Concluded projects
ASCenSIon
ASCenSIon was an Innovative Training Network funded by the European Commission in the frame of Horizon 2020, whose goal was to contribute to a sustainable and independent space access for Europe. To achieve this, a consortium of 24 partners ensured that 15 doctoral students were trained to become outstanding specialists in their field and gained a comprehensive understanding of the complexity, multidisciplinarity and internationality of launch vehicle development. The acronym stands for “Advancing Space Access Capabilities – Reusability and Multiple Satellite Injection”, and it well describes the focus of the project to research on several areas of space access. The three main research areas of the project were propulsion technologies and their reusability, Guidance, Navigation and Control (GNC), and aerothermo-dynamics of re-entry and safe disposal. The core of the project were the 15 Early Stage Researchers (ESRs), talented PhD students of different disciplines, nationalities and ages who were enrolled in different countries across Europe and employed within the project for maximum 36 months. The ASCenSIon consortium was coordinated by the Technische Universität Dresden and the project culminated and concluded in a dedicated conference in Dresden 2023.
MACARONIS
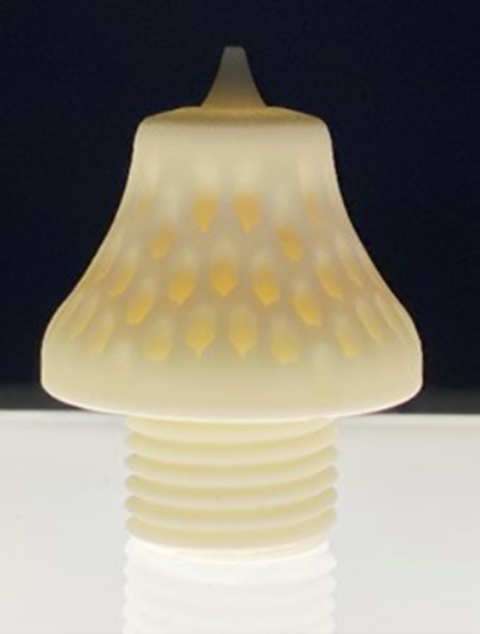
ceramic aerospike nozzle
As part of the project "MAnufactured Ceramic AeROspike Nozzle In Space" (MACARONIS), which was funded by the state of Saxony with ERDF funds, additively manufactured ceramic aerospike engines were investigated for use in cold gas propulsion systems for satellite applications. This was done by numerical simulations as well as by numerous experiments and a propulsion system demonstrator. The use of additive manufacturing opens up completely new application forms and fields for many materials, as well as new potentials for increasing performance and reducing mass. Among other domains, this is absolutely essential for the technology driver aerospace technology. The great interest of aerospace technology in additively manufacturable ceramics is due to a large number of advantageous material properties such as low density, high heat resistance and high strength. In this joint research project between the Institute of Aerospace Engineering (ILR) at TU Dresden and the Fraunhofer Institute for Ceramic Technologies and Systems (IKTS), these advantageous characteristics of additively manufactured ceramic components were transferred to a propulsion concept for satellites. Within the project, a cold gas satellite propulsion system with a ceramic nozzle was developed, which can be experimentally explored in future space missions. This development was implemented in the form of a propulsion demonstrator using nitrogen as the working gas. Aerospike engines researched at the ILR served as the basis for the developed propulsion system.
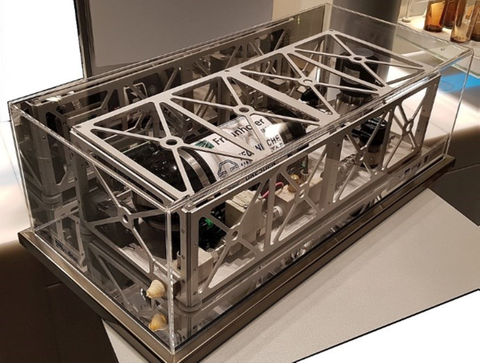
Demonstrator for the cold gas propulsion system with ceramic, additively manufactured aerospike nozzle
CFDµSAT
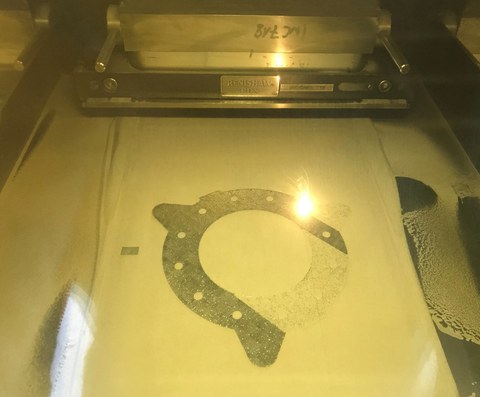
Engine components during manufacturing via LPBF
Within the CFDµSAT project, the additive manufacturing of metallic components for rocket engines was investigated as part of the Agent3D program (funded by the German Federal Ministry of Education and Research within the innovation campaign Zwanzig20). The focus was on injector heads and cooling channels for novel engine concepts. The overall process chain considered in the project for the manufacturing of complex fluidic components comprised the design, additive manufacturing using laser powder bed fusion (LPBF), post-processing of functional surfaces, quality assurance and testing. The use of simulations and experimental investigation of individual structures supported the design of the final components. Structures manufactured by LPBF have relatively high surface roughness and shape and position tolerances, which initially do not meet the requirements of many fluid technology applications. For this reason, the post-processing methods of abrasive flow machining (AFM) and laser drilling were investigated in order to refine internal channels on the one hand and to introduce fine holes in a defined manner on the other. At the end of the project, based on the knowledge gained, an aerospike engine was additively manufactured using LPBF, together with the cooperation partners of the Fraunhofer Institute for Material and Beam Technology (IWS) and the Institute of Materials Science (IfWW) of the TU Dresden, which will be used for future test campaigns.
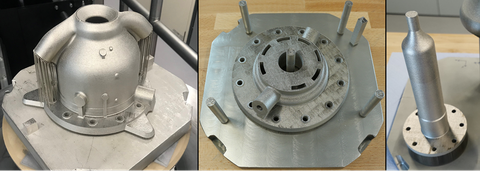
Additively manufactured engine components
ACTiVE
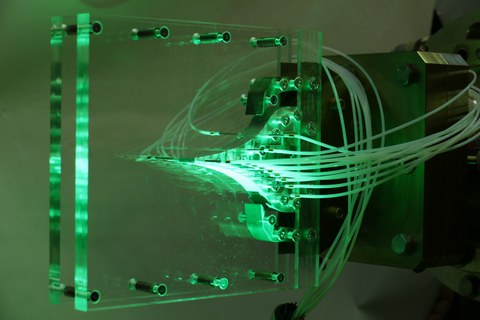
Investigation of secondary injection with a linear aerospike nozzle at DLR Lampoldshausen
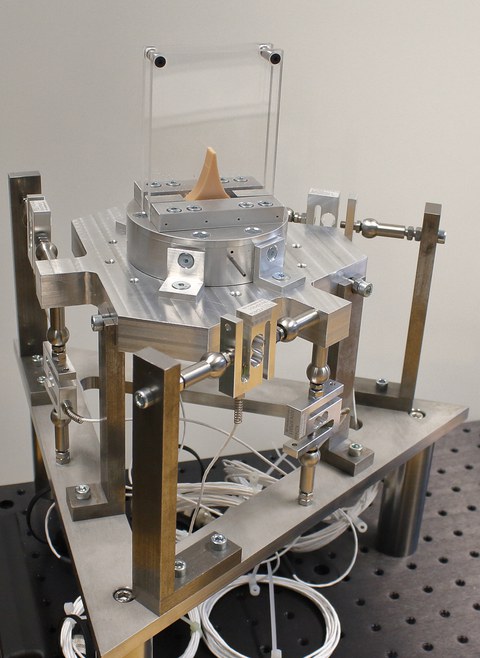
Nozzle mount with 6-axis force measurement and integrated linear aerospike nozzle
In the project "AerodynamiC Thrust VEctoring" (ACTiVE), funded by the state of Saxony, aerospike engines with aerodynamic thrust vector control were investigated. This was achieved both by numerical simulations and by means of numerous cold gas experiments. Aerospike engines with aerodynamic thrust vector control are an innovative engine design with high application potential for a variety of spacecraft. Examples include the use in upper stages of launch vehicles and in satellites for orbit and attitude control. The Space Transportation research group is investigating this innovative engine technology in order to understand the wider applicability in the space industry. The advantages of aerospike nozzles over conventional bell nozzles are numerous: increased performance potential due to continuous adaptation to the ambient pressure, thus improved propellant utilization, a compact and highly integrated design, and mass savings due to simplified integration. The aerospike nozzle concept with aerodynamic thrust vector control was investigated in various cold gas test setups in order to characterize the parameters influencing the generation of thrust and steering forces. For this purpose, a cold gas nozzle test rig was set up at the Chair of Space Systems to measure the force generation of a large number of additively manufactured nozzle variants. In further experiments, the pressure distribution on the nozzle surface was measured on a larger test rig in cooperation with the DLR Institute of Space Propulsion in Lampoldshausen. Based on these investigations, engineering models were then developed to describe the nozzle flows, and promising applications were tested for their feasibility. The project was unique in Europe and was able to open up new fields of research and application for Saxony's industrial and research landscape. As a result, three follow-up projects were launched at the beginning of 2020 and, building on the ACTiVE project, a 500 N aerospike engine was additively manufactured by the Fraunhofer Institute for Material and Beam Technology (IWS). This engine was investigated in 2019 as part of a hot gas test campaign by the Space Transportation research group.
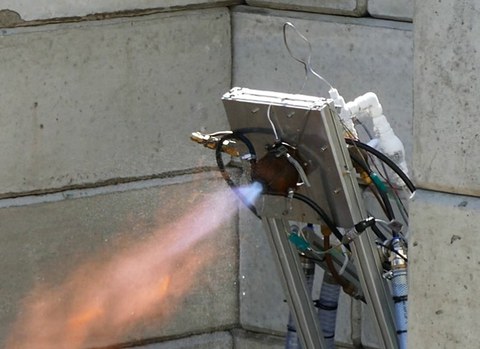
Hot fire test of the aerospike engine manufactured in cooperation with the Fraunhofer IWS
Polaris Aerospike concept study
POLARIS is developing reusable multi-role spacecraft based on initial concepts developed by the German Aerospace Center (DLR e. V.) in 2015-2018. Specific features include aircraft-like takeoff and landing on conventional runways and the ability to autonomously change mission bases. Reusability and airplane-like operations lead to potential cost reductions compared to conventional missiles and enable greater responsiveness, flexibility, and safety for launch systems. The horizontal launch spacecraft under development at POLARIS offer a multi-mission capability that covers various commercial and defense mission scenarios, including satellite launches, orbital cargo transport, and future manned spaceflight. Within the project "Rapid Deployable Reconnaissance System" (RDRS), a concept study for POLARIS was conducted within the Space Transportation Systems Research Group to investigate the suitability of aerospike engines for such multi-mission spacecraft. Aerospike engines appear to be of particular interest for such vehicles with a diverse altitude profile due to their continuous adaptation to changing ambient pressures.
SMART-Rockets
Based on the funding program STudentische Experimental-RaketeN (STERN) of the German Aerospace Center (DLR), a number of students from different semesters developed a small sounding rocket as part of their studies at the TU Dresden. Notably, is has been the only project within STERN that dared to develop a rocket with liquid propellants. In this project, called SMART-Rockets, a wide range of students were familiarized with the topic of small rockets and all their subsystems, which in turn are closely resembling those of large launch vehicles. This gave them a complete system-wide overview of a complex technological system, from design to quality control. In the course of the project, a transportable test stand for a combustion chamber with a thrust of 500 N was also designed, manufactured and validated. On this test bench, the students learned how to handle the fluids liquid oxygen (LOX), liquid nitrogen (LN2) and ethanol and developed and qualified a new type of injector with an associated combustion chamber. Although the launch of the planned MIRA rocket could not be realized within the project, the entire propulsion system and a variety of other components were finalized as part of SMART Rockets.
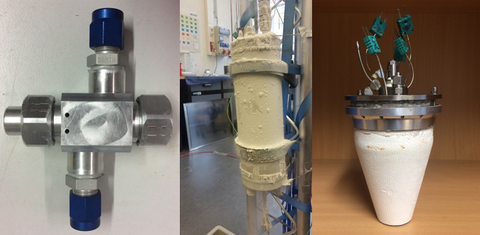
In-house developments within SMART-Rockets: pyrotechnic valve (left), propellant tanks for LOX (center), thrust chamber made of graphite and ceramic materials (right)