Spannungsumlagerung im Very-High-Cycle-Fatigue-Bereich
Inhaltsverzeichnis
Projektdaten
Titel | Title Numerische und experimentelle Untersuchungen zu den Spannungsumlagerungen von ermüdungsbeanspruchten Betonbauteilen im Very-High-Cycle-Fatigue-Bereich | Numerical and experimental investigations on stress redistribution in concrete structures subjected to fatigue loading in the very high cycle fatigue range Förderer | Funding Deutsche Forschungsgemeinschaft (DFG) Zeitraum | Period 09/2019 – 06/2023 Projektleiter | Project manager Prof. Dr.-Ing. Steffen Marx Team | Team Dennis Birkner, M.Sc. René Wallschläger (Versuchsdurchführung | Test conduction) |
Bericht aus dem Jahrbuch 2023
Ermüdungsversuche an Tragstrukturelementen von Windenergieanlagen
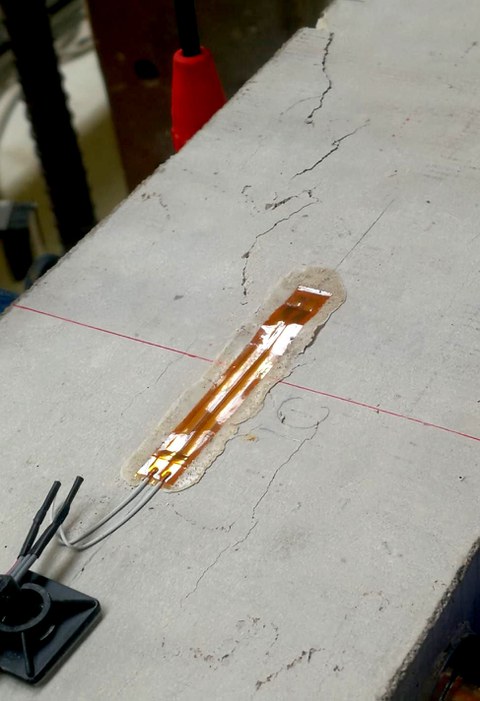
Detailaufnahme eines DMS in der gerissenen Betondruckzone nach dem Ermüdungsversuch
Ein zentraler Baustein zur Reduktion von CO2-Emissionen ist der Ausbau der Windenergie. Forschungsbedarf besteht dabei in der ressourceneffizienten Herstellung der Turmstrukturen. Bei Nabenhöhen von über 100 Metern sind Hybridtürme aus vorgespannten Stahlbetonsegmenten die geeignetste Konstruktion, für die jedoch eine genaue Kenntnis des Ermüdungsverhaltens erforderlich ist. In der Literatur existieren überwiegend Untersuchungen an kleinformatigen zylindrischen Probekörpern, deren Ergebnisse nur bedingt auf die großmaßstäblichen Bauteile übertragen werden können. Im Rahmen dieses Vorhabens wurden daher zum einen Großversuche mit zyklisch biegebeanspruchten, vorgespannten Betonbalken sowie Begleitversuche an zylindrischen Probekörpern und zum anderen numerische Simulationen der Balkenversuche durchgeführt. Das numerische Materialmodell wurde aufbauend auf einem additiven Dehnungsmodell im Finite-Elemente-Programm ANSYS Mechanical in einem iterativen Berechnungsablauf implementiert. Die Betondehnungen setzen sich hierbei aus vier Anteilen zusammen, einem elastischen, einem plastischen, einem viskosen und einem Temperaturdehnungsanteil. Somit konnte der kombinierte Einfluss der Anteile auf das Ermüdungsverhalten von Beton dargestellt werden.
In den Balkenversuchen konnte bei den Probekörpern ein Ermüdungsversagen der Druckzone erzeugt werden, das sich an dieser Stelle durch Risse parallel zur Normalspannung sowie teilweise Abplatzungen einstellte. Es zeigte sich, dass dies erst nach deutlich mehr Lastwechseln eintrat als bei den Betonzylindern in den Begleitversuchen mit derselben Spannungsschwingbreite. Dies ist auf die Spannungsumlagerung zurückzuführen, die im Querschnitt aufgrund der ermüdungsbedingten Materialdegradation der stark beanspruchten Randbereiche stattfand. In den Begleitversuchen wurden die Materialparameter für das numerische Modell ermittelt, mit dem im Anschluss die Balkenversuche nachgerechnet wurden. Es konnten die in den Versuchen beobachteten Effekte der Steifigkeitsdegradation und Spannungsumlagerung und die daraus resultierende Lebensdauerverlängerung nachgebildet werden. Das Modell kann somit für weitergehende Lebensdaueruntersuchungen von ermüdungsbeanspruchten Betonbauteilen verwendet werden.
Bericht aus dem Jahrbuch 2022
Lebensdaueruntersuchungen in kurzen Zeiträumen
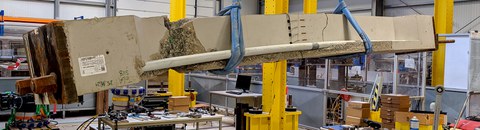
Ausgebauter und beschädigter Balkenprobekörper
Die zyklischen Beanspruchungen aus Wind- und Wellenlasten führen über die Lebensdauer zu einer sukzessiven Materialermüdung in den Tragstrukturen von Windenergieanlagen. Diese tritt zunächst in den stärker beanspruchten Randbereichen auf, und als Folge der daraus resultierenden veränderten Steifigkeitsverteilung lagern sich die Spannungen ins Querschnittsinnere um. In diesem Vorhaben wird dieser Effekt anhand von experimentellen und numerischen Untersuchungen näher betrachtet.
Das entwickelte numerische Modell bildet die Steifigkeitsveränderungen im Querschnitt über eine zugrundeliegende Degradationsfunktion ab, die durch die Auswertung von zyklischen Versuchen an Betonzylindern aufgestellt wurde. Auftretende viskose und plastische Betondehnungen können ebenfalls abgebildet werden. Auf experimenteller Ebene wurden Versuche an großformatigen Betonbalken mit einer Spannweite von 4,0 m sowie begleitend Ermüdungs-, Kriech- und statische Versuche an Betonzylindern durchgeführt. Im Fokus des Vorhabens stand die Untersuchung von zwei Betonen der Festigkeitsklassen C30/37 und C80/95. Anhand der Begleitversuche konnten die Materialeigenschaften der untersuchten Betone ermittelt und im numerischen Modell berücksichtigt werden.
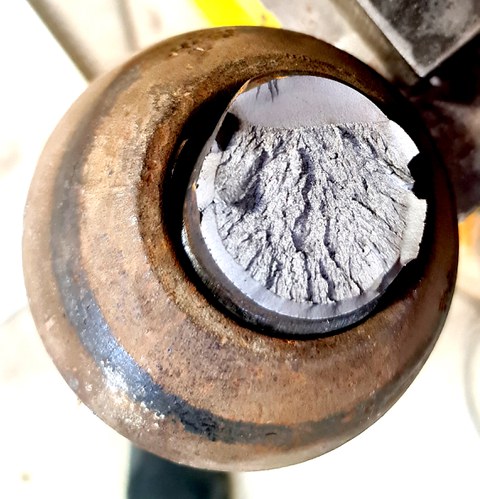
Detailaufnahme eines ungeplanten Ermüdungsbruchs in einem Gewindestab
In den Balkenversuchen konnte, wie vorgesehen, ein Ermüdungsversagen erreicht werden. Die vorgespannten Balken waren so ausgelegt, dass am oberen Querschnittsrand in Feldmitte die größte Spannungsschwingbreite infolge der Ermüdungsbeanspruchung auftrat. Diese führte dann zu Betonabplatzungen mit einer Dicke von mehreren Zentimetern. Diese Querschnittsänderung trat zum Teil schlagartig auf. Aufgrund der hohen Prüffrequenz von 14 bis 16 Hz konnte der Versuch nicht sofort gestoppt werden, sodass bei einigen Balkenprüfkörpern der Restquerschnitt ebenfalls zerstört wurde. Die Balken in diesem Vorhaben waren in Feldmitte ohne schlaffe Bewehrung ausgeführt. Die Frage, inwieweit eine vorhandene Bewehrung das Tragverhalten ändert, ist Teil der Untersuchungen des nachfolgenden, vom BMWK geförderten Verbundvorhabens WinConFat-Structure (FKZ 03EE3060).
Im nächsten Schritt fließen die Ergebnisse der Balkenversuche in das numerische Modell mit ein, um eine validierte Untersuchungsmethode zu schaffen, mit der die Lebensdauer und das Tragverhalten von ermüdungsbeanspruchten Betonbauteilen analysiert werden können.
Bericht aus dem Jahrbuch 2021
Positive Effekte durch Ermüdung?
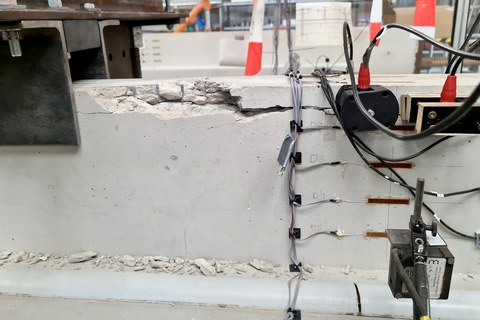
Detailaufnahme eines Ermüdungsschadens
Bei Bauwerken wie Windenergieanlagen und Eisenbahnbrücken kommt es während der Nutzungsdauer zu zyklischen Beanspruchungen im Querschnitt, die zu einer sukzessiven Materialermüdung führen. Hierbei verringert sich vor allem in den Randbereichen die
Materialsteifigkeit, wodurch eine Umlagerung der Beanspruchung ins Innere der Bauteilquerschnitte geschieht. Dieser Effekt wird in diesem Projekt mit Hilfe von Finite-Elemente-Simulationen und experimentellen Versuchen untersucht.
Für die Finite-Elemente-Simulationen wird ein additives Dehnungsmodell für ermüdungsbeanspruchten Beton weiterentwickelt. Die Betondehnungen bestehen dabei aus vier Anteilen: einem elastischen Dehnungsanteil als reversible Verformung infolge der äußeren Lasten, einem viskosen Dehnungsanteil aus zeitabhängigen Materialeffekten, einem plastischen Dehnungsanteil, der irreversible Verformungen infolge Materialzerrüttung beschreibt, und einem Temperaturdehnungsanteil für die Verformung infolge Erwärmung. Zusätzlich wurde eine Kopplung des Elastizitätsmoduls der einzelnen Elemente an deren Schädigungszustand implementiert. Das Materialmodell wurde in ANSYS Mechanical in einem iterativen Berechnungsablauf umgesetzt. Bei der Berechnung werden die einzelnen Lastwechsel der Ermüdungsbeanspruchung in Lastkollektiven mit gleichen Lastniveaus zusammengefasst und quasi-statisch auf das System aufgebracht. Anschließend werden elementweise die einzelnen Dehnungsanteile und die aktualisierten Steifigkeiten berechnet und das folgende Lastkollektiv appliziert. Die Modellparameter werden mit Hilfe von experimentellen Untersuchungen an kleinformatigen zylindrischen und großformatigen Balkenprobekörpern kalibriert. Da die Spannungsumlagerungen bei den Betonbalken zu ertragbaren Lastwechselzahlen von über 107 Lastwechseln führen können, werden die Balkenversuche in einem Resonanzprüfstand durchgeführt. So können die erforderlichen großen Beanspruchungen mit einer vergleichsweise geringen Erregerkraft erzeugt und der Very-High-Cycle-Fatigue-Bereich bei einer Erregerfrequenz von etwa 18 Hz in unter einer Woche erreicht werden.
Die Erkenntnisse des Forschungsvorhabens ermöglichen den Schritt in Richtung einer realitätsnäheren Bemessung und damit zu schlankeren, wirtschaftlicheren und kostengünstigeren Ausführungen ermüdungsbeanspruchter Betonbauwerke.
Bericht aus dem Jahrbuch 2020
Große Betonbalken in Resonanz
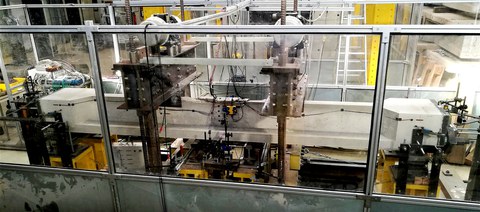
Betonbalken im Ermüdungsversuch in einem Resonanzprüfstand
Bauwerke wie Windenergieanlagen und Eisenbahnbrücken sind während ihrer gesamten Lebensdauer zyklischen Beanspruchungen ausgesetzt, die zu einer sukzessiven Materialzermürbung führen. Diese veränderten Steifigkeitsverhältnisse haben eine Umlagerung der Beanspruchung innerhalb der Bauteilquerschnitte zur Folge. Dieser Effekt wird in der Bauwerksbemessung bislang nur stark vereinfacht betrachtet.
In diesem Projekt sollen gezielt und systematisch die auftretenden Spannungsumlagerungen von ermüdungsbeanspruchten Betonbauteilen untersucht werden. In diesem Rahmen werden sowohl Finite-Elemente-Simulationen als auch experimentelle Versuche durchgeführt. Für die FE-Simulationen wird ein additives Dehnungsmodell für ermüdungsbeanspruchten Beton weiterentwickelt. Das numerische Modell ist in der Lage sowohl lokale Steifigkeitsänderungen als auch plastische und visko-elastische Verformungen zu simulieren. Die Modellparameter werden mit Hilfe von experimentellen Untersuchungen kalibriert, sodass eine realitätsnähere Simulation des Materialverhaltens unter Ermüdungsbeanspruchungen möglich wird. Die Versuche werden an großformatigen Prüfkörpern durchgeführt, da die lokalen Steifigkeitsänderungen und Spannungsumlagerungen so besser erfasst werden können. Hierfür wird ein Resonanzprüfstand verwendet, in dem die Betonbalken mit Hilfe von gerichteten Unwuchtmotoren in ihrer ersten Biegeeigenfrequenz angeregt und in Resonanz versetzt werden. So können die erforderlichen, großen Beanspruchungen mit einer vergleichsweise geringen Erregerkraft erreicht werden. Der Versuchsstand wird so ausgelegt, dass die Beanspruchungsfrequenz bei etwa 18 Hz liegt, sodass der Very-High-Cycle-Fatigue-Bereich mit über 107 Lastwechseln in unter einer Woche Versuchsdauer erreicht wird. Dies ist für die Versuchsdurchführung von wesentlicher Bedeutung, da die Spannungsumlagerungen zu sehr hohen ertragbaren Lastwechselzahlen bei den Betonbalken führen. In vorhergehenden Untersuchungen an ähnlichen Prüfkörpern konnte die Funktion des Prüfstands bereits nachgewiesen werden. Begleitend zu den großformatigen Untersuchungen werden zur Bestimmung der Materialparameter für das numerische Modell Versuche an zylindrischen Prüfkörpern durchgeführt.
Die Erkenntnisse des Forschungsvorhabens ermöglichen den Schritt in Richtung einer realitätsnäheren Bemessung und damit zu schlankeren, wirtschaftlicheren und kostengünstigeren Ausführungen ermüdungsbeanspruchter Betonbauwerke.