Automated commissioning of variable-speed linear drives in closed loop
Research Task/Objectives
The dynamics of hydraulic drives are dominated by the attached load mass, the oil volumes of the cylinder chambers and the effective bulk modulus of the oil. Consequently, there is a need for process-dependent controller parametrization. Drives with displacement control, e.g. electro-hydraulic compact drives (ECD), have low self-damping. In addition, inherent nonlinearities such as the pressure dependence of the effective bulk modulus have a significant influence on system behaviour. These factors additionally complicate the practical controller design and lead to a high time requirement during commissioning of position-controlled hydraulic linear drives. EKAs with their closed oil circuit and integrated design have only one electrical and mechanical interface, so that these drives can be easily and quickly installed in machines. In order to enable the Plug&Produce capability of ECDs, an automated commissioning assistant is required on the control side.
This assistant essentially consists of parameter identification, controller parameterization and controller adaption. During parameter identification, the system parameters of the corresponding drive model are determined. Subsequently, suitable controller parameters are calculated by using the parameterized model. Due to changing ambient conditions, such as operating temperature or wear, the system parameters vary. By the adaption of the variant parameters, a constant control behavior can be guaranteed.
Approach/Results
Known methods for parameter estimation, controller design and adaptation of valve-controlled drive systems are transferred to displacement-controlled systems, examined and evaluated. Subsequently, the preferred methods are combined to an overall algorithm. This algorithm is implemented and validated on a practical machine control system.
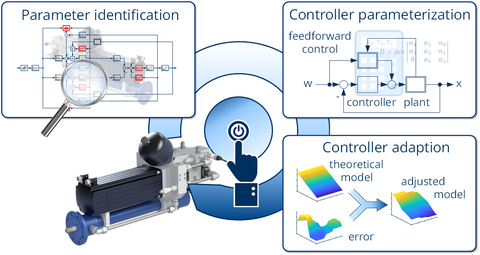
Main aspects of the development of an automated commissioning assistant
The presented research activities are part of the project " Automated commissioning of variable-speed linear drives in closed loop " (Ref. No. FKM Nr. 704420). The authors would like to thank the Fluid Power Research Fund of the VDMA for the funding and support.