CONCRETE 3D PRINTING at the Institute of Construction Management
The TU Dresden has been developing the concrete 3D printing process "CONPrint3D® - Concrete ON-site 3D-Printing" since 2014 and is thus represented in the world's top research. A modified truck-mounted concrete pump (ABP) with an integrated print head forms the technical basis of the new construction method. The ABP is to layer the pasty fresh concrete geometrically precisely and continuously. As an in-situ concrete construction method, the technology is to be applied directly on the construction site. A specially developed normal concrete with rock aggregate up to 16 mm maximum grain size is used as the pressure material. Monolithic, fully filled concrete structures (solid construction printing) will be produced. The print head is to be designed in such a way that sharp-edged wall joints (wall corners, -T-joints and -crossings) can be printed. This clearly sets CONPrint3D® apart from other research activities that primarily print smaller concrete strands "as an endless loop" and produce "round" corners in the process.
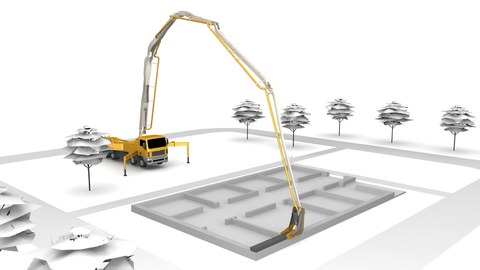
CONPrint3D®-Konzept
The TU Dresden research team consists of three partners. The endowed professorship for construction machinery deals with the adaptation of machinery technology. The Institute for Building Materials is developing the special concrete technology. The economic implementation on the construction site and productivity of the application as well as optimised data management are ensured by the Institute of Construction Management.
In order to be able to autonomously produce structures using concrete 3D printing, the demanding boundary conditions of the construction processes must be mastered in terms of content and machinery. The construction machine must be controlled via specially prepared data structures and have a sophisticated data management system. A BIM building model that contains both geometric and material-specific information will serve as the basis. The data required for the concrete 3D printing process will be extracted from the BIM model and then converted into machine control data via a continuous digital process chain. Currently, the data flow for concrete 3D printing is not continuous. The Institute of Construction Management is working on the modification of the data process chain.
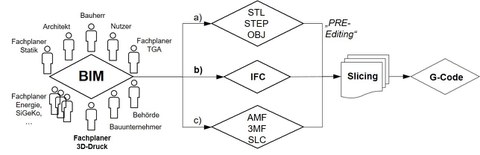
Modifizierung der Datenprozesskette für den Beton-3D-Druck, Quelle: Krause, Otto 2019
In a first development step, CONPrint3D® is to replace traditional masonry construction. Significant savings in terms of construction time and construction costs are possible. (Otto, Kortmann, Krause 2020) The potential of concrete 3D printing is enormous. The autonomous implementation will be a scientific and technical challenge in the coming years. A specially developed trainer is available for the practical investigation of the technological implementation of CONPrint3D®. The trainer allows a maximum printing speed of 15.0 cm/s (9.0 m/min, 540 m/h). The print aperture can be rotated through 360° and, in the picture shown, has an outlet and at the same time print geometry of (W - H =) 15.0 cm - 5.0 cm. The concrete layers printed in this way are unique worldwide. In particular, the height of the printed layer of 5.0 cm is a unique selling point compared to other research activities.
The research activities for CONPrint3D® have been continued steadily since 2014 and are currently at a stage that allows reliable statements and assumptions to be made about subsequent implementation on the construction site. The research projects CONPrint3D®, CONPrint3D® Ultralight, digiCON2 which have already been completed, are to be expanded to include further development activities, especially with regard to application-ready data management and practical solutions for the integration of reinforcement structures. In addition, a house prototype made of printed concrete with the dimensions (L) 6.0 m ∙ (W) 3.0 m ∙ (H) 2.7 m is to be created on a scale of 1:1 by the end of 2020.
Events on the topic of concrete 3D printing and other digital concrete construction methods