Sensors
Flexible Tactile sensor based on 3D printed moulds
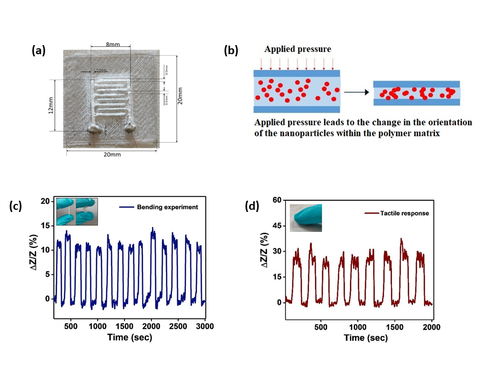
Figure: a) Final product with its dimensions b)The working mechanism c)Response of the ZnO/PDMS-based sensors towards oscillatory bending of the sensor d) Response of the ZnO/PDMS-based sensors towards tactile sensing.
This work highlights the implementation of flexible sensors formed using 3D printing moulds. The 3D printing process, being one of the state-of-the-art techniques, has been used to generate moulds. These moulds were subsequently used to develop the sensors with zinc oxide (ZnO) and polydimethylsiloxane (PDMS) as the processed materials. These two materials were considered due to their low cost, easy processing and enhanced electromechanical characteristics. The developed prototypes were characterized to determine their electrical performance with respect to mechanical deformations. The results for these sensors are promising and form a podium to use to form full-integrated tactile sensing systems.
Figure (a) and (b) represents the fabricated sensor and its working mechanism. Figure (c) shows the response of the sensors with the two positions given in its inset. The relative impedance values were reduced when the sensors were bent. This happens because as the sensors are bent, there is an increase in the effective connection between the nanopowder in the electrodes. This increases the overall current, thus reducing the impedance values. It is seen that the output was stable enough for the fourteen cycles. This result proves that the orientation of the ZnO nanopowder reverted back to its original position when the pressure was released every time. The sensors were then tested for tactile sensing applications as shown in Figure (d), where pressure was exerted on the sensing area of the prototypes. The pressure and contact area were kept almost constant during the entire process. Gloves were worn during the tactile process to negate the dielectric effect on the skin. Similar to the bendability test, the relative impedance values were reduced when the pressure was applied to the sensor. Due to the interdigitated electrodes, the glitches present in the response were caused as a result of the capacitor fringing effect. This effect can be seen more in the case of co-planar design as compared to the conventional parallel-plate capacitors. Further work would be done on the electromechanical characteristics of the sensors and their application for tactile sensing applications.
Mitarbeiter
NameMr Aniket Chakraborthy M. Tech.
Send encrypted email via the SecureMail portal (for TUD external users only).
Professur für Akustik und Haptik
Professur für Akustik und Haptik
Besucheradresse:
Barkhausenbau, Raum BAR 77A Helmholtzstraße 18
01062 Dresden
None
Flexible Piezoelectric Sensor for Acoustic Application
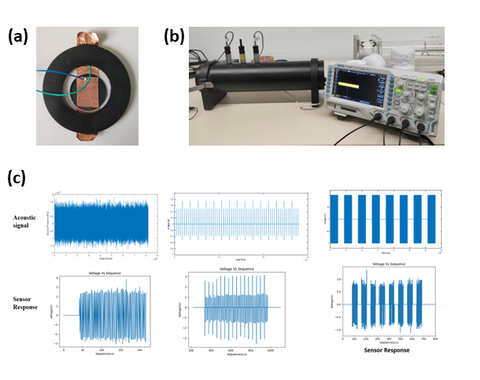
Figure a)Sensor bonding with 3D printed circular support to fit inside the impedance tube. b) The experimental setup. c) The voltage response of the sensor for different acoustic signals.
The aim of the work is to develop novel flexible sensors for acoustic applications. The sensors have been fabricated using Zinc oxide (ZnO) and reduced graphene oxide (rGO) nanomaterials. These nanocomposites are promising excellent piezoelectric properties and can respond well to vibration and acoustic signals. Some of the primary attributes of these sensors are their high mechanical flexibility, reproducibility, and stability in their responses. As a proof-of-concept, the prototypes have been tested with various acoustic signals with different frequencies. While the prototypes were connected to the end of the acoustic impedance tube for testing purposes, the sound pressure causes the piezoelectric response. The experimental data has been studied for the sensor’s stability, sensitivity, and repeatability. A facile and low-cost fabrication process can yield mass production of these piezoelectric sensors for acoustic applications.
The piezoelectric sensor has exhibited an excellent response to various acoustic signals with different frequencies. The response of the sensor was measured as ~2.5 V and ~3.0 V for white noise and click track acoustic signals respectively. It was perceived that the sensor response was stable and repeatable.
Hence the proposed rGO/ZnO-based piezoelectric sensors are most suitable for acoustic applications.
Mitarbeiter
NameMr Dr. Suresh Nuthalapati
Send encrypted email via the SecureMail portal (for TUD external users only).
Professur für Akustik und Haptik
Professur für Akustik und Haptik
Besucheradresse:
Barkhausenbau, Raum BAR 77A Helmholtzstraße 18
01062 Dresden
None