Real-time simulation for testing the function of drive and control systems
Research Task/Objectives
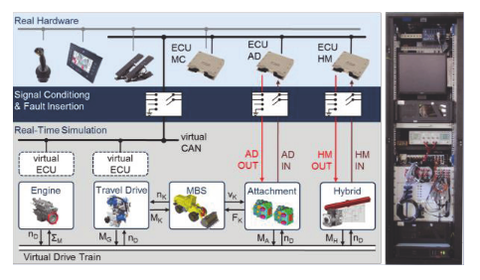
Hardware-in-the-Loop test bench
The importance of testing especially safety-critical functions of modern drive and control systems is continuously growing. Therefore, the used Hardware-in-the-Loop test benches require real-time capable calculations of simulation models. An increased level of detail improves the test validity, but the model complexity is growing as well.
Small and medium sized manufacturers avoid the great effort in building appropriate models, and do not take advantage of this technology. Supporting the generation of real‑time capable simulation models of complex hydraulic drive and control systems is the major research objective
Approach/Results
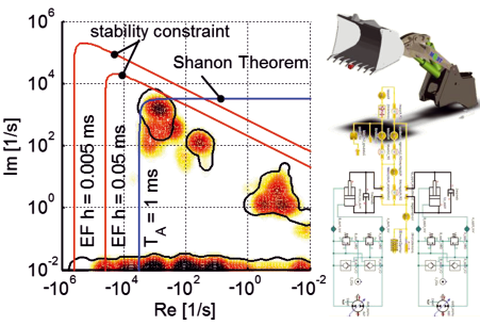
Example of the analysis for an attachment model
In order to achieve this, it is necessary to develop methods that systematically reduce the effort and contribute to an efficient use of HiL-test bench applications.
First, the requirements of real-time simulation need to be determined. Based on relevant frequencies of the controlling unit, the system analysis detects real-time critical model elements. It allows the identification and elimination of computationally intensive model descriptions. The usage of special integration methods shall also contribute to fulfilling the real-time demand. The realization and testing of industrial demonstrators shall verify the feasibility of this approach.
The article is based on the joint project proFAST (process-efficient real-time-simulation for testing the functions of drive and control system) financed by the European Regional Development Fund (ERDF). |