Hydrostatic bearings for offshore-application
Research Task/Objectives
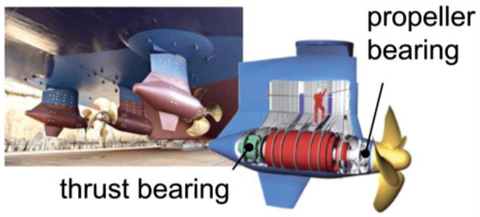
Cruise liner with pod-drives
Pod-drives are gaining ground from conventional drive concepts in applications like icebreakers and cruise liners. Ships with pod drives have a significantly higher maneuverability as the pod-drives’ thrust can be vectored around 360 degrees. But this leads to a significant influence from one pod to the other. This influence causes big, highly dynamic load forces on the propeller shaft bearings.
Currently used roller bearings are not able to withstand these load forces for a long time and fail early on.
Thus, it was necessary to develop a sustainable propeller shaft bearing, which considerably extends maintenance intervals of the drive. Basic requirements are long life cycles, robust design and operation of the bearing as well as good emergency running properties.
Approach/Results
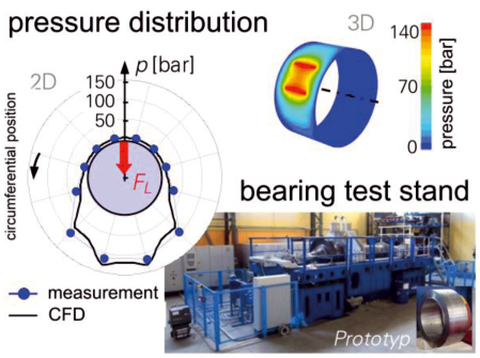
Methods for investigation of the bearings
To develop a sturdy bearing for different operating conditions, the advantages of hydro-static and hydrodynamic bearing concepts were combined in one bearing. To simulate the combined bearings’ internal flow, new calculation concepts had to be developed, in which computational fluid dynamics (CFD) played the most important role. The bearing concepts where compared and evaluated with extensive numerical simulations. Based on these concepts, a bearing prototype was designed and evaluated on a high-performance bearing test stand. Thus, the numerical models were validated, and the functionality of the new bearing concept was proven.
This research was funded by the German Federal Ministry of Economic Affairs and Energy (Ref. No. 03SX245A). The authors are responsible for the content of this publication.