ReHoAkt I
Table of contents
Important data at a glance
Project titel: | ReHoAkt I – Controllable FGL high-load actuator for automated fine adjustment of machine components and large parts |
---|---|
Duration: | 05/2019 – 10/2020 |
Collaborative project: | yes |
Subproject title: | FGL actuator simulation, measurement system development, and simulation-based alignment procedure development for large parts and machine components |
Funding: | PTJ, BMBF zwanzig20 |
Funding code: | 03ZZ1040A |
Processor / Contact person: | Dipl.-Ing. Ludwig Rogall Dipl.-Ing. Christoph Peukert |
Cooperation: | Fraunhofer IWU LWW, TU Chemnitz Feinmechanisches Fertigungszentrum Glashütte GmbH FFZ Dr. Matzat & Co. GmbH A.S.T. – Angewandte System Technik GmbH, Mess- und Regeltechnik watttron GmbH |
Logline: | Development of methods for fine adjustment of large components and machine components by means of shape memory high-load actuators, which are also to be developed, and using structure-integrated force measurement technology. |
Objective
Motivation
Both during assembly and commissioning as well as for the operation of machine tools, there are very high requirements with regard to the measurement and alignment or positioning of assemblies, such as guides, spindles, bearings and drives. The machining of large workpieces also requires time-intensive alignment processes. Particularly in the case of very precise and high-quality large components, more time is sometimes required for alignment than for machining the workpiece itself [1]. In the fine alignment of machine components and large parts, there is also a great dependence on the expertise and skills of the personnel. Thus, the fine alignment of machine components during initial commissioning, retrofitting or repair of machines, as well as the fine alignment of large workpieces, results in a high value-added share.
Solution approach
The aim of the project is to automate and thus significantly shorten alignment processes of workpieces and machine components with shape memory actuators. In order to allow a time- and cost-efficient as well as operator-independent alignment of machine components and large parts, controllable high-load actuators based on shape memory alloys (FGL) are to be developed and experimentally investigated (basic technology development). The force sensor technology integrated into the carriage developed in the joint project is to be used to align the PSF with low stress.
Challenges
The scientific and technical challenges can be divided into two main areas: actuator development and the automation of adjustment processes.
- In the field of actuator development, detailed solutions for FGL actuator technology, sensor technology and control must be developed for the specific requirements of the selected example applications. This includes the layout, design and construction of all relevant actuator components / assemblies. In particular, the resetting of the actuator to its initial position or length poses a challenge due to the high force required. In addition, the nonlinear and hysteretic conversion behavior of the FG material makes it difficult to achieve a high positioning accuracy.
- The core of the second focus is the development of methods for automated fine adjustment of profile rail guides by means of FGL high-load actuators and using structure-integrated force measurement technology. This requires model-based concept development, measurement-based manipulated variable calculation, actuator control and qualification of the sensor signals of the carriage-integrated measurement technology based on strain gauges.
Solution
Preliminary experimental investigations were carried out to define the requirements for the actuator. A test facility was designed and set up for this purpose. A load cell recorded the actuating forces occurring when positioning a screwed profile rail. The pre-assembly torques of the screws, the profile rail size and the surface quality of the mounting surface were varied.
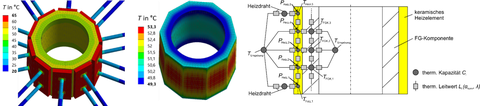
Fig. 1: FE simulation of the hollow cylindrical FG actuator with heating elements and wires (left), associated temperature gradient in the FG element (center) and corresponding network model (right).
Based on the requirements for travel and actuating force previously determined by the LWM, the project partner IWU developed a concept for an FGL high-load actuator. The achievable actuating dynamics of the thermally activated actuator is essentially determined by the geometry of the shape memory component and its thermal insulation. To design and dimension the geometries, LWM created a thermal conduction model. The finite difference method was chosen as the approach. With this approach and a suitable local model discretization, the prerequisites for a computationally efficient and real-time capable implementation for later use in a model-based control system could be created. The model was parameterized on the basis of thermographic investigations.
In addition, two concepts for generating actuator travels of different sizes were compared using this model. A monolithic design of the shape memory components (FGK) requires a higher control accuracy of the temperature of the heating elements used. On the other hand, it is much smaller than a split structure consisting of individual discretely activatable elements, which requires sufficiently good thermal insulation between the individual elements. The additional insulation layers also make the structure significantly more compliant.
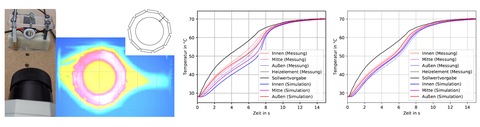
Fig. 2: Adjustment of the thermal behavior of the FG component: Measurement setup and thermal image (left) as well as temperature curves over the cross section before (center) and after model matching (right).
In addition to the mechanics and the actuators, the control system is an essential component of controllable actuators. With its hysteresis-laden, strongly nonlinear behavior, the shape memory alloy exhibits unfavorable properties for achieving the targeted actuator positioning accuracy with conventional control technology. Therefore, the LWM pursued the approach of a model-based control. For this purpose, a material model was created that reproduces the hysteresis of the phase transformation of the microstructure by means of a model with Preisach memory. The model also takes into account the dependence of various material parameters on the state variables of the alloy. It was parameterized using test data from various materials science studies conducted by the partner LWW. The material model was then coupled with the heat conduction model described above and a mechanical model in order to be able to represent the existing interactions.
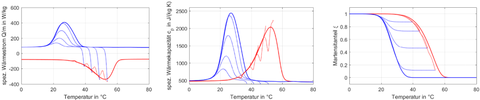
Fig. 3: Heat flow measurement (left) and heat capacity calculated from it (center) as well as martensite content calculated by means of material model (right) for different hysteresis loops.
With the aim of improving the achievable positioning accuracy of the actuator, the LWM looked at ways of detecting its positioning movement close to the active point. Due to the thermal activation of the FGL, a relevant temperature increase in the sensor was to be expected. Without suitable countermeasures, strong temperature changes usually have a negative effect on the measuring accuracy of position sensors. To estimate the influence, a simulation-based investigation of the temperature development was carried out.
The project partner A.S.T. GmbH developed a carriage-integrated force measurement technology for low-stress alignment. To support the partner in its design, the most important requirements were derived from the intended use cases of the sensor technology. In addition, the LWM developed options for using the force measurement technology set up by the partner A.S.T. GmbH not only during the assembly of the profile rails but also during the operation of the feed axis.
For the development of the alignment methods, different approaches were designed and compared with regard to their technical complexity, the achievable degree of automation and the positioning accuracy. To estimate the achievable positioning accuracy, simulation models were created in the multi-domain environment Simulink® and used to simulate positioning and alignment processes.
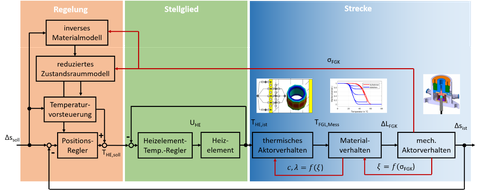
Fig. 4: Block diagram showing the control concept taking into account the line characteristics
The alignment procedures were to use the previously developed FGL actuator concept to generate the actuating motion. A systematic design process was followed to create the necessary mechanics. Particular attention had to be paid to the cramped installation situation and the sensitivity of the shape memory component to uneven loading. Various principles were compared for guiding the actuating movement. No clear preferred solution could be identified. Therefore, two variants were finally constructed. The geometry of these alignment modules was investigated using the finite element method. The aim was to determine a good compromise between stiffness and size.
Results
With the completion of the project, a prototype of an FG high-load actuator developed together with the project partners is available. The prototype meets the requirements for stroke (>200 µm) and actuating force (>10 kN) and is optimized in terms of its actuating dynamics. For its control, a concept for a model-based control is available, which is based on extensive and adjusted thermal, material and mechanical models.
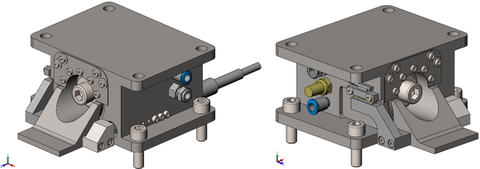
Fig. 5: High-load actuator prototype 1; left: Perspective from right; right: Perspective from left.
In addition, as a result of the project, several procedures are available to LWM for both geometric and low-stress alignment of the profile rail guides of feed axes. The process variants differ in terms of the type and quantity of fixtures required, the requirements on the installation environment for mounting these fixtures, and the degree of automation that can be achieved by them.
To generate the actuating motion, the processes provide for an alignment module that integrates the previously developed FG high-load actuator concept. With the completion of the project, two designs of the alignment module are available (cf. Fig. 5 and Fig. 6). They can be used for the alignment of three profile rail sizes due to a suitable geometry and due to the forces that can be generated with them. Furthermore, the most favorable location for travel measurement was identified in order to reduce measurement errors as a result of load- and temperature-related deformation. The dimensions of the first variant of the alignment module are 118x60x134 mm³, those of the second variant 118x80x189.5 mm³.
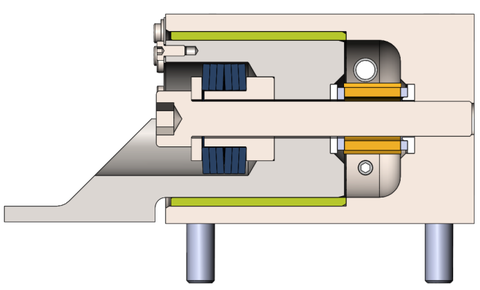
Fig. 6: Sectional view of high-load actuator prototype 1 (from right) with shape memory component (orange), disk springs (blue) and plain bearing (green).
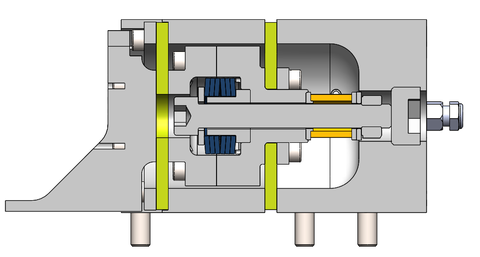
Fig. 7: Sectional view of high-load actuator prototype 2 (from right) with shape memory component (orange), disk springs (blue) and diaphragm springs as bearing (green)
For the subsequent use of the force measurement technology, process load calculation and monitoring of possible damage to the profile rail guide were identified as attractive and feasible applications.
Publications
[1] Bimatec, S. : Vollintegriertes 3D-Vermessungssystem. In: MAV: Innovation in der spanenden Fertigung (2015), Nr. 6, S. 112
Contact
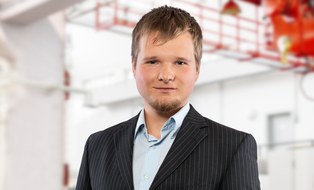
Research associate
NameMr Dipl.-Ing. Ludwig Leser
Control and Feedback Control Systems
Send encrypted email via the SecureMail portal (for TUD external users only).
Chair of Machine Tools Development and Adaptive Controls
Visiting address:
Kutzbach-Bau, Room 203 Helmholtzstraße 7a
01069 Dresden