Offers, Institutions and equipment
Table of contents
General offers
- Training, consulting and system introduction for reverse engineering and virtual reality
-
Loan of projectors, displays and VR technology such as glasses and various input devices
-
Preparation for trade fair appearances
Contact person | |
Dr.-Ing. Wolfgang Steger |
CAD Laboratory
The CAD Laboratory is a central facility of the Faculty of Mechanical Science and Engineering. It is subordinate to the Chair of Virtual Product Development.
Contact person | Dipl.-Inform. Ralf Städtler |
Product Lifecycle Management and Systems Engineering Lab (PLM-SE Lab)
The PLM-SE Lab deals with issues relating to concepts of product lifecycle management (PLM) and model-based systems engineering (MBSE). On the one hand, product data is to be managed effectively and efficiently over its entire lifecycle and the consistency of the product model is to be ensured through defined processes. On the other hand, MBSE methods are used to make information accessible within the submodels of a product.
In the PLM - SE Lab, methods and tools are made available in an integrated environment in order to provide product information at the right time, in the desired quality and sequence.
The integration of the systems engineering approach offers extended possibilities for describing systems on the basis of the product model. In addition to simple description models with SysML, the MBSE methodology and its tools are used to describe comprehensive system models.
Laboratory offers
- Integrated design review with several CAD workstations and VR
- Visualization of PDM metadata and product structures in VR
-
Development of additional functions in CAx and PDM
- Development of MBSE models
- Integration of MBSE and PLM
- Interfaces from MBSE tools to simulation tools
Laboratory equipment
- Interactive planning tools for data management processes
- Software used: Aras Innovator, SOLIDWORKS, Enterprise Architect
Contact person | |
Dipl.-Ing. Maximilian Peter Dammann | |
Dipl.-Ing. Bin Lin |
Reverse engineering laboratory
The reverse engineering laboratory has various 3D scanning technologies and powerful software for processing scan data for sophisticated research and services.
Laboratory services
- 3D scanning, 3D digitization
- 3D data and 2D image processing
- Evaluation of scan and CT data
- Customized software for user-specific tasks
- Data preparation for FEM and production engineering applications such as additive manufacturing and milling
- Design applications in the medical environment (implant planning, design of individual implants)
- Quality control and measurement tasks
- Establishment and optimization of reverse engineering process chains
- System implementation and consulting
- Training courses on reverse engineering
Laboratory equipment
3D scanner:
- Zeiss ATOS Q system with GOM ScanCobot (measuring fields 100x100 and 500x500)
- ARTEC LEO
Photogrammetry system:
- GOM TRITOP
3D microscope:
- Alicona Infinite Focus SL (5x and 10x objective)
Software:
- Zeiss Reverse Engineering
- Gom Inspect Professional
- Polyworks
- Geomagic DesignX
- Geomagic Wrap
- Own software solutions
Contact person |
Our software
For the analysis and visualization of CT and DVT data in various formats, we provide you with a free demo version of our viewer. This enables the import of uncompressed DICOM data, image stacks or RAW data. Isosurfaces can also be generated using marching cubes and exported as STL files.
(Attention: The resolution of the images in the demo is limited to a maximum of 512 x 512 pixels. A maximum of 200 slice images can be loaded simultaneously).
Here you can find a collection of CT sample data: www.volvis.org
KTC Dicom Viewer
Download version 1.0.0.12 (.exe), Download version 1.0.0.12 (.msi)
With the KTC Dicom-Viewer it is possible to visualize slice image data with up to 200 slice images and a size of 512x512, 3D and export them in the form of an STL model. The KTC Dicom Viewer requires .NET framework version 4.0 or higher, Windows 7 (64 bit) or higher and graphics cards with OpenGL version 3.3 or higher.
KTC STL Viewer
Download version 1.0.0.12 (.exe), Download version 1.0.0.12 (.msi)
With the KTC STL-Viewer it is possible to import and visualize point clouds and triangle meshes in .stl and OBJ format. The KTC STL Viewer requires .NET framework version 4.0 or higher, Windows 7 (64 bit) or higher and graphics cards with OpenGL version 3.3 or higher.
If you have any questions or suggestions, please contact us. We will be happy to develop customized software solutions for your specific problem.
Contact | |
Virtual Reality Lab
The Virtual Reality Laboratory deals with the use of virtual reality and augmented reality as components of product lifecycle management. Virtual reality is used to visualize complex spatial structures and thus enables both the visual evaluation of a product (e.g. the design of virtual prototypes) and the simulation of assembly and maintenance processes. Augmented reality is used to link virtual models and information with the real environment. Virtual data is superimposed on the stakeholder's field of vision using mobile glasses systems.
Laboratory services
- Services relating to the conception and creation of VR scenes for product presentations
- Transfer of CAD models into visualization models
Laboratory equipment
Various presentation and input devices are available for experiments in the virtual reality laboratory. A powerwall with front and rear projection technology supports preliminary investigations, especially in large discussion groups. Sophisticated projects can be continued in a 5-sided CAVE. A 3D presentation room for up to 400 people and several AR systems complete the equipment.
Visualization systems
- 5-sided CAVE with passive stereo projection system (polarization filter)
- AR workstation
- Scott study workstation (ZEU 232B): HTC Vive Pro /Microsoft HoloLens
- Scott2 study workstation (ZEU 232B): HTC Vive/Microsoft HoloLens
- Study workstation Scott3 (ZEU 232B): Oculus Rift S
- ARCore-capable tablet Samsung Tab S6, Tango Tablet
Working hours for the study workstations must be booked as required. Booking instructions
The workstations can also be used via remote access. Instructions for remote access
Input and interaction devices
- Kinect sensor, 4x HTC Vive remote controls with haptic feedback, 2x HTC Vive tracker, 2x Occulus Touch Controller, PHANTOM® Omni, data gloves, game controller, Leap Motion Controller, RealSense Camera R200
Software used
- Unity, EON® Studio, Softvise Cadmium
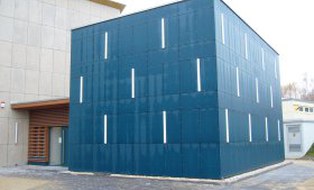
Virtual Reality Labor
Send encrypted email via the SecureMail portal (for TUD external users only).
Visiting address:
Heidebroek-Bau Nöthnitzer Straße 62
01187 Dresden
Postal address:
TUD Dresden University of Technology
TU Dresden
Fakultät Maschinenwesen
Professur für Virtuelle Produktentwicklung
01062 Dresden
Contact person | |
Dipl.-Ing. Maximilian Peter Dammann |