Mobile Agricultural Systems
Mobile agricultural CPPS will become a central part of advanced Farm Management Information Systems (FMIS) as they provide process feedback data and enable field-specific processing. Although agricultural production in open fields is exposed to high dynamic environmental influences, it is driven to optimize process and machine efficiency to maximize production quantity and quality to the highest extent. Upscaling machine features as a conventional strategy for such improvements runs up against reasonable or legal limits in terms of vehicle weight and dimensions. With the capabilities of advanced automation technology, smaller and swarm-organized machine systems can further improve efficiency while increasing flexibility. Today, this is the most promising approach to further improve the use of the technical installed process power.
However, managing such fleets requires optimized orchestration through advanced farming management and information systems (FMIS). The class of supervised highly automated machines will continue to evolve, with decreasing requirements for the presence and qualifications of the supervising operators. Work profiles of operators will transform from routine towards management and problem-solving activities.
With the increased complexity of agricultural CPPS, as well as frequently changing process and system properties, and increasing intransparency of the highly automated systems, operators can no longer adequately cover the system properties with their competencies. Nevertheless, they must be able to handle critical situations with complex intervention tasks that occur frequently, especially in shared autonomy systems. To cope with these changes, a sustainable and robust system design is needed that is specially tailored to and promotes people, their capabilities and competencies. Such a conducive design pursues the goal of enabling operators to act correctly in difficult decision-making or intervention tasks.
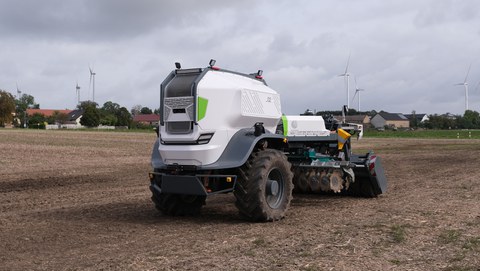
Illustration of the Feldschwarm demonstrator
Currently, the research and development of agricultural field robotics in many sizes and purposes is very dynamic and many machine prototypes and digital technologies are presented nowadays. With the “Feldschwarm” – a high-level automated power unit, capable of carrying multiple implements - the Technische Universität Dresden is part of this cutting-edge development.
The Feldschwarm Demonstrator
- Field test ready system of power unit and implements
- Demonstration of future tillage scenarios with highly automated machines
- Implemented advanced environmental detection and positioning technology, machine process simulation and highly automated control systems
- Implemented interfaces for human operation on-site and off-site
- Developed in a “Wachstumskern” cluster project