SIMS (Siemens Infrastructure Manufacturing Scheduling)
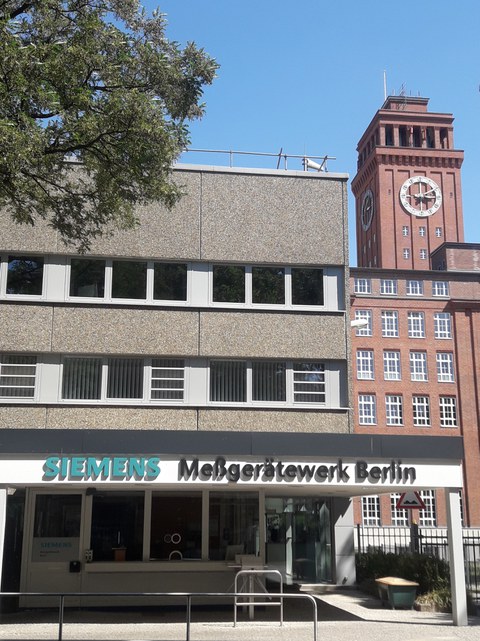
The Messgerätwerk Berlin
The Siemens Messgerätewerk Berlin (MWB) manufactures digital protection devices, automation and communication products for the intelligent transmission and distribution of electrical energy. The different devices require more than 500 different flat modules. Due to the increasing complexity of the production process, efficient manual planning is becoming more and more difficult to implement, despite extensive experience.
The aim of the project is therefore to optimize the exact daily production sequence by means of machine scheduling instruments and thus to use the existing production capacities more efficiently.
Within the project, the current production process is first mapped in the form of a digital twin in order to be able to estimate the exact effects of sequence changes. The problem is basically similar to a hybrid flow shop scheduling problem with more than 25 manufacturing stages and more than 80 heterogeneous (partly parallel) machines. Due to some special features such as:
- Re-entry of orders (reentrant)
- Different production sequences (Job Shop)
- Skip machining steps (Emergency All Machines)
- Need for assembly-specific test tools (multi-resource scheduling)
- Rescheudling
Classical approaches can only be pursued to a limited extent. Consequently, a new constructive heuristic approach was developed to solve the problem as well as possible in a short time. In further project phases, this approach was be rolled out to all assemblies and integrated into the existing software structure. Further practice-relevant data will be taken into account and the existing approach will be continuously improved.
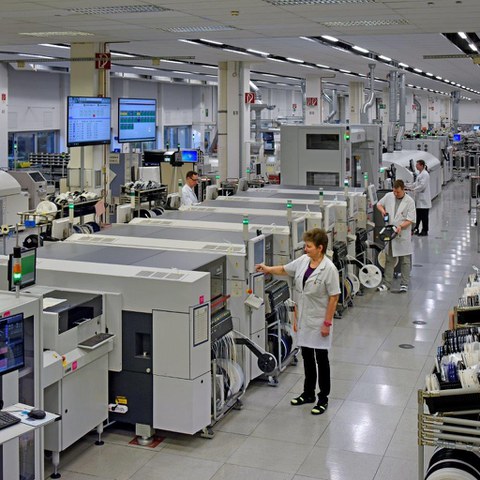
Insight into flat module production at MWB Siemens
Duration:
11/2018 - 04/2021