01.03.2021
LignoBraid
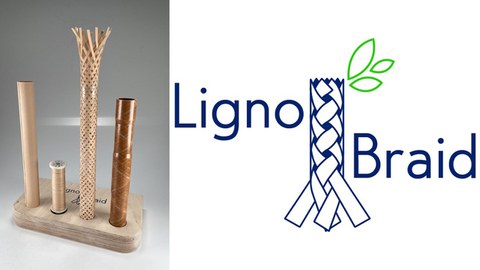
LignoBraid - Werkstoffproben und Logo
Biobasierte Leichtbau-Hohlprofile mit geflochtenen Holzbändern; Herstellung von Furnierbändern
Laufzeit |
03/2021 - 02/2024 |
Finanzierung |
BMEL | FNR |
Förderkennzeichen |
2220HV059B |
Kontakt |
|
Schlagworte |
Furnier, Nachhaltigkeit, Leichtbau, Flechttechnik |
Leichtbau ist eine der Schlüsseltechnologien für eine ressourceneffiziente und zukunftsorientierte Wirtschaft. Besonders im Bereich der Mobilität und des Transportwesens können durch hohe Leichtbaugrade maßgebliche Energie- und somit auch CO2-Einsparungen erzielt werden. Durch den Einsatz von Naturwerkstoffen wie Holz kann sowohl der Verbrauch fossiler Rohstoffe reduziert als auch CO2 im Werkstoff gebunden werden.
Vor diesem Hintergrund haben sich Wissenschaftler des Instituts für Leichtbau und Kunststofftechnik und der Professur für Holztechnik und Faserwerkstofftechnik zum Ziel gesetzt, eine neuartige Prozesskette zur Herstellung von Hohlprofilen aus Holzwerkstoff zu entwickeln. Das im Rahmen der Charta für Holz 2.0 des BMEL am 01.03.2021 gestartete Projekt LignoBraid setzt dabei bereits bei der Aufbereitung des Werkstoffs an. So möchte das Team der TU Dresden den Rohstoff Holz weitgehend in seinem natürlichen Zusammenhalt erhalten und trotzdem eine hochwertige technische Nutzung ermöglichen. Dazu sollen handelsübliche Furniere aus regional verfügbaren Hölzern zu kontinuierlichen Furnierbändern verarbeitet werden. Aus diesen Furnierbändern entstehen dann erstmals in einem automatisierten Flechtprozess beanspruchungsgerechte Preformen. Diese lassen sich anschließend durch Infusion mit biobasierten Kunststoffen zu dünnwandigen Hohlstrukturen konsolidieren.
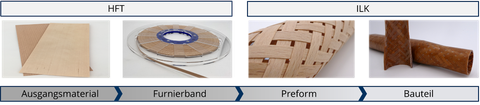
Prozesskette LignoBraid
Die so entstehenden Holzverbund-Hohlprofile erweitern aufgrund ihres einstellbaren geometrischen und mechanischen Eigenschaftsspektrums das Leichtbaupotential von Holzwerkstoffen deutlich. Durch die Nutzung regional verfügbarer biogener Rohstoffe, eine verschnittarme Herstellung der Furnierbänder sowie den Einsatz leichter und gleichzeitig hochbelastbarer Hölzer soll ein bestmöglicher Kompromiss aus ökologischen, ökonomischen und technischen Anforderungen erzielt werden. Im Ergebnis soll eine wirtschaftliche Serienfertigung von Holzverbund-Hohlprofilen unterschiedlicher Geometrien ermöglicht werden. Dadurch werden neue Anwendungsmöglichkeiten für technische Holzprodukte erschlossen und ein Beitrag im Forschungsbereich nachwachsender Rohstoffe geleistet.
Förderhinweis
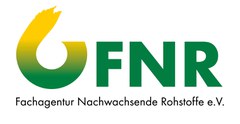
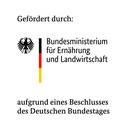