Increase of process stability by iterative learning control
Research Task/Objectives
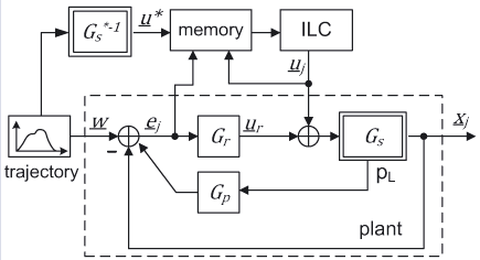
Structure of Iterative Learning Control
Model based control features good tracing accuracy. However, the quality strongly depends on the accuracy of the modelling and parameters.
The obtainable tracking accuracy is strongly influenced by changes of operation condition. In conventional closed loop control deviations are corrected after they have already occurred.
Approach/Results
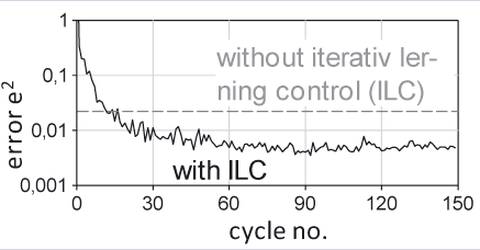
Cyclic minimisation of process errors
Iterative learning controllers (ILC) use information of elapsed circles for a “forward-looking „control. The smaller occurring deviations in between the circles, the better ILC works. In cooperation with the Georg-Simon-Ohm-University of applied sciences Nuremberg ILC controllers for injection- and clamping unit of an injection moulding machine have been developed and applied.
The results prove that process stability and constancy can be significantly improved.
Hereby the betterment is solely reached by the use of information on the process structure and its parameters for a feed-forward control without any influence on process stability.