Stress redistribution in the very high cycle fatigue range
Table of contents
Project data
Titel | Title Numerische und experimentelle Untersuchungen zu den Spannungsumlagerungen von ermüdungsbeanspruchten Betonbauteilen im Very-High-Cycle-Fatigue-Bereich | Numerical and experimental investigations on stress redistribution in concrete structures subjected to fatigue loading in the very high cycle fatigue range Förderer | Funding Deutsche Forschungsgemeinschaft (DFG) Zeitraum | Period 09/2019 – 06/2023 Projektleiter | Project manager Prof. Dr.-Ing. Steffen Marx Team | Team Dennis Birkner, M.Sc. René Wallschläger (Versuchsdurchführung | Test conduction) |
Report from the year book 2023
Lifetime estimation of wind energy tower structures
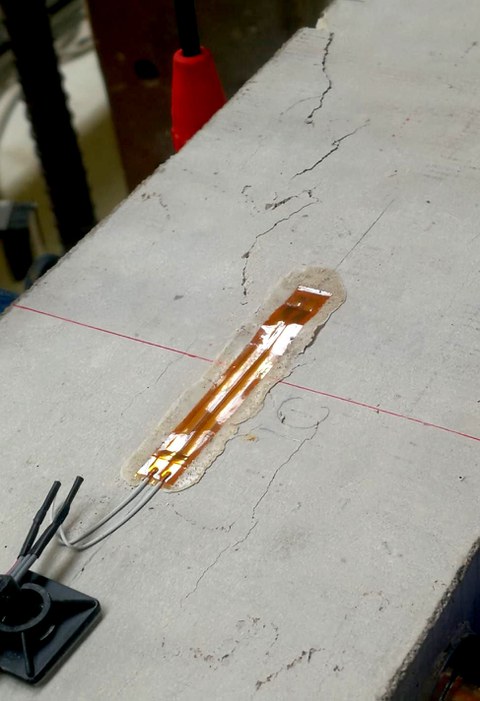
Strain gauge glued at the cracked concrete compression zone after the fatigue test
The expansion of renewable energies, especially wind energy, is a key element in reducing CO2 emissions. Research is needed for resource-efficient manufacturing of tower structures. For hub heights exceeding 100 meters, hybrid towers made of prestressed concrete segments are the most suitable construction. However, precise knowledge of the fatigue behavior of concrete is required for this purpose. Existing literature predominantly focuses on small-scale cylindrical specimens, but the results of which have limited applicability to large-scale components. In this project, large-scale tests on cyclically flexural loaded, prestressed concrete beams were conducted, along with accompanying experiments on small-scale cylindrical specimens, and numerical simulations of the beam tests. The numerical material model was developed based on an additive strain model within the finite element software ANSYS Mechanical, implemented in an iterative calculation process. Concrete strains in this model are composed of four components: elastic, plastic, viscous, and temperature-induced strains. Thus, the combined influence of these components on the fatigue behavior of concrete was investigated.
In the large-scale tests, fatigue failure was induced in the beam specimens, characterized by the development of cracks parallel to the compressive normal stress and partial spalling of the concrete compression zone, which was subjected to the highest stress cycle range. It was observed that this occurred after significantly more load cycles than in the accompanying cyclic tests on axially loaded concrete cylinders with the same stress cycle range. This can be attributed to stress redistribution that occurred within the cross-section due to fatigue-induced material degradation and stiffness reduction in the highly stressed edge regions. In the accompanying tests, material parameters for the numerical model were determined, which were subsequently used to simulate the beam tests. The model successfully replicated the observed effects of stiffness degradation, stress redistribution, and the resulting extension of the fatigue life. Thus, the model can be used for further investigations into the service life of fatigue-loaded concrete components.
Report from the year book 2022
Life cycle analysis in a short time frame
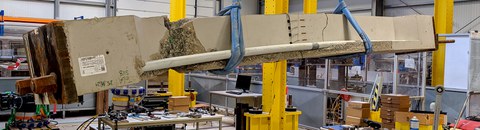
Dismantled and damaged beam specimen
Cyclic loads from wind and waves lead to successive material fatigue in the structural components of wind turbines over the course of their lifetime. This initially occurs in the more stressed edge zones and, as a consequence of the resulting change in stiffness distribution, the stresses are redistributed to the inner part of the cross-section. This effect is examined in more detail in this project by means of experimental and numerical investigations.
The developed numerical model simulates the stiffness changes in the cross-section based on an associated degradation function, which was determined by evaluating cyclic tests on concrete cylinders. Occurring viscous and plastic strains of concrete can also be modelled. On the experimental level, tests were carried out on large-scale concrete beams with a span of 4.0 m and accompanying fatigue, creep and static tests on concrete cylinders. The project focused on the investigation of two concrete types with strength classes C30/37 and C80/95. The evaluation of the accompanying tests yielded the material properties of the investigated concretes and they could then be taken into account in the numerical model.
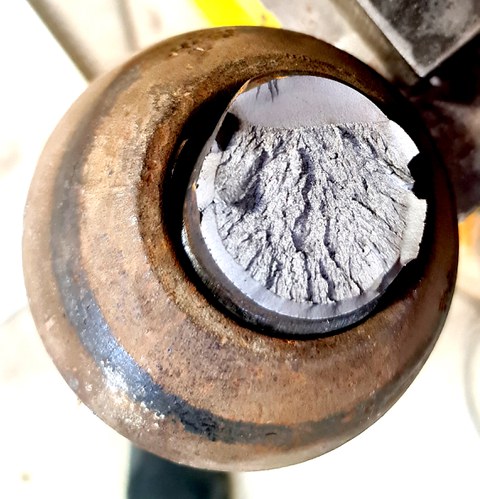
Detailed view of an unexpected fatigue failue of a threaded rod
The beam tests led to intended fatigue failure in the specimens. The prestressed beams were designed in such a way that the largest stress range due to fatigue loading occurred at the upper cross-sectional edge in midspan. In the tests, this then led to concrete spalling with a thickness of several centimeters. This change in cross-section occurred abruptly in some cases and, due to the high test frequency of 14 to 16 Hz, the load application could not be stopped immediately, so that the residual cross-section of some beam specimens was also destroyed. The beams in this project were designed without reinforcement in midspan. The question whether an existing reinforcement changes the load-bearing behavior is part of the investigations of the BMWK funded joint project WinConFat-Structure (grant no. 03EE3060), which started in May 2022.
In the next step, the results of the beam tests will be taken into account in the numerical model in order to create a validated investigation method that can be used to analyze the service life and load-bearing behavior of components subjected to fatigue loading.
Report from the year book 2021
Positive effects from fatigue?
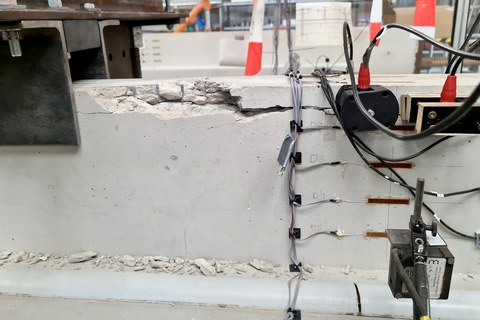
Detailed view of a fatigue damage
In structures such as wind turbines and railroad bridges, cyclic stresses occur in the cross-section during the service life, leading to successive material fatigue. As a result, the material stiffness decreases, especially in the edge zones, which leads to a redistribution of the stress to the inner part of the cross-section. This effect is investigated in this project utilizing finite element simulations and experimental tests.
For the finite element simulations, an additive strain model for fatigue loaded concrete is being developed further. The concrete strains consist of four components: an elastic strain component as a reversible deformation due to the external loads, a viscous strain component from time-dependent material effects, a plastic strain component that describes irreversible deformations due to material degradation, and a temperature strain component for the deformation due to heating. In addition, a coupling of the elastic modulus of the individual elements to their damage state was implemented. The material model was implemented in ANSYS Mechanical in an iterative calculation sequence. In the calculation, the individual load cycles of the fatigue loading are combined in load collectives with equal load levels and applied quasi-statically to the system. Then, the individual strain components and the updated stiffnesses are calculated for each element and the following load collective is applied. The model parameters are calibrated through experimental investigations on small-scale cylindrical and large-scale beam specimens. Since the stress redistributions in the concrete beams can lead to an increase in the bearable load cycles to more than 107, the beam tests are carried out in a resonance-based testing facility. In this way, the required large stresses can be generated with a comparatively low excitation force and the very-high-cycle fatigue range can be achieved in less than a week with an excitation frequency of around 18 Hz.
The results of the research project make it possible to take a step towards a more realistic design and thus towards leaner, more economical and more cost-effective designs of fatigue-loaded concrete structures.
Report from the year book 2020
Large concrete beams in resonance
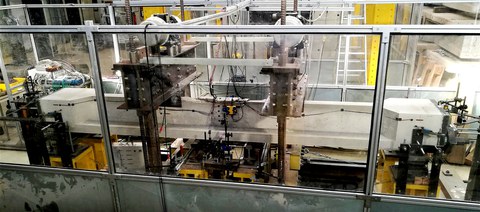
Concrete beam during fatigue loading in a resonance-based testing facility
Structures such as wind turbines and railway bridges are subjected to cyclic loads throughout their lifetime, which leads to successive material degradation. The reduced stiffness conditions cause a stress redistribution within the cross-section of the structures. So far, this effect has only been considered in a very simplified manner in the structural design.
This project aims to specifically and systematically investigate stress redistributions occurring in concrete structures subjected to fatigue loads. Within this framework, both finite element simulations and experimental investigations are carried out. An additive strain model for fatigue loaded concrete is refined for the FE simulations. The numerical model can simulate local stiffness changes as well as plastic and visco-elastic deformations. The model parameters are calibrated using experimental investigations enabling a more accurate simulation of the material behaviour subjected to fatigue loads. The experimental investigations are carried out on large-scale specimens since local stiffness changes and stress redistributions can be better determined this way. For this purpose, a resonance testing facility is used in which the concrete beams are excited in their first natural bending frequency using oriented imbalance motors. This makes it possible to reach the required large stresses with a comparatively low excitation force. The test setup is designed to have an excitation frequency of approximately 18 Hz to reach the very-high-cycle fatigue range with over 107 load cycles in less than one week of test duration. This is essential for the test execution since the stress redistributions lead to a very large number of cycles to failure of the concrete beams. The functionality of the test setup has already been confirmed in previous tests on similar specimens. To determine the material parameters for the numerical model, experiments on cylindrical specimens are carried out additionally to the large-scale investigations.
The results of the project allow a step towards a more accurate design and thus towards more slender, economical and cost-effective designs of fatigue loaded concrete structures.