean Wirtz, Buehler -
for the manual and semi-automatic preparation of polished samples - Vibration polishing machine
- Microstructure development via dip etching, etch polishing or electrochemical etching
- Stand macro-photography - Nikon
- Stereo-microscope - Nikon, enlargement 3.75:1 up to 150:1
- Digital-microscope - Keyence, enlargement 20:1 up to 200:1 and 100:1 up to 1000:1
- Various optical microscopes - Carl Zeiss, Nikon – for the investigation of polished samples in bright field mode, in dark field mode, in polarised light or as the case may be by differential interference microscopy, enlargement 25:1 up to 1000:1
- Picture acquisition and analysis software - Keyence and Nikon - for single object measurements, layer thickness determination, as well as point, area and line analysis on metallographic polished samples and digital pictures
Laboratory for Mechanical Material Testing
In the laboratory for Mechanical Material Testing a diverse range of materials are tested for their statistical and dynamic stability, hardness, ductility and rigidity. Metallic materials form the focus of the investigations. Extensive experience exists in the implementation of standardised tests as well as in the handling of particularly difficult to measure materials (e.g. thin films, foils, powder metallurgic samples, various composite systems). A particular highlight in the laboratory is the available equipment for hardness testing. They allow hardness measurements to be made across the macro-, micro- and nano-range. The determination of the mechanical characteristic values is always in overview related to the interrelation of material, technology and microstructure properties.
Head
Senior Engineer
NameMs Dr.-Ing. Birgit Vetter
Head of the Laboratory for Mechanical Material Testing
Send encrypted email via the SecureMail portal (for TUD external users only).
Professor for Material Technology
Professor for Material Technology
Visiting address:
Berndt-Bau, Room 21/17 Helmholtzstraße 7
01069 Dresden
Equipment
- Static tensile test machine - Zwick (load range: 2.5 kN up to 100 kN, warm chamber up to 250 °C, mechanical and optic length change measurement)
- Servo-hydraulic test machine - Instron (load range: up to 100 kN)
- Macro hardness measurement equipment (Brinell, Vickers, Rockwell)
- Small load measurement equipment - Zwick
-
Micro hardness measurement equipment - Leco, Shimadzu, Uhl (VMHT Auto)
HV0.001 – HV2, HK - Nano-indenter - Asmec, Unat (Test load up to 2000 mN, max. measurement depth up to 150 µm)
- - Charpy impact test equipment
- Measurement microscope
- Digital microscope - Keyence, enlargement 1:1 up to 50:1
- Ultra-sound measurement equipment
- Slot grinding machine - Asmec, KSG 110
Laboratory for High Temperature Oxidation
In the laboratory for High Temperature Oxidation isothermal investigations are made of the reactivity of various materials with oxygen and the oxidation kinetics in a temperature range up to 1400°C. Furthermore, fully automated cyclic oxidation tests can be made up to a temperature of 1000°C. Both methods can be run in a duration mode for multiple weeks.
Head
N. N.
Equipment
- Precision scales - Mettler Toledo - (max. 41 g (0.01 mg); max. 120 g (0.1mg))
- Drying oven - Binder – up to 300°C, 400 l volume
- Cyclic oxidation oven - Xerion Advanced Heating Ofentechnik GmbH - (fully automatic up to 1000°C, argon and nitrogen atmospheres also possible)
- Isothermal oxidation oven - Nabertherm (max. 1400°C, argon and nitrogen atmospheres also possible)
Laboratory for Particle Erosion
In the laboratory for Particle Erosion erosively worn samples are characterised by the material removal caused by solid-state particle currents. The test rig facilitates the replication of complex wear exposure scenarios that are due to the impact of the erosion particle on the component surface. The influence of the particle size and the resulting kinetic energy delivered to the surface on the erosion performance of the material is dependent on a number of factors that can be systematically varied in the test rig.
Head
N. N.
Equipment
- Particle erosion rig (up to 300 m/s particle velocity, diverse abrasive material (corundum, glass balls) various particle distributions, impact angle from 15 – 90° adjustable in 5° steps, X-Y moveable sample holder, max. sample size of 100 x 100 mm, precision powder feeder 1-10 g/min (±1.5 %), particle image velocimetry (PIV), tests in accordance with the standard ASTM G76-07 possible)
Laboratory for Additive Manufacturing
Selective electron beam melting (SEBM) is a powder based process for the generative manufacture of complex three dimensional parts. For this a powder bed is layer-wise selectively melted by an electron beam. The process is undertaken in a vacuum.
In addition to the testing of the material properties, it is important to obtain knowledge about the geometrical dimensions, as well as the material and pore structure, of the generative manufactured components in order to comprehensively characterise the part. In the centre for additive manufacturing (AMCD) the Chair of Materials Technology at the TU Dresden operates X-ray based measurement methods (X-ray macro-structure (2D) and micro-CT (3D)) with a minimal resolution of up to 3 μm.
Head
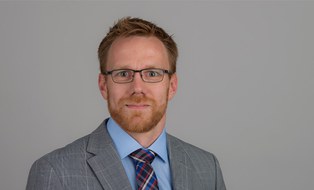
Mr Dr.-Ing. Axel Marquardt
Leitung des Labors für additive Fertigung
Send encrypted email via the SecureMail portal (for TUD external users only).
Professor for Material Technology
Professor for Material Technology
Visiting address:
Berndt-Bau, Room 211 Helmholtzstraße 7
01069 Dresden
Equipment
- ARCAM A2X
- Max. part size 200 mm x 200 mm x 380 mm
- Max. beam power 3000 W
- Min. beam diameter 250μm
- CT-measurement system YXLON FF35 CT (YXLON International GmbH):
- Y.FXE 225.48 reflection tube:
- Voltage < 225 kV,
- Power < 320 W,
- Resolution ≤ 4 μm, TXI
- Detector YXLON Panel 2530:
- 16 Bit detector
- active area 249 mm x 302 mm
- Test part:
- Size (Ø x H) 300 mm x 500 mm
- Maximum weight 30 kg
- Y.FXE 225.48 reflection tube:
- X-ray macro-structure Y.MU2000-D (YXLON International GmbH)
- Y.TU 225-V01 X-ray tube
- Variable spot from 250μm / 290 W to 800 μm / 1600 W,
- Voltage < 225 kV
- Resolution: 70 μm
- Tilt angle of ray path* ± 30°
- Detector Y.Panel 0822-16 HDR premium
- 16 Bit detector
- Test room for radioscopy
- (Ø x H) 600 mm x 900 mm
- Part weight 60 kg
- Y.TU 225-V01 X-ray tube