Identification for hydraulic die cushions
Research Task/Objectives
During the process of deep drawing in a single- action deep drawing press the blank is
clamped between slide and blank-holder. The blank-holder force is applied by the hydraulic die cushion and has a major influence on the drawing process. Therefore the press-operator sets highest standards towards dynamic and static behavior of the die cushion. Due to the complex and non-linear behavior of the hydraulic die cushion and its numerous parameters, the initial set-up process is a costly and time-consuming process that requires experienced staff.
The aim of the current research is to find an algorithm for automatic model identification
and control parameter computation that should be implemented in an industrial production press. The developed algorithm must be able to automatically determine the optimal control parameters and to adapt these to a changing system behavior. The algorithm is implemented within the presses control systemm and will significantly reduce the set-up time, improve control quality and include an automatic parameter adjustment during ongoing operation.
Approach/Results
The research is conducted in close cooperation with TRsystem as part of a ZIM-funded
project. The basis for the algorithm forms a system model of the deep drawing press that was simplified in order to be implemented within the control system of the press. At the same time, this model needs to simulate the die cushions behavior sufficiently. Its model parameters are to be identified automatically with adequate algorithms. This fully parameterized and validated system model will then be used to automatically determine the optimal control parameters with the help of analytical methods.
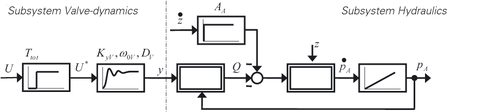
Simplified system model of the die cushion with the subsystems Valve-dynamics and Hydraulics
The presented research activities are part of the project Ref. No. KF2452605LP3, which was funded by the German Federal Ministry for Economic Affairs and Energy within the ZIM programme.
The project was realized in cooperation with the company "Trsystems GmbH".