Measurement and simulation of static and dynamic bearing behaviour of internal gear motors and pumps
Research Task/Objectives
Internal gear hydraulic machines are widely used in nearly all industrial and mobile applications because of their simple but efficient and low noise design. Especially for their application in electro-hydraulic compact drives, the crossing of operating limits leads to a need for the evaluation of the bearing characteristics using experiments and simulation tools as well, Analytical calculations do not deliver enough information and precision of the results at stability limits. CFD-simulations are precise enough, but the calculation times exceed all acceptable limits.
Approach
The static and dynamic bearing behavior was experimentally analyzed with eddy-current sensors. Based on these data, the well-known mobility method for journal bearing was adopted for the specific properties of internal gear machines. The hydrodynamic and hydrostatic pressure distributions are calculated with the method of finite-differences and an analytical network-model, respectively. Thus all static and dynamic behavior of the internal gear radial bearing can be analyzed with sufficient accuracy over the whole operating range as well as for all dynamic operating cycles in calculation times of a few minutes.
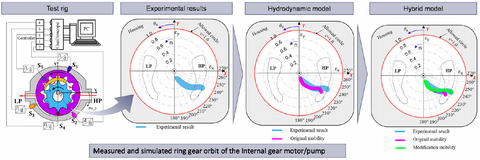
Comparison of experimentaly and computational analysis of the bearing charakteristic for steady loading
The work was made possible with a scholarship „Vietnam International Education Development“ (VIED) provided by the Vietnamese Ministry of Education and Training.