Thermo-energetic optimization of cooling circuits in frame structure
Research Task/Objectives
High manufacturing precision and low energy demand are decisive requirements for modern machine tools. Through the application of mineral concrete for molding machine tool frames opens up considerable potential for the integration of cooling circuits close to the heat source. The aim of this project is the thermo-energetic optimization of cooling
circuits so that the thermal stability and consequently the manufacturing precision can be improved (minimization of thermo-elastic deformations). The challenge in adapting the cooling system are the temporally variable thermal loads as well as the controlling of complex three-dimensional heat flows in the frame.
Approach/Results
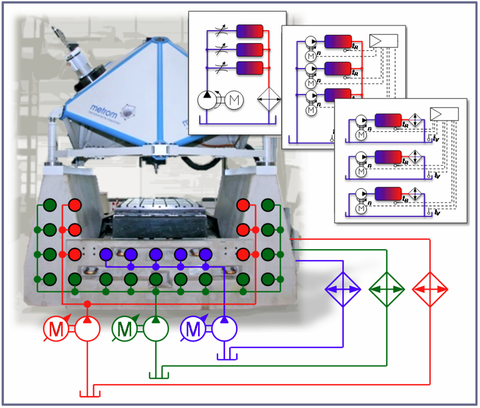
Frame structure and cooling circuits with decentralized pumps
Originating from an existing frame structure, FEM-, CFD- and network-models for the description of thermo-energetic and thermo-elastic behavior are developed and validated experimentally on the basis of temperature and displacement measurements. These calculation models can be used to optimize the temperature control system. The system includes the structure and positions of the cooling circuits in the frame structure as well as the control of the supply with the cooling medium. The optimized design of temperature control system is implemented using a concrete example. The resulting new improved demonstrator serves to verify the optimization method.
The presented research activities are part of the project SFB/Transregio 96 “Thermo-energetic design of machine tools“ (subproject T02). The authors would like to thank the German Research Foundation (DFG) for the financial support.