artificial aging
Fields of application
The artificial aging attempts to accelerate the course of naturally occurring decomposition processes of aging-susceptible materials. The aim of these experiments is to predict the natural aging behavior over the typical period of use of the materials. They are usually based on intensive UV irradiation, elevated temperatures and increased or fluctuating humidity, which are often combined with each other.
The artificial aging is applied to:
- the investigation of the aging stability of adhesives and film materials,
- the determination of the material compatibility of sealants and contact materials,
- the targeted damage to components.
Methods
With the climatic test chamber, climate change tests can be carried out according to DIN EN ISO 9142 and DIN EN 1279 on samples of substances and small format components. It is possible to set the temperature from -80 °C to + 180 °C and to adjust the humidity to values between 10 % and 98 % relative humidity in a range of + 10 °C to + 95 °C. Furthermore, the rapid heating and cooling rates of up to 3 K / min allow rapid temperature changes and thus accompanying high thermal stresses to be transmitted to the materials. In addition, by controlling the temperature and humidity, substance and large-format samples can be conditioned under controlled conditions.
The corrosion test chamber allows the investigation of materials under the influence of a corrosive medium. Particularly in components with metallic components, corrosion can lead to severe material changes up to the failure of an adhesive bond between different joining partners. In addition, studies on the delamination behavior of composite glasses can be made by the influence of the corrosive atmosphere.
With the SUNTEST, it is possible to subject small samples and samples of artificial aging to UV-weathering. The samples are irradiated with high-intensity radiation in a wavelength range of 280 to 800 nm with a high intensity. This stress can be combined with phases of a humidity storage. Thus, investigation into photocuring processes can be carried out by means of controlled control of the radiation intensity and the irradiation time. However, changes in the material, such as discolouration or opacity which affect the properties of the components, can also be caused by photo-induced processes.
Pure temperature storage and tests for solvent and dishwashing resistance can be carried out in a warming cabinet with a test chamber volume of 400 l. This operates in a temperature range of + 30 °C to + 250 °C. It is also possible to program different temperature programs with several ramps and holding phases, in addition to maintaining a constant temperature. Here, heat-induced delamination processes can be investigated and described. It is also possible to condition larger samples in this warming box before other tests.
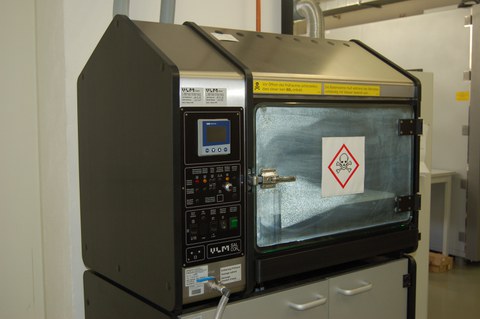
VLM Kondenswasser Prüfgerät Typ CON 300-FL AIR CWC AWRF
The corrosion test cabinet allows corrosion tests to be carried out according to DIN EN ISO 6270-2 or DIN EN ISO 6988 or comparable national and international standards. The test chamber volume is 300 l for a test chamber size of B / T / H1 / H2: 800 x 600 x 520 x 733 mm. An additional exhaust air valve, which is closed during the condensation water phase, is installed for carrying out the Kesternich-tests with SO2. After switching to the ventilation phase, this valve is opened. After a cycle has elapsed, the floor pan is emptied after opening the floor drain valve. At the start of another cycle, the floor drain valve is closed and the floor pan is filled with fresh demineralised water.