System pressure level in mobile machinery - system characteristics and potentials
Task / Objective
Increasing the available system pressure in hydraulic drives offers the potential to increase the power density, reduce weight and oil volumes and thus save installation space and resources or use them more efficiently. Apart from mobile traction drives, which currently work with system pressures of up to 450 bar, there are no known series applications in mobile hydraulics in which higher system pressures are used. The research project aims to systematically work out what challenges an increase in the system pressure level entails, whether there is an ideal pressure level from a technical and/or economic point of view, where the hurdles lie in the application and what measures should be taken to overcome the current restrictions.
Solution approach
Based on the application scenarios and requirements, applications are selected for which an increase in system pressure is expected to bring benefits. The main challenges posed by increasing the pressure level are first analyzed in general terms and later in relation to the specific application. An increase in system pressure and the resulting effects are analyzed on the basis of an application defined in collaboration with the working group accompanying the project. Analysis tools and test benches are designed and implemented for the key aspects of energy and weight savings, installation space, component availability and application limits of the pressure medium.
Results
The analysis of weight and installation space shows that a system pressure level of 500 to 700 bar can be considered desirable from a technical point of view. This enables weight savings for control blocks, cylinders and pressure fluid and is associated with moderate cost increases through the use and processing of higher-strength steels. For the cylinder as an essential actuator in mobile hydraulic applications, the investigations show that there is an ideal pressure level between 200 bar (area ratio 1:1.1) and 450 bar (plunger), depending on the area ratio of cylinders but independent of the cylinder power, at which the lowest possible cylinder mass is achieved for simple steels(σ=235 MPa). When using higher-strength structural steels(σ=500 MPa), the ideal pressure range is between approx. 400 and 900 bar.
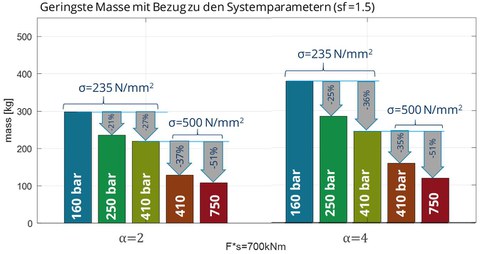
Mass savings as a function of pressure level and cylinder material for area ratio α=2 and α=4, safety factor sf=1.5, force F, cylinder stroke s
In contrast to considerable mass savings in cylinders, laminar flow situations that can be achieved by increasing the pressure do not make a significant contribution to efficiency; the reduction in viscosity due to the influence of temperature remains the decisive influencing factor, well ahead of the reduction due to the influence of pressure, which, however, must be taken into account at pressures above 500 bar. The test rig developed to analyze the viscosity of pressurized fluids at pressures of up to 3500 bar was successfully put into operation. It allows the viscosity of a wide range of hydraulic fluids to be analyzed.
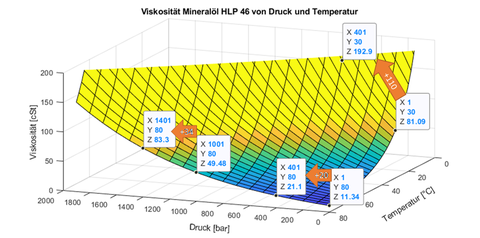
Viscosity (Z) of a standard mineral oil as a function of pressure (X) and temperature (Y)
Using the example of a comprehensive non-linear simulation model of a 40-ton handling device, further aspects of the system pressure increase are analyzed in a practical manner. The influences developed in theory can be confirmed in the simulation. The weight saving on the cylinders achieved by increasing the system pressure reduces the hydraulic energy consumption in realistic handling cycles by approx. 5%.
This pre-competitive project (funding code 21840 BR /1) was funded by the Federal Ministry of Economics and Climate Protection (BMWK) with funds from the Industrial Collective Research (IGF).
Duration: 01.05.2021 - 31.01.2025
The final report of the project can be obtained from the Forschungskuratiom Maschinenbau e. V. (http://www.fkm-net.de) (postal address: Lyoner Str. 18, 60528 Frankfurt am Main, e-mail: info@fkm-net.de).