ImPosAnt
Table of contents
Important data at a glance
Project titel: | Development of pulse-compensated positioning drive systems (ImPosAnt) |
---|---|
Duration: | 06/2021 – 05/2023 |
Collaborative project: | yes |
Subproject title: | Development of calculation algorithms for the control of the compensation drives required for the realization of the pulse compensation as well as design and design optimization of the components of the positioning system |
Funding: | AiF, BMWi Program: ZIM |
Funding code: | 01LY2004B |
Processor / Contact person: | Dipl.-Ing. Marcel Merx Dr.-Ing. Jens Müller Dipl.-Ing. Christoph Peukert |
Cooperation: | Jenaer Antriebstechnik GmbH |
Logline: | As part of the project, intelligent servo amplifiers and a pulse-compensated positioning system are being developed with the project partner JAT. |
Objective
Motivation
Pulse compensation is a method developed and patented at the Chair of Machine Tools Development and Adaptive Controls, in which the structure-exciting reaction force components of electric feed drives are compensated by a targeted control of additional drives (compensation drives), thus achieving an increase in the dynamics of the motion specifications while maintaining or improving motion accuracies (cf. [TUD06] and [Ihl20]). For the industrial applicability of the method, it is necessary to implement the path planning algorithms for all involved drives in their drive controllers.
Solution approach
The goal and innovative core of the cooperation project is to develop adaptive algorithms for the control of the compensation drives based on simulation and to integrate them in the form of technology functions into the drive control units of JAT GmbH. The experimental testing, the functional verification as well as the proof of the dynamic increase with increased motion accuracy will be carried out on a newly developed positioning drive system adapted to the possibilities and advantages of the pulse compensation. The main contributions of the cooperation partners to the innovation process are illustrated in Fig. 1.
Challenges
Implementation of the algorithms on the servo amplifiers from JAT
For the efficient and control-independent control of the compensation drives, the corresponding calculation algorithms must be implemented in the inverter. Only by providing the required software functionalities in the JAT drive controllers can pulse compensation be successfully implemented in industrial applications. However, the computing power and the memory space in the servo amplifier are limited. Especially for very low interpolation clocks, it is conceivable that the required calculation time for the algorithms is too large. In addition, the implementation of non-causal filtering to avoid phase shifts requires the intermediate storage of path segments. At present, it has not yet been clarified how large the path sections and thus the memory requirement in the inverter must be.
Implementation of cross communication between several servo amplifiers
In order to be able to additionally take interference force influences into account, data exchange between several inverters via cross communication is required. For the different fieldbuses supported by JAT it is not known to what extent they support cross communication.
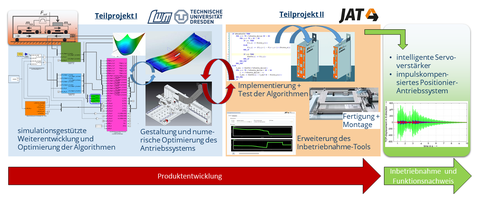
Fig. 1: Classification of the subprojects in the innovation process
Solution
To achieve the objective, the development and implementation of extended functionalities (technology functions) of existing drive control units (servo amplifiers) as well as the development of constructive solutions for minimizing the mass of the moving assemblies, the thermostable design as well as the integration of the compensation drives required for the pulse compensation are necessary.
In particular, the following basic sub-objectives (implementation variants of the control of the compensation drives) are to be implemented, which represent the innovative core of the project and at the same time serve as purchasing arguments for the customer, since the appropriate servo amplifier type can be selected or combined by the customer depending on requirements and application (cf. Fig. 2):
- Target path preparation in the control system, use of 1-channel servo amplifiers, without consideration of disturbance forces (Fig. 2, variant a)
- Setpoint path preparation in the 2-channel servo amplifier, without taking interference forces into account (Fig. 2, variant b)
- Setpoint path preparation in the 2-channel servo amplifier, with consideration of disturbance forces using internal cross communication (Fig. 2, variant c)
- Setpoint path preparation in the 1-channel servo amplifier, cross communication between the servo amplifiers, without and with consideration of disturbance forces (Fig. 2, variant d)
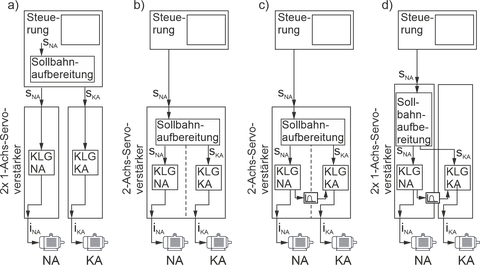
Fig. 2: Overview of the innovation levels of the functionalities in the drive controllers
Results
The technology maturity level TRL 6 is targeted. Using the fully tested, pulse-compensated positioning system, an increase in dynamics by a factor of 10 in terms of acceleration and jerk as well as a reduction in vibration excitation by 80% measured in terms of vibration amplitude must be demonstrated.
Sources
[TUD06]: Schutzrecht DE 102004057062B4 (22.06.2006). Großmann, K. ; Müller, J. ; Jungnickel, G. ; Mühl, A. (Erfinder); TU Dresden, 01069 Dresden (Anmelder)
[Ihl20]: Ihlenfeldt, S. ; Müller, J. ; Merx, M. ; Kraft, M. ; Peukert, C. : Simplified Manufacturing of Machine Tools Utilising Mechatronic Solutions on the Example of the Experimental Machine MAX. In: Yan, X.-T. (Hrsg.) ; Bradley, D. (Hrsg.) ; Russell, D. (Hrsg.) ; Moore, P. (Hrsg.) : Reinventing Mechatronics: Developing Future Directions for Mechatronics. Springer, 2020, pp. 145–162 – ISBN 978–3–030–29131–0
Contact
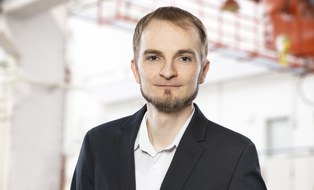
Research associate
NameMr Dipl.-Ing. Marcel Merx
Control and Feedback Control Systems
Send encrypted email via the SecureMail portal (for TUD external users only).
Chair of Machine Tools Development and Adaptive Controls
Visiting address:
Kutzbach-Bau, Room 203 Helmholtzstraße 7a
01069 Dresden