Development of a modular seal tester for heat and ultrasonic sealing as well as a test method for determining the optimum sealing parameters of films under application conditions
The heat sealing process and the ultrasonic sealing process are the most commonly used technologies for sealing film packaging in the consumer goods industry. In heat sealing, the film layers are heated by sealing bars on the outer sides of the films. Heat conduction heats the contact zone of the two films to such an extent that the films melt and flow into each other. During ultrasonic sealing, the film layers are periodically compressed at high frequency. The contact zone heats up as a result of internal friction and friction at the contact surfaces of the foils, and the foils fuse.
The project intends to develop a combined laboratory sealing and testing device for testing the seam strength of packaging films during heat sealing and ultrasonic sealing, as well as an associated test procedure that automatically generates the design of experiments and guides the operator through the tests.
The aim of the project is divided into two sub-aims:
- Development of a modular testing device for heat sealing process and ultrasonic sealing process, which achieves the required short sealing times and high sealing forces
- Development of a corresponding test and evaluation procedure, which can be controlled by a suitable test sequence in dependence on the technical boundary conditions of the packaging process and the material properties of the packaging film, to determine the optimum operating points for the respective sealing processes.
Sub-aim 1 is being worked on by Willi Kopp e.K. Verpackungssysteme and sub-aim 2 by the Chair of Processing Machines and Processing Technology at the TUD Dresden University of Technology.
Project funding:
The research project is supported by the the Federal Ministry for Economic Affairs and Climate Action through the program "Zentrales Innovationsprogramm Mittelstand".
Project duration:
06.2023 - 05.2025
Project management and contact:
Project leader: Dr.-Ing. Max Britzke
Project management: Dipl.-Ing. Phillip Rosenbusch
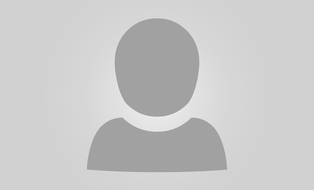
Processing Systems
NameDipl.-Ing. Phillip Rosenbusch
Natural Fiber Based Functional Structures
Send encrypted email via the SecureMail portal (for TUD external users only).