Energy efficiency of displacement controlled hydraulic presses
Research Task/Objectives
Due to the high flexibility of hydraulic deep drawing presses regarding the adjustability of position and force curves, these machines can be used for a wide range of production tasks in sheet metal forming. Despite of high throttle losses, valve control is the standard especially in the die cushion drive of conventional hydraulic press machines today.
The objective of the project was the investigation of the potentials of displacement
controlled drives with focus on reduced energy consumption. The research activities were based exemplarily on a modern test machine.
Approach/Results
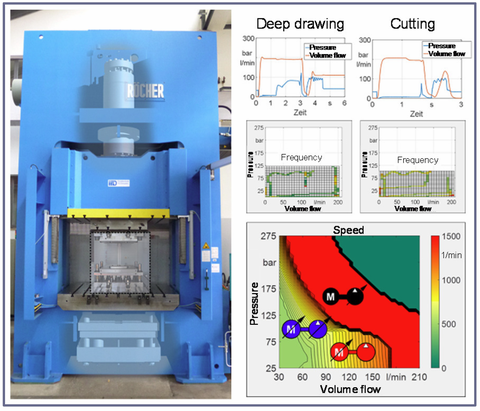
Test machine, example processes and energetic optimum control strategy for the speed of the motor-pumpunit in the slide drive
After an experimental analysis of the components of slide and die cushion drives, the component losses were modelled and control strategies were developed. The models of the motor-pump-units were integrated into an existing, experimentally validated machine model. Afterwards, the energetic properties of different types of displacement control were analysed and evaluated.
For the slide drive of the test machine energy savings of up to 5 % could be proofed when using optimized displacement controlled drive architectures. For the die cushion an even higher reduction of the energy consumption of up to 40 % was possible, which was mainly the effect of energy regeneration.
Based on the simulation results a methodology was developed, which allows the application-specific selection of the appropriate type of displacement controlled drive
architecture for hydraulic presses.
The project 17739 BR was financed and supervised by the Research Association Mechanical Engineering – FKM, Lyoner Straße 18, 60528 Frankfurt am Main. In the scope of the Programme to promote Industrial Collective Research it was funded by the German Federation of Industrial Research Associations (AiF) with means of the Federal Ministry of Economic Affairs and Energy (BMWi) on the basis of a decision by the German Bundestag.