Thermo-energetic design of fluid power systems in machine tools
Research Task/Objectives
In regards to functional and design aspects, fluid power systems interact with a variety of
machine tool components, and are therefore an important control element for the thermoelastic behavior within the complex machine structure. However, concerning thermo-energetic and economic issues, the increasing complexity, performance and energy demand of fluid power systems have to be critically examined.
The developed network-based calculation models and the achieved experimental results
of the first project phase show that there is considerable potential by improving the heat transfer of fluid power components, and that a compensation and correction of thermo-elastic deformations of machine tools require innovative system structures, that allow local and process dependent tempering of machine subsystems.
Approach/Results
In the first project phase, thermo-energetic calculation models and tools for the fluidic
temperature control systems have been developed and verified. On this basis, the second
project phase utilizes these models to optimize the heat transfer and fluid system structures, as well as to develop process and demand-oriented control strategies in order to provide design recommendations for thermo-energetic efficient components and systems. An essential aspect regarding minimal thermo-elastic deformations is the optimal tempering of the structures of machine tools while minimizing the energy demand and thus, the operating costs.
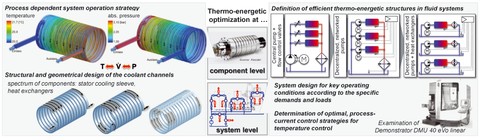
Objective of the second project phase in the SFB/TR 96, subproject A04 “Thermal Fluid Engineering”
The presented research activities are part of the project CRC/Transregio 96 "Thermo-energetic design in machine tools" within the subproject A04 „Thermal Fluid Engineering“. The authors would like to thank the German Research Foundation (DFG) for the financial support.
Funded by: