Modal Control II
Table of contents
Important data at a glance
Project titel: | Basic investigation of the application of modal control for overactuated machine tools (Modal Control II) ► Continuation project |
---|---|
Duration: | 06/2021 – 05/2024 |
Collaborative project: | no |
Funding: | DFG |
Funding code: | IH 124/4-2 |
Processor / Contact person: | Dipl.-Ing. Christoph Peukert |
Cooperation: | Jenaer Antriebstechnik GmbH |
Logline: | In modal control, the control loops of overclocked machine tools are modally decoupled in order to achieve high dynamic path accuracy and thus high accuracy on the workpiece as well as increased process stability. |
Objective
Motivation
Highly dynamic motion processes and process forces cause both the moving assembly (e.g. slide) and the underlying machine structure (e.g. frame) to vibrate. Especially for lightweight structures, high vibration amplitudes result. Vibrations in machine tools lead to a deterioration of the machining quality and must therefore be reduced to a minimum. In order to enable an increase in dynamics while maintaining or improving the quality of motion, measures for vibration reduction or avoidance are required. In general, the reduction of dynamic compliance at the tool center point should be aimed at in order to increase process stability and chatter limit. This can be achieved by increasing the system damping, for which purpose active damping systems, so-called active damping devices, are used. As a rule, the drives required for motion generation and the additional actuators are controlled independently of each other and without consideration of mutual interference. This makes the selection and parameterization of mechanically coupled drives and additional actuators difficult. In addition, the control loop performance of such overactuated systems is limited.
Within the scope of a preceding first project phase, three test objects with different focal points of investigation were realized and investigated simulatively and experimentally (see Fig. 1). Numerical models were developed for all configurations for simulation-based investigation with respect to suitable control concepts [Peu19a], determination of modal quantities [Pöh17], optimal sensor/actuator placements [Pöh18], and for predetermination of the components of the experimental setups. First, the MR for vibration damping of an elastic structure (fixed gantry bridge) was investigated simulatively and experimentally using two ADDs (Config. 1). Using the example of a linear motor-driven gantry axis, which was investigated metrologically without (Config. 2) and with (Config. 3) additional actuators, it was possible to work out the relationships, advantages, but also difficulties in the application of modal control for machine tools (see [Peu19b] and [Peu19c]). The modal control approach is advantageous because all sensor signals are considered in each modal control loop. In addition, the modal forces required for vibration damping are specifically generated by all available actuators. Modal control makes it possible to control the eigenmodes individually. Modal control of the cascaded position and velocity control loops is particularly advantageous in the case of rigid coupling of the drives (cf. Conf. 2) and the associated strong dynamic interaction of the drives, since it decouples the system and allows higher gain factors to be set, which makes it possible to achieve high dynamic path accuracy and thus high accuracy on the workpiece. However, the increase in control bandwidth is limited due to spillover effects that occur. In addition, it was shown for two positions of the cross slide or the additional mass (manual adjustment) that modal decoupling simplifies the parameterization of the controllers of all drives and actuators involved and reduces the feedback effect of the active additional systems on the position control of the feed drives (cf. Config. 3).
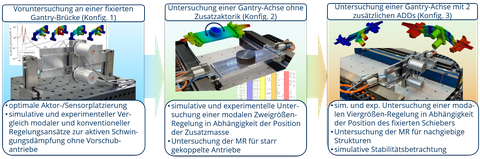
Figure 1: Overview of the focal points and objects of investigation in the first project phase
Solution approach
The aim of the research project is to use modal control (MR) to improve the dynamic properties of motion systems, such as machine tools, which have more drives or actuators than degrees of freedom of movement. Modal control makes it possible to individually control eigenmodes and to selectively damp the excited oscillations with all available actuators. Modal decoupling is intended to simplify the parameterization of the controllers of all drives and actuators involved and to reduce the feedback effect of the active auxiliary systems on the position control of the feed drives. The aim is to increase the control bandwidth of the feed axes and reduce the dynamic compliance at the TCP in order to achieve high dynamic path accuracy and thus high precision at the workpiece as well as increased process stability.
Research question
Can modal control of electromechanical feed axes achieve a significant improvement in dynamic path accuracy?
Is it possible to increase the stability limits during milling with the help of modal control?
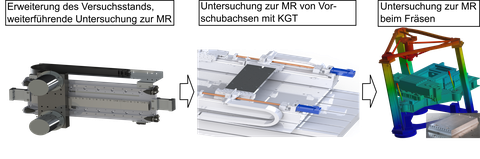
Figure 2: Overview of the procedure
Solution
To achieve the objective, the following further investigations are planned, building on the results of the 1st project phase (modal control I): In order to reduce the observation spillover, investigations to improve the modal separation are planned. For this purpose, the existing trainer (see Fig. 2, left) will be extended by one axis in order to investigate MR for structures with position-variable system properties and to develop methods for adapting the modal transformations or the modal controller parameters. Using another existing trainer (DFG project IH124/6), see Fig. 2 center, the MR of electromechanical feed axes with ball screws (KGT) will be investigated in order to remove the restriction of the application to linear motor driven axes. Furthermore, milling tests are to be carried out on the experimental machine MAX (see Fig. 2, right, cf. DFG project GR1458/48) in order to provide evidence for the increase in stability limits expected with MR.
Sources
[Peu19a] Peukert, C. ; Pöhlmann, P. ; Ihlenfeldt, S. ; Müller, J. ; Merx, M. : Modale Regelung von Werkzeugmaschinen – Anwendung der modalen Regelung für eine Gantry-Anordnung. In: wt Werkstattstechnik online 109 (2019), Nr. 5, S. 358–364. – ISSN 1436–4980
[Peu19b] Peukert, C. ; Pöhlmann, P. ; Merx, M. ; Müller, J. ; Ihlenfeldt, S. : Investigation of local and modal based active vibration control strategies on the example of an elastic system. In: Journal of Machine Engineering 19 (2019), Nr. 2, S. 32–45. – ISSN 2391–8071
[Peu19c] Peukert, C. ; Pöhlmann, P. ; Merx, M. ; Müller, J. ; Ihlenfeldt, S. : Modal-space Control of a Linear Motor-driven Gantry System. In: MM Science Journal (2019), S. 3285–3292
[Pöh17] Pöhlmann, P. : Recherche und Implementierung effizienter Berechnungsverfahren modaler Größen für die modale Regelung von Werkzeugmaschinen. Studienarbeit, TU Dresden, 2017
[Pöh18] Pöhlmann, P. : Simulationsgestützte Untersuchung zur modalen Regelung einer Gantry-Achse und Auslegung zusätzlicher Aktorik und Sensorik. Diplomarbeit, TU Dresden, 2018
Contact

Research associate
NameMr Dipl.-Ing. Christoph Peukert
Control and Feedback Control Systems
Send encrypted email via the SecureMail portal (for TUD external users only).
Chair of Machine Tools Development and Adaptive Controls
Visiting address:
Kutzbach-Bau, Room 203 Helmholtzstraße 7a
01069 Dresden