ReHoAkt II
Inhaltsverzeichnis
Wichtige Daten im Überblick
Projekttitel: | ReHoAkt II – Geregelte FG-Hochlastaktorik für die automatisierte Feinjustierung von Maschinenkomponenten und Großbauteilen |
---|---|
Laufzeit: | 11/2020 – 04/2022 |
Verbundvorhaben: | ja |
Teilprojekttitel: | Entwicklung und experimenteller Funktionsnachweis einer Automatisierungslösung zur Ausrichtung von Profilschienen mittels FG-Hochlastaktorik |
Finanzierung: | PTJ, BMBF zwanzig20 |
Förderkennzeichen: | 03ZZ1040A |
Bearbeiter: | |
Kooperationspartner: |
Fraunhofer IWU Feinmechanisches Fertigungszentrum Glashütte GmbH FFZ Dr. Matzat & Co. GmbH A.S.T. – Angewandte System Technik GmbH, Mess- und Regeltechnik watttron GmbH |
Logline: | Entwicklung und Erprobung von Konzepten zur Feinjustage von Großbauteilen und Maschinenkomponenten mittels der FG-Aktoren sowie Entwicklung, Konstruktion, Bau und experimentellen Funktionsnachweis einer Automatisierungslösung zur Ausrichtung von Profilschienen mittels FG-Hochlastaktorik. |
Zielstellung
Motivation
Sowohl bei der Montage und Inbetriebnahme als auch für den Betrieb von Werkzeugmaschinen (WZM) bestehen sehr hohe Anforderungen hinsichtlich der Vermessung und Ausrichtung bzw. Positionierung von Baugruppen, wie z. B. Führungen, Spindeln, Lagern und Antrieben. Auch die spanende Bearbeitung großer Werkstücke erfordert zeitintensive Ausrichtvorgänge. Insbesondere bei sehr präzisen und hochwertigen Großbauteilen wird teilweise mehr Zeit für das Ausrichten benötigt als für die Bearbeitung des Werkstücks selbst [1]. Bei der Feinjustierung von Maschinenkomponenten und Großbauteilen besteht zudem eine große Abhängigkeit vom Fachwissen und den Fähigkeiten des Personals. Somit ergibt sich durch die Feinausrichtung von Maschinenkomponenten bei der Erstinbetriebnahme, beim Retrofit bzw. der Reparatur von Maschinen sowie bei der Feinjustierung großer Werkstücke ein hoher Wertschöpfungsanteil.
Lösungsansatz
Ziel des Vorhabens ist es, Justageprozesse von Werkstücken und Maschinenkomponenten mit Formgedächtnisaktorik zu automatisieren und damit deutlich zu verkürzen. Um eine zeit- und kosteneffiziente sowie bedienerunabhängigere Ausrichtung von Maschinenkomponenten und Großbauteilen zu erlauben, sind regelbare Hochlastaktoren auf Basis von Formgedächtnislegierungen (FGL) zu entwickeln und experimentell zu untersuchen (Basistechnologieentwicklung). Im Vorgängerprojekt ReHoAkt I lagen die Schwerpunkte auf der Materialuntersuchung und ‐stabilisierung, der Erstellung umfangreicher Simulationsmodelle der Aktoren und der Anwendungen sowie der Entwicklung, Konstruktion und Fertigung geregelter Aktoren. Daneben galt es, ein Konzept zur Verspannungsmessung in PSF zu entwickeln.
In ReHoAkt II werden weitere Versuche durchgeführt, um die in Phase I erstellten Simulationsmodelle weiter zu validieren und die ausgewählten Ansteuerungs- und Regelungsstrategien zu optimieren. Die strukturintegrierte Kraftmesstechnik zur verspannungsfreien PSF-Feinjustage wird optimiert, umgesetzt und experimentell charakterisiert. Aufbauend auf den virtuellen Verfahrensuntersuchungen der geplanten Anwendungen in ReHoAkt I – dem Ausrichten von Profilschienenführungen und dem Ausrichten großer Werkstücke – sollen zudem entsprechende Demonstratoren konstruiert, aufgebaut und untersucht werden. Schließlich sind die entwickelte FGL-Hochlast-Aktorik und die entwickelten Ausrichtverfahren zu bewerten.
Herausforderungen
Die Phasenumwandlungstemperaturen des FG-Materials weisen eine starke Abhängigkeit von der Legierungszusammensetzung auf. Diese variiert sowohl zwischen verschiedenen als auch innerhalb einer Charge des Halbzeugs. Außerdem bewirken unvollständige Gefügeumwandlungen Verschiebungen der Umwandlungstemperaturen.
Innerhalb des Vorhabens sollen Ansätze erarbeitet werden, diese Parameteränderungen in der modellbasierten Steuerung zu berücksichtigen, um so die Stellgenauigkeit weiter zu verbessern.
Die Signale der strukturintegrierten Kraftmessung werden neben den vorhandenen Lagefehlern der Profilschienenführungen der Vorschubachse auch von äußeren Lasten sowie der Geometrie und Anbindung des Schlittens bestimmt. Das Unterscheiden der Ursachen mit möglichst geringem Messaufwand stellt eine Herausforderung dar. Sie ist jedoch erforderlich, um korrekte Stellsignale für die Aktoren zu berechnen.
Im Vorgängerprojekt wurden mehrere Verfahrensvarianten zur Ausrichtung von Profilschienenführungen entwickelt. Der aufzubauende Demonstrator soll die Erprobung möglichst aller entwickelter Verfahren ermöglichen. Die unterschiedlichen Verfahren – das geometrische und das verspannungsarme Ausrichten – stellen unterschiedliche Anforderungen an den Aufbau des Versuchsstandes. Zudem sollen die Verfahren an mehreren Baugrößen untersucht werden und dabei der Materialeinsatz geringgehalten werden. Insgesamt führen die Anforderungen zu einem erhöhten Konstruktionsaufwand.
Lösungsweg
Zur Abschätzung der Einflüsse variierender Materialparameter werden zunächst Sensitivitätsuntersuchungen durchgeführt. Für kritische herstellungsbedingt schwankende Parameter werden anschließend Verfahren zur Identifikation erstellt. Diese können einmalig während der Inbetriebnahme des montierten Aktors durchgeführt werden. Für in Folge des Betriebs der Aktoren veränderliche Parameter gilt es, geeignete Mittel der Regelungstechnik zu finden, zu testen und schließlich zu implementieren.
Zur Erweiterung der Sensitivität der Kraftmesstechnik werden zunächst simulationsbasierte Untersuchungen des Verformungsverhaltens der Baugruppe durchgeführt. Dabei werden die auftretenden Dehnungen an messtechnisch zugänglichen Orten des Laufwagens in Folge von Lagefehlern analysiert. Anschließend wird die geeignetste Kombination an Messorten mittels Hauptkomponentenanalyse ermittelt. Außerdem werden simulationsbasierte Untersuchungen durchgeführt, um geeignete Kalibrierprozeduren zu identifizieren. Zur experimentellen Verifizierung der entwickelten Ansätze wird eine Versuchsvorrichtung aufgebaut. Mittels dieser Vorrichtung wird zunächst das Kalibrierverfahren durchgeführt. Anschließend wird das Kalibrierergebnis durch Manipulation der Schienenabstände validiert.
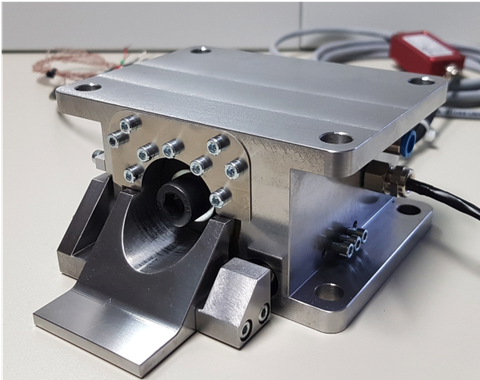
Abb. 1: Aufgebautes Ausrichtmodul – Variante A
Zur Erprobung der Ausrichtverfahren wird eine Vorschubeinheit konstruiert, gefertigt, montiert und in Betrieb genommen. Für dessen Betrieb ist zudem die Erstellung einer Steuerung erforderlich. Die Stellsignale des verspannungsarmen Ausrichtens werden aus den Sensordaten der Kraftmesstechnik berechnet. Hierfür muss dessen Datenerfassungsmodul in die Steuerung eingebunden werden. Die Stellbewegung während des Schienenausrichtens soll mit Ausrichtmodulen erfolgen, die im Vorgängerprojekt konstruiert wurden. In ReHoAkt II werden diese Ausrichtmodule gefertigt, montiert und in Betrieb genommen. Das Herstellen der Kommunikation zwischen Steuerung und den verschiedenen Sensoren und Stellgliedern stellt einen Schwerpunkt dar. Dazu gehören die Heizelemente, das Pneumatikventil sowie verschiedene zu erprobende Wegsensoren. Vor dem Einsatz der Ausrichtmodule im Rahmen der Erprobung der Verfahren ist deren experimentelle Untersuchung vorgesehen, um Schwachstellen in der Mechanik oder der erreichbaren Regelgenauigkeit zu erkennen und ggf. zu beheben. Schließlich sind die in ReHoAkt I erstellten Verfahren experimentell am Versuchsstand an den drei vorgesehenen Profilschienenbaugrößen zu erproben. Dabei sind die Ausrichtergebnisse u. a. hinsichtlich geometrischer Genauigkeit bzw. bleibender innerer Verspannungen sowie Aufwand und Dauer zu bewerten und mit dem Stand der Technik zu vergleichen. Zudem sollen die Einflüsse möglicher Störgrößen, wie z. B. der Temperatur, streuender Vormontagemomente, variierender Zustände der Montageflächen analysiert werden. Zur Bewertung des Potentials des verspannungsarmen Ausrichtens sollen zudem die Motorströme jeweils vor und nach dem geometrischen und verspannungsarmen Ausrichten erfasst und ausgewertet werden.
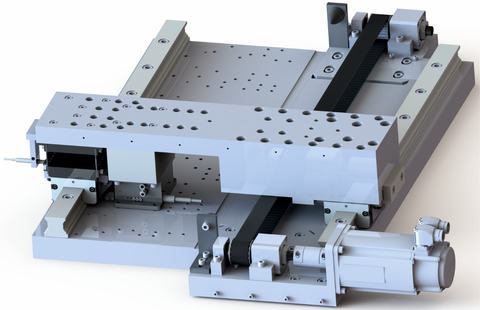
Abb. 2: CAD-Modell des Versuchsstandes zur Erprobung der Verfahren zum Ausrichten der Profilschienen einer Vorschubachse
Für den zweiten Anwendungsfall von regelbaren FG-Hochlast-Aktoren – dem Ausrichten großer Werkstücke- entwickelt, konstruiert und montiert ein Projektpartner einen Versuchsstand mit Dummy-Werkstück und speziell adaptierten FGL-Hochlast-Aktor-Demonstratoren. Für diese Versuchsanordnung entwickelt das LWM ein Ansteuerungskonzept für die Aktor-Demonstratoren. Dies umfasst die Erstellung eines Messkonzeptes zur Erfassung der Werkstücklage, die Erarbeitung von Algorithmen zur Datenauswertung und Berechnung der erforderlichen Aktorstellwege zur Korrektur der Werkstücklage. Das erstellte Steuerungskonzept wird anschließend in die Steuerung des Versuchsstandes implementiert. Letztlich sind am aufgebauten Versuchsstand Mess- und Ansteuerungskonzept der Aktoren experimentell zu untersuchen und zu bewerten.
Anmerkungen
Infolge der Auswirkungen der Corona-Pandemie kam es sowohl beim LWM als auch bei den Projektpartnern zu nennenswerten Verzögerungen bei der Bearbeitung des Projektes. Unter anderem bewirkte ein reduzierter Werkstattbetrieb als Maßnahme der Eindämmungsmaßnahmen die Geschwindigkeit der Fertigung zahlreicher Teile für den Aufbau des Demonstrator-Versuchsstandes. Aufgrund anhaltender Lieferengpässe von Elektronikbauteilen konnten die Ausrichtmodule erst verspätet und mit alternativen Komponenten aufgebaut werden. Dies führte zu einem erhöhten Aufwand zur Implementierung der Kommunikationsfunktionen in die Steuerung.
Daher wurde die Laufzeit des Projektes um vier Monate bis April 2022 verlängert.
Quellen
[1] Bimatec, S. : Vollintegriertes 3D-Vermessungssystem. In: MAV: Innovation in der spanenden Fertigung (2015), Nr. 6, S. 112
Kontakt
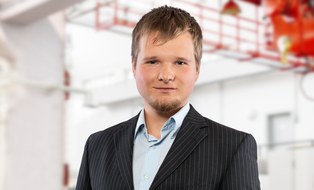
Wissenschaftlicher Mitarbeiter
NameHerr Dipl.-Ing. Ludwig Leser
Antriebs- und Steuerungstechnik
Eine verschlüsselte E-Mail über das SecureMail-Portal versenden (nur für TUD-externe Personen).
Professur für Werkzeugmaschinenentwicklung und adaptive Steuerungen
Professur für Werkzeugmaschinenentwicklung und adaptive Steuerungen
Besuchsadresse:
Kutzbach-Bau, Raum 203 Helmholtzstraße 7a
01069 Dresden