Tribology optimization of pump systems through manufacturing-oriented application of mesostructures
Objectives
Due to the rise in electrification of hydraulic systems, hydrostatic pumps experience a new challenge in terms of operating speed. Especially in the low-speed range, pumps must be able to hold loads without running into mixed friction and thus component wear. Today, some pumps can still withstand these conditions, mainly because they use leaded metals in their sliding bearing. However, these are to be replaced by lead-free materials in the future to comply with European regulations (Reach Regulation). The aim of the research project is to optimize the hydrostatic-hydrodynamic bearings of an axial piston pump for low speeds and thus low relative speeds of the bearing pairs, which will occur increasingly in the future.
Approach
Using a simulation-based design process, industrially manufacturable surface modifications are made to the slipper sealing surfaces to support hydrodynamic pressure buildup without impairing hydrostatics. Surface modifications suitable for series production are planned in the meso area. In addition, these structures are to be investigated with regard to their effect on minimizing the running-in phase of the slippers, so that lead-containing materials can be dispensed with in these sliding partners in the future. In addition to the pump test rig, the structured components will be validated on a tribometer converted for hydrostatic testing.
Results
The two best structures, a ±6 µm wave and a 6 µm step design, were subsequently manufactured and tested using near-series production lathes. The sliding shoes were compared with an unstructured sliding shoe design also designed and optimized in the simulation. This represents the best possible design without surface structures and already outperformed the standard pump slipper in terms of efficiency and wear.
As a result, the stepped slipper performed best. It achieved an overall efficiency improvement of 6 percentage points at full stroke, and 16 percentage points at 25% swash plate angle, both at low operating pressures and speeds. At the same time, overall efficiency did not deteriorate at any operating point, even at corner power (350 bar, 2300 rpm). For electrification, the start-up torque is particularly important, and the step slipper was able to reduce this by 80% at 1 rpm without generating more leakage. After a 500 h endurance test, less than 1 µm of the 6 µm step wore off, which means that this design has virtually no wear other than in the surface roughness. This made it possible to test a lead-free slipper that was at no point inferior to the leaded slipper and also survived the 500 h endurance test with less than 1 µm wear.
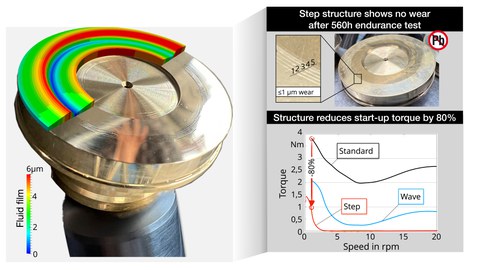
Lead-free structured slippers reduce start-up torque and wear
This IGF Project 20757 BR/1 and BR/2 of the research association Forschungskuratorium Maschinenbau e.V. was supported via AiF within the programme for promoting the Industrial Collective Research (IGF) of the Federal Ministry of Economic Affairs and Climate Action (BMWK), based on a resolution of the German Parliament.
The final project report can be obtained from Forschungskuratorium Maschinenbau e.V. (mailing address: Lyoner Str. 18, 60528 Frankfurt am Main, E-Mail: info@fkm-net.de).