Development and optimization of resonance-based test methods | ResoWind
Table of contents
Project data
Titel | Title TP ABT.Reso.TUD: Entwicklung und Optimierung resonanzbasierter Prüfmethoden für axial- und biegebeanspruchte Tragstrukturelemente im Verbundvorhaben ResoWind: Resonanzbasierte Prüfmethoden für kosten- und zeitoptimierte Lebensdaueruntersuchungen an Tragstrukturelementen von Windenergieanlagen | Subproject ABT.Reso.TUD: Development and optimization of resonance-based test methods for structural elements under axial and bending loads within the joint research project ResoWind: Resonance-based testing methods for cost- and time-optimized lifetime studies on support structure elements of wind turbines Förderer | Funding Bundesministerium für Wirtschaft und Klimaschutz (BMWK) Zeitraum | Period 12/2019 – 11/2022 Teilprojektleiter | Subproject manager Prof. Dr.-Ing. Steffen Marx Team | Team Dipl.-Ing. Clara Schramm René Wallschläger (Versuchsdurchführung | Test conduction) Projektpartner | Project partners Testzentrum Tragstrukturen Hannover (TTH), Leibniz Universität Hannover | Fraunhofer-Institut für Windenergiesysteme (IWES), Bremerhaven Assoziierte Partner | Associated partners Bauunternehmung Gebr. Echterhoff GmbH & CO. KG, Westerkappeln | Vallourec Deutschland GmbH, Düsseldorf |
Concluding summary
Wind turbines can experience load cycles > 107 over the course of their 25-year service life. Large-scale cyclic tests are required to verify their structural safety. However, these tests are very energy- and time-intensive using conventional hydraulic testing technology. By using electric unbalance motors as actuators, on the other hand, very high load frequencies close to the natural frequency of the test specimen can be achieved. The resonance-based dynamic enhancement of the load level is highly efficient for reasons of energy and time savings.
In this project, the resonance-based testing principle was extended by two applications and validated on two demonstrators. Demonstrator I enabled high-cycle tests on axially loaded test specimens under a defined mean load. Force amplitudes of up to approx. 300 kN at an excitation frequency of approx. 14 Hz were achieved in compression and tension swelling tests. Utilization of the dynamic magnification due to the resonance effect in combination with a leverage effect led to a 45-fold increase in forces.
The Demonstrator II was developed for cyclic tests on test specimens subjected to bending. The special feature here was its vibration node support, in which the support positions corresponded to the vibration nodes of the natural frequency to be excited. In the vibration nodes, the displacements and consequently also the support forces were zero. With an excitation just below the natural frequency, the support forces in the tests could be reduced to approx. 10 % compared to the acting force, so that the transmission of vibrations into the environment was minimal.
In this project, we were able to demonstrate the versatility and efficiency of the resonance-based testing method with unbalance drives and thus facilitate future fatigue research on large components.
Report in the annual report 2022
Innovative resonance testing facilities
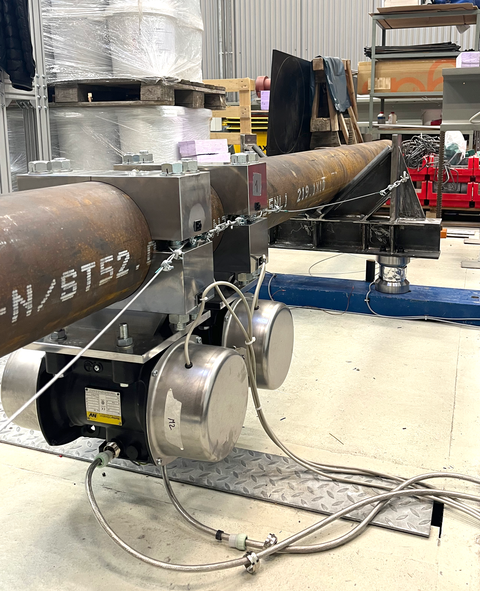
Centered unbalanced motors at Demonstrator II
Wind turbines are subject to high cyclic loads over the course of their 25-year lifetime. Especially offshore turbines, due to additional wave load, can reach more than > 107 load cycles. Therefore, experimental fatigue tests of structural wind turbine elements are of great importance. Testing with conventionally servo-hydraulic actuators is very cost-intensive due to the limited test frequency. For this reason, a resonance-based testing method with synchronized unbalanced motors was developed at Leibniz University Hanover. By using this method it is possible to generate cyclic loads with high loading frequencies > 15 Hz and low energy consumption at the same time.
In order to expand the application possibilities of the resonance test method for large component tests, two demonstrators were developed within the framework of the project: Demonstrator I for axially loaded structural elements and Demonstrator II for structural elements under bending. Demonstrator I operates as a cantilever system with hinged bearings. The specimen is placed either below (compression test) or above (tension test) the cantilever beam. Vertically prestressed tension springs were used to apply a specific mean stress to the specimen. At the free end, two contra-rotating unbalanced motors generate a vertically directed oscillation. Demonstrator II is designed as a four-point bending test and is also excited in the vertical direction by two contra-rotating unbalanced motors. To avoid vibrations to the surrounding area, the specimen supports are placed in the vibration nodes of its natural frequency. With an excitation frequency just below the natural frequencies, the reaction forces can thus be greatly reduced and problematic vibration transmission avoided.
First trials showed that fatigue tests under compressive and tensile loads can be realised with the Demonstrator I. The axial fatigue load could be kept constant to the specimen during the test. Demonstrator II confirmed the enormous effect of the support position near the vibration nodes on reducing the reaction forces.
Report in the annual report 2021
Resonance cleverly used
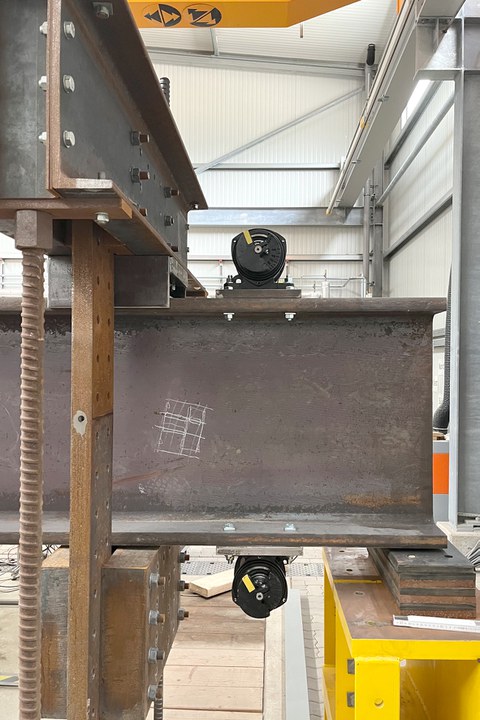
Two imbalanced rotors to generate vertical forces to Demonstrator II
Experimental testing of big structural elements, such as those used in wind energy turbines, is extremely time-consuming and expensive. In particular, the study of fatigue behaviour, which is of great importance as a result of high cyclic stresses due to wind and shaft loading, can become very inefficient with conventional servo-hydraulic actuators. The idea: resonance-based testing. Therefore, the Institute of Concrete Construction of the University of Hannover has already developed a resonance-based testing rig. To imply the excitation to the system simple imbalanced rotors were used to generate cyclic fatigue loads with minimal energy input and simultaneously high excitation frequency.
Within this project, the mission is to continue the research on the resonant testing method and to make it more practicable for different types of applications. Upon completion it will be possible to do experimental testing of large structural elements at high frequencies (20–50 Hz) and with a very large number of cycles (N > 107) in an energy and time-saving way.
To achieve the project goals, two demonstrators will be developed. Demonstrator I, for testing specimens under axial tensile or compressive loading and Demonstrator II for testing structural elements subjected to bending. By using two imbalanced rotors, which rotate in opposite directions a vertical oscillation will be generated. The excitation frequency of the rotors is close to the first natural bending frequency of the system. Due to the resonance effect, a relatively small excitation force will result in strong reaction forces. The Demonstrator I functions as a cantilever system with an articulated bearing. Vertically prestressed tension springs are used to apply a specific stress to the specimen around which the system oscillates. The specimens are placed either below (compression test) or above (tension test) the cantilever beam. After numerical considerations and the analysis of the testing rig, the realisation in the laboratory will follow. The most challenging aspect of the design of the Demonstrator II is to find its nodes of deflection. The aim here is to identify the vibration nodes of the specimen (a steel tube) so that a critical vibration transmission to the environment can be reduced to a minimum.
Report in the annual report 2020
Testing by resonance
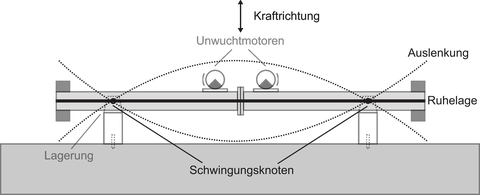
Schematic illustration of a beam support in its oscillation nodes in a resonance-based test facility
During their 20 years-service life, wind turbines are subjected to high dynamic loads. Especially offshore turbines, subjected to both wave and wind loads, are exposed to load cycles as high as 107. Therefore the research on the fatigue behaviour of structural elements of offshore wind turbines is of great importance.
Until now high and ultra-high cycle fatigue tests for service life studies have been performed solely on small-scale specimens. Due to size effects, only large-scaled testing provides relevant measurement results that can be transferred to real structural scales. Fatigue tests of structural elements with high numbers of load cycles are commonly carried out with servo-hydraulic actuators. Because of the high energy demand and the limited loading frequencies of the actuators, this method is no longer efficient for tests on large structural elements. That’s why a resonance test rig was developed at the Institute of Concrete Construction of the Leibniz University Hanover. With this test method, based on synchronized imbalance rotors, it is possible to generate cyclic fatigue loading with minimum energy consumption and a high excitation frequency at the same time. However, the strong oscillations being transmitted to the test hall are limiting factors for resonance tests on large structural elements such as those used in the wind energy sector.
Within the framework of the joint project ResoWind in cooperation with the Fraunhofer Institute for Wind Energy Systems (IWES) and the Test Centre for Support Structures Hanover (TTH), the resonant testing method is being optimized to enable tests on large-scale structures. Demonstrators are being designed for fatigue-stressed support structures of offshore wind turbines. They enable tests at both axially (tensile and compressive) loaded and bending stressed structural elements. The focus of designing the resonant bending fatigue test is on the development of an oscillation node support. Consequently, the critical transmission of oscillations to the environment is being minimized. The demonstrators for axial compressive and tensile loads combine the advantage of low energy costs compared to conventional hydraulic testing technology with the flexibility to use test specimens with almost any geometry.