Development of a system for inline process diagnosis in the heat sealing process using existing process data - Intelligent sealing tool
The closing of packaging is usually carried out by sealing or welding, whereby the plastic is melted by the action of heat and can thus form an adhesive or cohesive bond. Typically, permanently heated or impulse-driven tools are used for this purpose, which are equipped with a resistance heating element (heating cartridge or heating tape). In addition, a temperature sensor is usually used to record and control the temperature of the tool. These systems work according to the principle of high thermal mass - as much heat as possible is stored in the tool so that at the moment of sealing, the amount of heat dissipated corresponds to only a fraction of the stored energy and thus does not significantly affect the temperature of the tool.
watttron GmbH has developed a new type of heating process based on ceramic technology (cera2heat and cera2seal). In contrast to conventional technology, the heat is generated directly at the surface of the heating conductor structures applied to ceramic substrates in a thick-film process. The heating conductors also serve as temperature sensors, or additional temperature sensors can be applied in close proximity to the heating conductor. The resulting very short control path and the inherent high dynamics (up to 7000 K/s, typ. 50-100 K/s heating rate) of the heating elements make precise and highly dynamic temperature control possible. In addition, a large number (up to several hundred) of small heating conductor structures are usually incorporated in a mold in order to achieve improved temperature distribution via local temperature control or to enable the targeted introduction of temperature profiles.
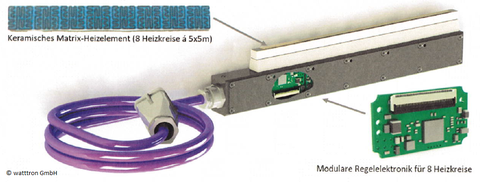
Basic design of the sealing tool
The aim of the project is the development of an evaluation routine of the available data of the heating system for the detection of defects and faulty seals caused by:
- position and positioning of the packaging material or folding of the packaging material
- Absence of packaging material or packaging material with major imperfections or differences in thickness
- Presence of product residues (contamination) in the sealing level
- Change of the packaging material properties or use of a different / wrong packaging material
- Inadequate packaging material contact due to insufficient tool alignment
However, in order to be able to establish a cause-and-effect relationship between the measurable changes in the process and the potential causes, a methodical and "intelligent" data analysis is required in addition to the actual recording of measured values. For this purpose, modern methods of "data mining" and artificial intelligence (AI) are available, which are adapted and applied to the task at hand. As a result of the project, a system (demonstrator) is to be available which enables an autonomous diagnosis of the sealing system. Diagnoses in the form of plain text or error codes based on the data and measured values from the system are to be generated and transmitted to a next higher instance (PLC or IPC of the machine control).
Project funding:
The cooperation project ZF4100943PR9 is part of the program "Zentrales Innovationsprogramm Mittelstand (ZIM)”.
Project duration: 11/2019 – 04/2022
Project management and contact:
Project leader: Prof. Majschak
Projekt manager: Norbert Bunk
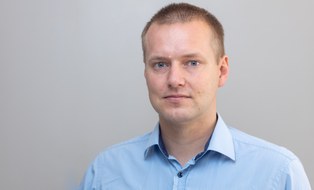
Processing Systems
NameDipl.-Ing. Norbert Bunk
Sealing and Forming of polymer Packaging Materials
Send encrypted email via the SecureMail portal (for TUD external users only).
Cooperation partners: watttron GmbH, Fraunhofer IVV Dresden