Hydraulically actuated local flow control for blades of wind turbines
Research Task/Objectives
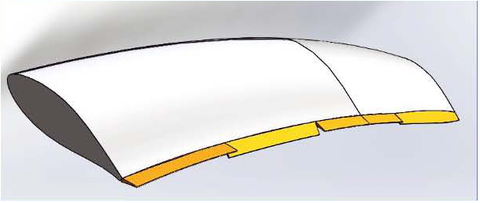
Flaps for local flow control of a wind turbine blade
The limited number of attractive sites for wind turbines causes the development of
longer blades. Fatigue loads, which are induced by dynamic wind loads (gusts) and tower passing, significantly limit the lifetime of these components.
The project aims at the development of a hydraulically actuated flap for the trailing edge of a wind turbine blade, facilitating dynamic local flow control. The flap system shall reduce the consequences of dynamic wind loads working on the blade structure and thereby leading to longer lasting blades or reduced production cost.
Major challenges of the project are the linking of the flap to the blade, components lifetime under given harsh environmental influences, and lightning protection of the overall system.
Approach/Results
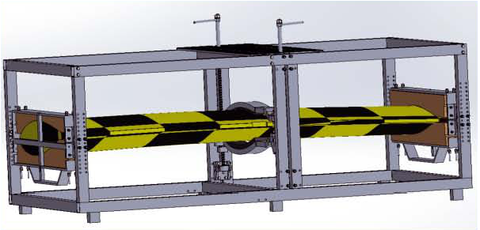
Design concept of a test rig
The interdisciplinary collaboration of four project partners from polymeric material science, blade development, blade construction/repair/°optimization and fluid power aims at the development of a fluid-actuated trailing edge flap for a 44 m blade of a 1.5 MW wind turbine. The development is going to be tested on a prototype. A test rig, specially developed for systematic longtime testing, is developed to show strengths and weaknesses of the developed concept.
The presented research activities are part of the project " Developmet and implementation of a hydraulic actuator system for a trailing edge flap in blades of wind energy turbines" (Ref. No. KF2452606HM4), which was funded by the German Federal Ministry for Economic Affairs and Energy within the ZIM programme.
The project was realized in cooperation with Leibniz Institute for Polymer Research Dresden, WindNovation GmbH and cp.max Rotortechnik GmbH.