Aerodynamic
The field of aerodynamics for aerospace engineering includes the investigation of various fluid mechanical effects, but also the development of systems to increase the efficiency of future wings and aircraft configurations. The Chair's wind tunnel provides excellent conditions for experimental investigations under controlled conditions. Numerical flow simulations (CFD) are also used to validate a problem. Our Chair focuses on the engineering application of CFD software. In addition, the simulation offers the possibility to investigate flow problems for which an experimental approach is difficult. Our research topics include
- the measurement of airfoils in the wind tunnel
- the characterization of aircrafts in wind tunnels and free flight tests
- the simulation of flow effects using CFD tools
- the investigation of fuel behavior in tanks for launch vehicles and satellites using numerical analysis
Topics:
The Chair of Flight Mechanics and Flight Control currently offers the following topics for student research projects and theses. If you are interested, please get in touch with the contact person for the relevant topic. Please refrain from multiple requests.
Most measuring instrumentation used in wind tunnels must be calibrated before use. While this requires only a few support points for pressure sensors, for example, and can be largely automated for flow probes, the calibration of balances for up to six components is carried out in a fairly extensive manual process. Because several parameters have to be varied and entered manually, the procedure is quite error-prone. Above all, however, the existing, historically grown software is completely outdated and partly no longer executable on the existing systems.
In this initial situation, it seems appropriate to redesign the calibration procedure and harmonize it with the current Python-based measurement program. After a basic familiarization with the topic and the structure of the measurement chain for aerodynamic force measurement, the existing material would first have to be viewed and systematized. Based on the analysis of the existing program parts, a new algorithm in Python is to be developed. Particular attention should be paid to possible sources of error, their avoidance and correction options. Furthermore, proposals for a sensible addition to the equipment should be worked out.
Contact person
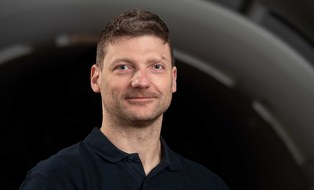
Research Assistant
NameDipl.-Ing. Jürgen Frey
Send encrypted email via the SecureMail portal (for TUD external users only).
If you are still unsure about your topic, we are also happy to offer general advice. Alternative options can also be presented based on the student's individual interests. We are also happy to support student theses with industry partners or initiative topic suggestions from students. The contact person for aerodynamic projects is:
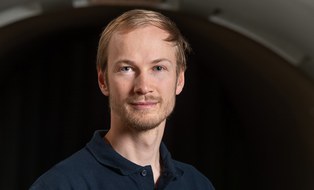
Research Assistant
NameDipl.-Ing. David Nölle
Send encrypted email via the SecureMail portal (for TUD external users only).