Novel three dimensional shape measurement technique for fast rotating objects
The measurement of shape and position of fast rotating workpieces with sub-micron precision enables important advances in process technology, for instance in metal cutting lathes. The interferometric P-LDD sensor system employs the simultaneous measurement of the lateral surface velocity and the axial surface distance, in order to measure the absolute shape and position of the rotation axis with keyhole access. The P-LDD sensor system was integrated into a lathe (cooperation with PTB in Braunschweig) and the shape of a workpiece was measured with a standard deviation of 300 nm at high lateral surface velocities. However, speckle noise and thermal drifts of the calibration functions currently limit the total measurement uncertainty for this novel system. Camera based signal detection with coherent fiber bundles and novel signal processing algorithms are investigated, in order to overcome these limitations and miniaturize the sensor. It was shown, that evaluating individual speckles reduces the total shape uncertainty below 100 nm, enables an in-situ calibration and increases the lateral resolution. Thus, micro-geometric features of free form parts can be resolved additionally to the shape in-situ with submicron uncertainty. A novel in-situ vibration measurement approach in CNC machines with a single sensor was proposed, which enables measuring the vibrations in two vertical directions simultaneously.
Staff:H. Zhang, R. Kuschmierz
Period: 08/2016 – 07/2019

P-LDD Sensor measuring shape inside a lathe
R. Kuschmierz, A. Davids, S. Metschke, F. Löffler, H. Bosse , J. Czarske, A. Fischer “Optical, in situ, three-dimensional, absolute shape measurements in CNC metal working lathes“, The International Journal of Advanced Manufacturing Technology, Volume 84, Issue 9, pp 2739-2749 (June 2016).
.
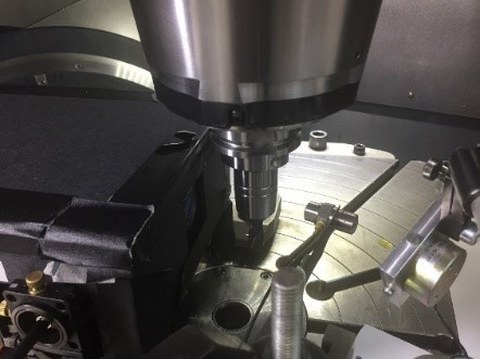
in-situ vibration measurement inside of a CNC machine
H. Zhang, R. Kuschmierz, J. Czarske, “Miniaturized interferometric 3-D shape sensor using coherent fiber bundles”, Optics and Lasers in Engineering, 107, 364-369 (2018).