SFB/TR B04 - Identifikation von Modellparametern für exemplarisch streuende sowie zeitlich veränderliche thermische Maschineneigenschaften
Strukturbasierte thermische Maschinenmodelle werden für die entwicklungsbegleitende Analyse sowie die steuerungsintegrierte Korrektur thermisch bedingter Verlagerungen an Werkzeugmaschinen (WZM) genutzt. Sie enthalten unsichere und zeitlich veränderliche Parameter mit signifikantem Einfluss auf die Modellgüte, deren reale Repräsentation sich erst mit der Montage oder beim Betrieb der Maschine einstellt und nicht direkt messbar ist, z. B. Reibungsverluste in Lagern und Führungen oder konvektive Wärmeübergänge. Zur Verbesserung der Modellgüte ist ein exemplarischer Parameterabgleich im betriebsbereiten Zustand erforderlich. Hierbei wird die Maschine mit geeigneten Belastungsversuchen angeregt, das thermische Maschinenverhalten gemessen und aus den Stell- und Messwerten eine Datenbasis gebildet. Auf dieser Basis werden exemplarische Modellparameter dann so angepasst, dass simulierte und reale Messwerte bestmöglich übereinstimmen. Hierfür dienen Methoden der nichtlinearen Optimierung.
Der Erfolg dieses indirekten Parameterabgleichs hängt dabei nicht nur von der Optimierungsmethode, sondern auch von der Konditionierung des Modells ab. Darüber hinaus ist eine hohe Qualität der Datenbasis entscheidend. Relevant hierfür sind die gewählten Belastungsversuche und Messungen. Sie müssen die individuelle Ausprägung von Maschine und thermischem Modell sowie aktuelle Betriebsbedingungen bestmöglich berücksichtigen, d.h. sie müssen spezifisch für diese Randbedingungen entworfen werden.
Ein Parameterabgleich erfordert generell die schrittweise Abarbeitung mehrerer Teilaufgaben. Diese können drei Bereichen zugeordnet werden: Planungsphase (Modellanalyse und -konditionierung, Parameteranalyse, Entwurf der Belastungsversuche und Messungen), Versuchsphase (Belastungsversuche, Messung, Aufbereitung der Datenbasis) sowie Abgleichphase (nichtlineare Optimierung mit Ergebnisverifikation). Dieser Workflow muss, insbesondere in der Planungs- und Versuchsphase, spezifisch auf die oben genannten Randbedingungen angepasst werden. Dies erfolgt bisher weitgehend manuell und gestützt auf umfangreiches thermisches und mathematisches Fachwissen. Der Abgleich beschränkt sich auf wenige dominante Parameter sowie thermische Modelle mit begrenzter Komplexität. Die Belastungsversuche sind einfach und orientieren auf einen thermischen Beharrungszustand mit entsprechend langer Versuchsdauer. Bislang ist der exemplarische Parameterabgleich dadurch zeitlich und personell sehr aufwändig.
Ziel des TP B04 ist die Reduzierung dieses Aufwandes. Der verfolgte Lösungsansatz besteht in der Entwicklung geeigneter Methoden und Werkzeuge zur effizienten Unterstützung des Parameterabgleichs während des Maschinenentwurfs, der Inbetriebnahme und im Betrieb. Als Grundlage erfolgten in Phase 1 des Projektes eine Systematisierung des Vorgehens und die Herausarbeitung geeigneter Ansätze zur Unterstützung des Abgleichs. Wesentliche Aufwände konnten bei der Planung der Abgleichversuche während des Maschinenentwurfs sowie bei der Versuchsdurchführung identifiziert werden. Zur Unterstützung der Planung der Versuche, während des Entwurfs, wurde eine Methodik zur Parameterauswahl über Unsicherheit und Sensitivität entwickelt. In Phase 2 stand die Planung der Versuche im Vordergrund. Inhaltliche Schwerpunkte waren Methoden und Werkzeuge für den simulationsgestützten Entwurf der Abgleichversuche auf Ebene der Achsbaugruppen.
Unter Leitung von Prof. Kabitzsch (TIS) wurden dabei informationstechnisch relevante Untersuchungen hinsichtlich der effizienten Auswahl, Parametrierung und Verknüpfung der vielfältigen Softwaretools und Modelle durchgeführt. Die Erkenntnisse wurden in Form eines Identifikationskoordinators softwaretechnisch umgesetzt und erfolgreich erprobt. Damit ist die Grundlagenforschung beendet und es steht ein Werkzeug für die weitere Nutzung zur Verfügung. Bei der Parameteridentifikation rücken nun Problemstellungen des Abgleiches in der der Betriebsphase der Maschine in den wissenschaftlichen Fokus. Dies wird durch die Expertise des neuen Teilprojektleiters Dr. Hellmich (Fraunhofer IWU) unterstützt.
Ein erster Schwerpunkt in Phase 3 ist die Inbetriebnahmephase, in der die Datenbasis für den Abgleich gewonnen wird. Die Datenbasis enthält die Wirkung der abzugleichenden Parameter, die über Lastregimes angeregt und über Messregimes erfasst wird. Es werden zeitlich komprimierte und für die Achsbaugruppen parallelisierte Lastregimes für den Abgleich des Modells der Gesamtmaschine erstellt. Der zweite Schwerpunkt ist der Parameterabgleich in der Betriebsphase. In dieser herrschen produktionsnahe Bedingungen, die mit eingeschränkter Zugänglichkeit für Messungen, geringer verfügbarer Maschinenzeit für Abgleichversuche und ohne die Möglichkeit der Vorgabe optimaler Lastregimes verbunden sind. Der Fokus in der Betriebsphase liegt auf zeitveränderlichen Parametern. Untersuchungen zur Charakterisierung dieser Effekte und Ansätze für den Abgleich werden erarbeitet. Dazu werden zunächst Messgrößen, Messorte und Messzeitpunkte analysiert und es wird untersucht, welche Methoden der Vorverarbeitung, Anregungsdetektion und Parameter-/Modellfehlerbewertung angewandt werden müssen. Anschließend werden Methoden zur wirtschaftlichen Messung basierend auf bereits verfügbaren Steuerungsdaten und Daten zusätzlicher Sensoren erarbeitet. Der Funktionsnachweis erfolgt anhand des Parameterabgleichs an einer Produktionsmaschine.
Kontakt:
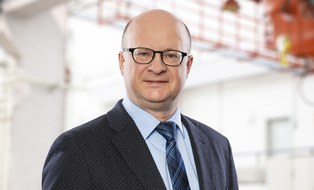
Wissenschaftlicher Mitarbeiter
NameHerr Dr.-Ing. Bernd Kauschinger
Eine verschlüsselte E-Mail über das SecureMail-Portal versenden (nur für TUD-externe Personen).
Professur für Werkzeugmaschinenentwicklung und adaptive Steuerungen
Professur für Werkzeugmaschinenentwicklung und adaptive Steuerungen
Besuchsadresse:
Kutzbach-Bau, Raum 106 Helmholtzstraße 7a
01069 Dresden
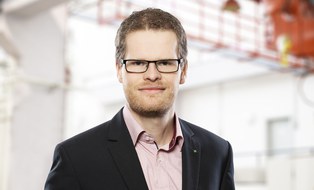
Wissenschaftlicher Mitarbeiter
NameHerr Dr.-Ing. Arvid Hellmich
Gruppenleiter
Eine verschlüsselte E-Mail über das SecureMail-Portal versenden (nur für TUD-externe Personen).
Besuchsadresse:
Technologiezentrum "Universelle Werke" Dresden, Raum 4.34.4 Zwickauer Str. 46
01069 Dresden