Jul 26, 2024
Integrated Planning for Additive Manufacturing Published in Journal Omega
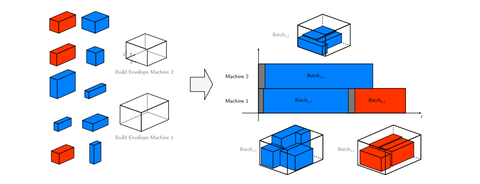
Schematische Darstellung des Planungsproblems
The Chair of Business Administration, esp. Industrial Management is pleased to announce the latest publication in the journal Omega, titled "Scheduling for additive manufacturing with two-dimensional packing and incompatible items." In this paper, Benedikt Zipfel, Prof. Rym M'Hallah from King's College London and Prof. Udo Buscher, explore an integrated planning problem that involves the packing process batches and sequencing these batches on available parallel additive manufacturing machines. The study pays special attention on the consideration of part families, which arise, for example, from different material or quality requirements of the components.
To solve the problem, a model formulation and a matheuristic are compared with appropriate methods from the literature. The results clearly show the superiority of the matheuristic over other approaches. Special thanks go to the transCampus initiative of TU Dresden and King's College London for supporting this research work.
https://doi.org/10.1016/j.omega.2024.103139
Abstract
Additive manufacturing technology can enable low-cost, efficient production of low-demand, highly-complex customized items with reduced lead time if production is judiciously planned. This paper addresses the assignment of requested items into batches and the scheduling of the batches onto 3D printers. The objective is to minimize the manufacturing makespan while satisfying items' compatibility, two-dimensional no-overlap and containment packing constraints within a batch, and machine's capability to manufacture a batch.
The problem is modeled as a mixed-integer linear program (MIP) that solves instances up to 100 items. For hard and large instances, this paper proposes a matheuristic that fathoms packings using a step-wise check procedure. Computational results reveal that the proposed heuristic improves the makespan of MIP solutions of hard instances by 12% on average, with improvements reaching up to 72% for instances with 150 items. They further show that the proposed heuristic finds the best makespan for 88% of all cases. Finally, we provide useful managerial insights for production flexibility and scheduling policies.