Space Transportation
This research field covers the scientific investigation and development of critical technologies for the transportation between Earth, space and other celestial bodies. The focus lies on innovative chemical propulsion systems, with a world-leading expertise in the field of additively manufactured aerospike engines for thrust levels between 1 N and 30 kN.
To investigate such engines, experimental measurements are carried out on cold gas test benches as well as in hot gas tests at the institute's own engine test field or at external partners. Another focus is on the numerical simulation of specific flow phenomena, such as re-entry or thrust vector control, which in turn are verified by the corresponding experimental activities.
Another research focus is the use of extraterrestrial resources. This so-called "In-Situ Resource Utilization" (ISRU) plays a central role in future space concepts and enables, for instance, the acquisition of propellant for missions on the moon or Mars. This research will not only enable the more efficient and environmentally friendly use of space, but will also enable currently unfeasible missions to explore the cosmos.
In addition, the impact of space transport systems on the environment and climate is increasingly becoming the focus of research. Understanding these influences, deriving tools for trading off design decisions and developing technologies to minimise these influences are the declared objectives of this field of research. Initial progress has already been made with the development of biodegradable thermal protection materials for re-entry systems.
Contact:
Dr.-Ing. Christian Bach
Head of Space Transportation
Recent projects
SR Dorado
Within the framework of the STERN III funding (STudentische ExperimentalRaketeN) of the German Aerospace Center (DLR) (BMWK: FKZ 50RL2252), TU Dresden established a new development project called SR Dorado. As a follow-up project to the SMART Rockets campaign, the Institute of Aerospace Engineering (ILR) is developing a novel, larger and more powerful sounding rocket in cooperation with the Student Spaceflight Group (STAR) Dresden. The focus of this development project is on the practical training of students in the field of launch systems. The aim is to promote both specialized training as a supplement to study topics, as well as work in project structures and the deepening of social skills. The rocket is scheduled for launch in spring 2025 from the northern Swedish launch site ESRANGE in Kiruna.

Cross-section SR Dorado
ASPIRER
Within the framework of the ESA funded project "AeorSPIke Rocket Engine Realisation" (ASPIRER), an additively manufactured aerospike breadboard thrust chamber using kerosene and hydrogen peroxide as propellants is developed and tested. The engine is designed for 6 kN thrust at 2.0 MPa chamber pressure and is manufactured from nickel-based superalloy INCONEL® 718 powder using the laser powder bed fusion process (LPBF). A staged-bipropellant concept is applied, where hydrogen peroxide is decomposed by a catalyst and combustion is initiated by kerosene autoignition. The overall objective of the activity is a bread board design and test piece of an space engine for space exploration. The engine shall be demonstrated in a final hot-fire test in 2024. The project is part of the overall effort at Technische Universität Dresden to overcome the low Technology Readiness Level (TRL) and the resulting uncertainties associated with aerospike engines and is carried out in cooperation with Fraunhofer Institute for Material and Beam Technology (IWS), the Łukasiewicz Institute of Aviation and ArianeGroup.
LUNAR ISLANDS
Within the "LUNAR In-SituLANDing Structures" (LUNAR ISLANDS) activity, funded by the European Space Agency, an international consortium led by TU Dresden is assessing the effectiveness of in-situ manufactured structures on the containment of high-velocity particles that are generated by the plume-surface interaction of landers. This involves the manufacturing and characterisation of samples from lunar regolith simulants, experimental investigations in the form of cold gas and hot fire tests as well as numerical simulations of the interaction of exhaust plumes and lunar regolith. During this project, TU Dresden as the prime is executing a central part of the numerical investigations of the continuum flow and the peripheral region of the exhaust jet. In addition, the University of Glasgow is involved with cold gas tests and simulations of the surface interaction, while ONERA is involved with subsequent hot gas experiments. The replica of lunar regolith used for this purpose is manufactured by TU Berlin, while the material characterization and particle simulations are carried out at TU Braunschweig.
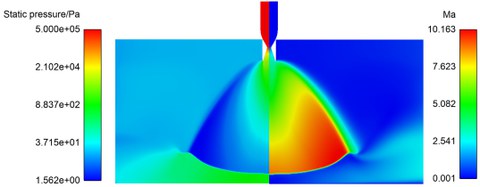
Simulation of an engine exhaust jet directed downwards and its interaction with the ground.
SOCRATES
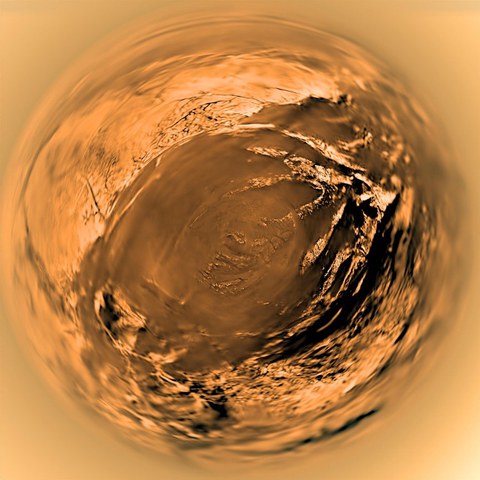
Surface of Saturn's moon Titan captured by Huygens
The project "Solid Oxide Cell Realisation through Adaptation of Terrestrial Energy Systems" (SOCRATES) aims to revolutionize outer planets exploration by developing an innovative Solid Oxide Fuel Cell (SOFC) system using hydrocarbons and oxygen. This alternative power source addresses the challenges of energy generation in the outer solar system, leveraging the proven capabilities of SOFC technology, as demonstrated on the Perseverance rover.
Financed by the European Space Agency (ESA), SOCRATES involves key partners in its development. The Fraunhofer Institute for Ceramic Technologies and Systems (IKTS) is responsible for the demonstrator's development and testing, ensuring its practical viability. Concurrently, TU Dresden manages the state-of-the-art (SOTA) aspects and investigates the utilization of residual propellants as fuel, contributing valuable insights to the project's comprehensive approach.
This collaborative effort holds the potential to redefine the landscape of outer planets exploration, providing a reliable, high-energy-density power source for future space missions in challenging environments.
TPSea2
TPSea2 is a follow-up project to TPSea and focusses on the application-related investigation and feasibility of the contents identified in the TPSea project. The aim is to design an ablative thermal protection system (TPS) from renewable raw materials, in particular natural fibres, by developing, producing and qualifying a dimensionally stable bio-based material that meets the highest material standards. The developed bio-based TPS utilises the acceptance of a previously used material of biological origin - cork - but offers improved mechanical properties and avoids its disadvantages. This means that it can be used much more widely as a bioeconomic high-tech and can be utilised in the future as a substitute material for a more sustainable space economy. TPSea2 thus aims to establish bioeconomic principles in a prestigious industry with the highest added value - the space industry.
Within the framework of the funding guideline “Ideas competition: New Products for the Bioeco-nomy” in the context of the German “National Bioeconomy Strategy” the project is funded and administered by the Federal Ministry of Education and Research (BMBF, Bundesministerium für Bildung und Forschung) and the Projektträger Jülich (ptj).
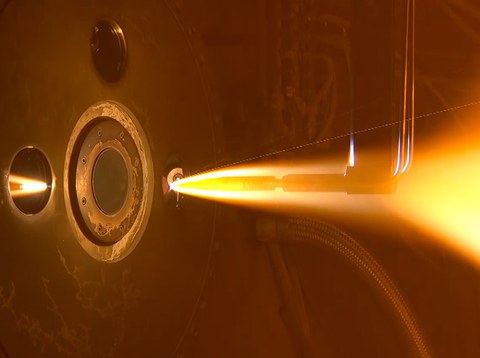
Investigation of a biobased sample in the DLR plasma channel
NEDSERD
The project "Numerical and Experimental Demonstration Study for Engines using Rotating Detonation" (NEDSERD) is investigating the extent to which rotating detonation engines can be used for space applications and the extent to which they can provide an advantage over conventional space propulsion systems, especially in terms of the overall system design. As the name suggests, Rotating Detonation Engines use detonation as a combustion process to convert the chemical energy from the propellant and oxidizer into thermal energy. Compared to conventional isobaric combustion at constant pressure, detonation combustion as a pressure-increasing process theoretically offers an efficiency improvement. Such an efficiency gain can be exploited, for example, by carrying less propellant and more payload or by reducing the total mass and thus the take-off costs. In addition to the efficiency advantage, Rotating Detonation also offers the advantage that combustion takes place in a more compact space and thus the length of the engine can be reduced, so that the launch vehicle can be built shorter and lighter. In addition to these advantages, there are challenges that need to be overcome, such as the very high thermal loads in the combustion chamber and reproducible and stable operation.
For this reason, TU Dresden, together with its project partners ArianeGroup and the Institute of Space Propulsion of the German Aerospace Center (DLR) in Lampoldshausen, is investigating rotating detonation drives for space applications to determine their integrability into an overall system and possible application scenarios. Central to this is the realisation of numerical flow simulations and hot test campaigns in order to understand and overcome the detonation process and the challenges that arise.
We are currently looking for a student assistant to support the simulation work on the NEDSERD project. Click here for further information.
THOMAS
As part of the "THrottable Oxygen Methane AeroSpike" THOMAS project funded by the European Space Agency (ESA), an aerospike engine is being designed for extraterrestrial landing applications, e.g. on the moon. The engine uses oxygen and methane as propellants and is designed to provide a thrust of 20-30 kN. The aerospike engine design was chosen because, unlike conventional engines with bell nozzles, it can adapt its exhaust flow more effectively to the ambient pressure. In addition, when truncated, the overall size can be reduced while maintaining a comparable thrust. Despite the truncation, the thrust only decreases slightly, so that this difference is compensated for by the reduction in system weight. Due to the shorter overall length of the propulsion system, a corresponding landing module can be designed to be shorter and more space can be provided to payloads. Alternatively, the launcher can be kept shorter and thus lighter, which has a positive effect on launch costs. A demonstrator engine will be derived based on the design of the lander engine. Alongside the design process, numerical flow tests are carried out, the results of which are incorporated into further development. The demonstrator will then be additively manufactured from a copper alloy using the Laser Powder Bed Fusion (LPBF) process at the Fraunhofer Institute for Laser Technology (ILT). The post-processing of the demonstrator is carried out by the Fraunhofer Institute for Machine Tools and Forming Technology (IWU) with the aid of cyber-physical systems methods. Ignition and fuel atomization and mixing are being investigated by the Łukasiewicz Research Network - Institute of Aviation. The project will culminate in the demonstrator being tested at the German Aerospace Center (DLR) at the Institute of Space Propulsion in Lampoldshausen.
Publications
All publications associated with Dr.-Ing. Christian Bach on Researchgate and the FIS of the TU Dresden
Selection of some notable publications of the Space Transportation Systems Research Group:
- Buchholz, Maximilian & Gruber, Samira & Selbmann, Alex & Marquardt, Axel & Meier, Lucas & Müller, Michael & Seifert, Lukas & Leyens, C. & Tajmar, Martin & Bach, Christian. (2022). Flow rate improvements in additively manufactured flow channels suitable for rocket engine application. CEAS Space Journal. 10.1007/s12567-022-00476-7.
- Fälker, Svenja & Dorau, Tim & Viedt, Isabell & Mädler, Jonathan & Urbas, Leon & Tajmar, Martin & Bach, Christian. (2022). Modular ISRU Systems as a Building Block for Sustainable Space Exploration.
- Buchholz, Maximilian & Gruber, Samira & Marquardt, Axel & Seifert, Lukas & Selbmann, Alex & Leyens, C. & Tajmar, Martin & Bach, Christian. (2022). Design and test of an additively manufactured 500 N aerospike engine.
- Propst, Martin & Sieder-Katzmann, Jan & Abel, Johannes & Schwarzer-Fischer, E & Scheithauer, Uwe & Tajmar, Martin & Bach, Christian. (2022). Influence of manufacturing accuracy on the performance characteristics of miniaturized ceramic cold-gas thrusters.
- Scarlatella, Giuseppe & Tajmar, Martin & Bach, Christian. (2021). Advanced Nozzle Concepts in retro-propulsion applications for Reusable Launch Vehicle recovery: a case study.
- Dorau, Tim & Propst, Martin & Gruber, Samira & Selbmann, Alex & Joseph, Adheena & Sieder-Katzmann, Jan & Buchholz, Maximilian & Sobczak, Kamil & Soller, Sebastian & Tajmar, Martin & Bach, Christian. (2021). Development of an additively manufactured hydrogen peroxide / kerosene 6kN aerospike breadboard engine.
- Propst, Martin & Sieder-Katzmann, Jan & Stark, Ralf & Schneider, Dirk & General, Stephan & Tajmar, Martin & Bach, Christian. (2021). ACTIVE – Optimisation of a Fluidic Thrust Vector Control on Aerospike Nozzles.
- Buchholz, Maximilian & Gloder, Alessia & Gruber, Samira & Marquardt, Axel & Meier, Lucas & Müller, Michael & Propst, Martin & Riede, Mirko & Selbmann, Alex & Sieder-Katzmann, Jan & Tajmar, Martin & Bach, Christian. (2020). Developing a roadmap for the post-processing of additively manufactured aerospike engines.
- Sieder-Katzmann, Jan & Propst, Martin & Tajmar, Martin & Bach, Christian. (2019). Cold gas experiments on linear, thrust-vectored aerospike nozzles through secondary injection.
- Propst, Martin & Liebmann, Vera & Sieder-Katzmann, Jan & Bach, Christian & Tajmar, Martin. (2018). Maximizing side force generation in aerospike nozzles for attitude and trajectory control.
- Propst, Martin & Ruemmler, Lucas & General, Stephan & Liebmann, Vera & Sieder-Katzmann, Jan & Bach, Christian & Tajmar, Martin. (2018). FLOW VISUALISATION AND SURFACE MEASUREMENTS OF SHALLOW WATER EXPERIMENTS EXEMPLARY FOR AEROSPIKE NOZZLES WITH SECONDARY INJECTION.
- Bach, Christian & Schöngarth, Sarah & Bust, Bernhard & Propst, Martin & Sieder-Katzmann, Jan & Tajmar, Martin. (2018). How to steer an aerospike.
- Bach, Christian & Sieder-Katzmann, Jan & Tajmar, Martin & Przybilski, Olaf. (2013). SMART Rockets – A Contribution to the DLR STERN Programme by Dresden University of Technology.