Entwicklung eines Systems zur Inline Prozessdiagnose im Heißsiegelprozess unter Nutzung vorhandener Prozessdaten - Intelligentes Siegelwerkzeug
Das Verschließen von Verpackungen wird i. d. R. durch Siegeln oder Schweißen realisiert, dabei wird durch Einwirkung von Wärme der Kunststoff aufgeschmolzen und kann somit eine adhäsive oder kohäsive Verbindung eingehen. Typischerweise werden dazu dauerbeheizte oder impulsbetriebene Werkzeuge eingesetzt, die mit einem Widerstandsheizelement (Heizpatrone bzw. Heizband) ausgestattet sind. Zusätzlich dient i. d. R. ein Temperatursensor zur Erfassung und Regelung der Temperatur des Werkzeugs. Diese Systeme arbeiten nach dem Prinzip hoher thermischer Masse – d. h. im Werkzeug wird möglichst viel Wärme gespeichert, sodass im Moment des Siegelns die dabei abgeführte Wärmemenge nur einen Bruchteil der gespeicherten Energie entspricht und damit die Temperatur des Werkzeugs nicht wesentlich beeinflusst.
Durch die watttron GmbH wurde ein neuartiges Heizverfahren auf Basis keramischer Technologie (cera2heat und cera2seal) entwickelt. Im Gegensatz zur konventionellen Technik wird die Wärme direkt an der Oberfläche der im Dickschichtverfahren auf keramische Substrate aufgebrachten Heizleiterstrukturen erzeugt. Die Heizleiter dienen gleichzeitig als Temperatursensor bzw. können zusätzlich dezidierte Temperatursensoren in unmittelbarer Nähe zum Heizleiter aufgebracht werden. Die daraus resultierende sehr kurze Regelstrecke und die inhärente hohe Dynamik (bis zu 7000 K/s, typ. 50-100 K/s Aufheizrate) der Heizelemente machen eine präzise und hochdynamische Temperaturregelung möglich. Zusätzlich werden üblicherweise in einem Werkzeug eine Vielzahl (bis zu mehreren hundert) von kleinen Heizleiterstrukturen eingebracht, um über die lokale Temperaturregelung eine verbesserte Temperaturverteilung zu erzielen bzw. das gezielte Einbringen von Temperaturprofilen zu ermöglichen.
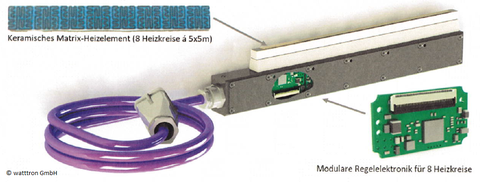
Prinzipieller Aufbau des Siegelwerkzeugs
Ziel des Projektes ist die Entwicklung einer Auswerteroutine der verfügbaren Daten des Heizsystems zur Detektion von Störstellen und fehlerhaften Siegelungen verursacht durch z. B.:
- Lage und Positionierung des Packstoffs bzw. Faltungen des Packstoffs
- Fehlen von Packstoff oder Packstoff mit größeren Störstellen oder Dickenunterschieden
- Vorhandensein von Produktresten (Kontaminationen) in der Siegelebene
- Veränderung der Packstoffeigenschaften bzw. Einsatz eines anderen/falschen Packstoffs
- Unzureichender Packstoffkontakt infolge unzureichender Werkzeugausrichtung
Um jedoch daraus möglichst eine Ursache-Wirkungs-Beziehung zwischen den messbaren Veränderungen im Prozess und den potentiellen Ursachen herstellen zu können, bedarf es neben der eigentlichen Messwerterfassung einer methodischen und „intelligenten“ Datenanalyse. Dazu stehen moderne Methoden des „Data Mining“ und Künstlicher Intelligenz (KI) zur Verfügung, die für die Aufgabenstellung angepasst werden und Anwendung finden sollen. Als Ergebnis des Projektes soll ein System (Demonstrator) vorliegen, der eine autarke Diagnose des Siegelsystems ermöglicht. Dabei sollen Diagnosen in Form von Klartext bzw. Fehlercodes auf Basis der Daten und Messwerte aus dem System generiert und an eine nächsthöhere Instanz (PLC oder IPC der Maschinensteuerung) übermittelt werden.
Projektfinanzierung:
Das Kooperationsprojekt ZF4100943PR9 wird im Rahmen des Programmes „Zentrales Innovationsprogramm Mittelstand (ZIM)“ gefördert.
Projektlaufzeit: 11.2019 – 04.2022
Projektbearbeitung und Kontakt:
Projektleitung: Prof. Majschak
Projektmitarbeiter: Norbert Bunk
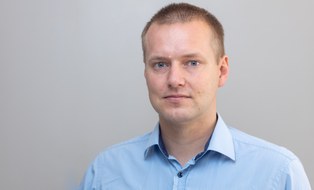
Verarbeitungssysteme
NameDipl.-Ing. Norbert Bunk
Arbeitsgebiet Fügen und Formen polymerer Packstoffe
Eine verschlüsselte E-Mail über das SecureMail-Portal versenden (nur für TUD-externe Personen).
Kooperationspartner: watttron GmbH, Fraunhofer IVV Dresden