Research Projects
2nd Life Metal Component - Upcycling by Remanufacturing
While topics relating to energy as a resource have recently attracted a great deal of attention, materials as a resource often go unnoticed, even though both types of resources are essential for sustainable production technology. Industrialized nations in particular have a very high demand for materials - especially metals - which cannot be met by the energy-intensive production of new materials alone or with existing recovery strategies such as recycling. In future, goods in use must therefore be used directly as raw materials. The energy-intensive recycling step of returning the material to a melt will no longer be necessary and will be replaced by direct reuse of the material. However, production technology is currently not equipped for this new type of raw material extraction, meaning that there are no adequate process routes or chains that enable these resources to be processed. This is where the research project comes in, in order to develop a practicable process route for the largest proportion of metallic components - the sheet metal components - in which the areas of laser processing, material characterization, forming and planning interact in a complementary manner. As a result, it should be possible to sustainably manufacture a new component with a proportion of 75% from materials that have already been used at least once without a classic recycling step:
¾ previously used component + ¼ new semi-finished product ⇨ 2nd Life Metal Component
Contact person: Prof. Dr.-Ing. Alexander Brosius
Automated removal of 3D metal printing supports by milling - AutoSupport
The EU-funded project is a cooperation project with H+E Produktentwicklung GmbH. The aim of this project is the joint development of an innovative technology for the automated removal of support in 3D metal printing components by 5-axis milling to increase the automation of production capacity while reducing production costs. The project aims to use the latest research findings to solve a previously insurmountable problem of great economic importance.
Contact person: Dr. Martin Erler
Transregio TRR285 - Development of methods for mechanical joinability in versatile process chains
With the research of scientific methods in the field of joining technology, which lead to the establishment of efficient and resource-saving process chains with product diversity, different materials and construction methods, the CRC/Transregio is addressing an exciting and current topic. In view of the volatile demands of industry and consumers as well as accelerating development cycles in the globalized world, adaptability is one of the central topics of modern production technology
Further information can be found on the TRR285 website
Contact person: Christina Guilleaume
ProKI Dresden - Demonstration and Transfer Center for Artificial Intelligence in Forming Technology
The Federal Ministry of Education and Research (BMBF) is funding the visibility and development of artificial intelligence (AI) in production applications from October 1, 2022 to the end of 2024. Together with other partners in the "ProKI network", the common goal is to make it easier for manufacturing small and medium-sized enterprises (SMEs) to start using AI applications. At the Dresden center location, the focus is on forming technology.
Further information can be found on the ProKI website
Contact person: Christina Guilleaume
Experimental characterization and numerical analysis of the vibration strength-increasing effect of residual stresses in cross-rolled components
The production of components by forming leads to residual stresses which have a lasting effect on the component properties. Such internal stresses can, for example, have an effect on manufacturability and service life. As a rule, the aim is to avoid or reduce residual stresses, as they are primarily assigned negative properties. This ignores the fact that residual stresses can also be used in a targeted manner, for example to improve static and operational or fatigue strength, if they act in the opposite direction to the operational stress. Residual stresses are regarded as critical to quality in conventional manufacturing strategies. This is where the DFG Priority Program 2013 comes in and instead investigates the opportunities and possibilities of improving the properties of components through the in a targeted manner use of residual stresses.
Contact person: Christina Guilleaume
Complementary database generation for machine learning for quality prediction using the example of ring rolling
In order to use machine learning for manufacturing processes such as radial-axial ring rolling, data sets of good and reject parts must be recorded. This requires balanced data sets with regard to the ratio of good to reject parts. However, this is not the case with industrial data, which is why the method of data augmentation through synthetic data via simulation is used within the project. Within the field of radial-axial ring rolling, there is no fast, analytical simulation that can be used to generate a sufficiently large number of synthetically produced data sets with "rollings with form or process errors". For this reason, the research question of the extent to which a similar process can be investigated for the transfer to radial-axial ring rolling is being pursued.
Contact person: Christina Guilleaume
Development of a process for forming aluminum sheet materials at cryogenic temperatures
Lightweight materials such as aluminum alloys play an important role in weight reduction. However, their limited formability at room temperature poses a major challenge and restricts their use. Significant improvements in formability can be achieved, for example, through recovery annealing or hot forming with several process steps. However, this improvement in formability comes at the expense of various positive properties such as strength, component quality or costs. To avoid this, aluminum sheets can be formed at cryogenic temperatures, whereby the limit for adjusting the positive properties should be the subject of the research applied for here. The project deals with the combination of cryogenic sheet metal forming with the macro-structuring of the die and blank holder during deep drawing. A special, wave-like geometry of the forming tools minimizes the contact surface between the sheet metal and the tool in order to suppress the heat flow and thus the heating of the sheet metal. In addition, the local limit temperature of the sheet metal must be determined, above which the advantages of the cryogenic material properties of aluminum alloys come into play.
Contact person: Christina Guilleaume
Mechanical surface hardening of shafts and axles
Surface hardening measures are used in industry to increase dynamic load-bearing capacity. For example, components are only strengthened in a targeted manner in the highly stressed surface layer. In addition to (chemical) thermal methods, mechanical surface strengthening methods also offer immense potential. This study is dedicated to basic and application research on the subject of mechanical surface strengthening, in particular deep rolling and shot peening. It includes an international literature search, a user survey within the FVA, a patent search and selected on-site visits. The aim is to prepare the basic knowledge on the subject area within the FVA and to identify the need for further research.
Contact person: Christina Guilleaume
Development of a manufacturing technology for the production of permanent magnetic rings
Electromobility is a key building block for sustainable mobility strategies of the future and offers great opportunities for German industry. The focus on the economical production of bearing rings for plain bearings with improved properties and the results already achieved in the forming production of hybrid rings from various material combinations (e.g. bearing brass and rolling bearing steel), together with the lightweight construction requirements of electromobility, form the basis for the ZIM cooperation project.
The process to be developed will be used to produce composite rings with permanent-magnetic properties for use as rotors in electromagnetic drives. The development is divided into the fundamental focal points of further development of composite ring rolling with permanent magnets as well as material characterization and process modelling. The main quality criteria here are high composite strength and adjustment of the tolerances and imbalance of the ring as a component as well as the positioning of the permanent magnets in the composite ring. The aim is a process chain with as few process steps as possible and thus improved resource efficiency from the blank (forged part) to the finished hybrid ring.
Contact person: Christina Guilleaume
Thermomechanical ring rolling with predictive property control
Thermomechanical tangential profile ring rolling (TMR) is a process for producing near-net-shape ring geometries while simultaneously influencing the microstructure and hardness in a targeted manner through controlled process management with regard to forming and temperature. For this purpose, a combined approach of PID and predictive models is used, which makes it possible to utilize the existing process window in such a way that the target values for final geometry, microstructure and hardness can be achieved simultaneously. After validation on the real machine, it will be possible to transfer the control strategy for geometries and configurations to cases that cannot be realized on the existing rolling mill. An analysis of the process and system performance should enable the derivation of design principles and rules regarding the system architecture (actuators, sensors, modeling and control) for the implementation of thermomechanically controlled ring rolling.
Further information can be found on the SPP2183 websiteSPP2183 website
Contact person: Christina Guilleaume
Resilient deep drawing through macrostructured tools
The approach of using macrostructuring in the flange area to stabilize the deep drawing process and to increase robustness against changing input variables is useful in all sheet metal processing industries and in the associated toolmaking. The central aim is to make the results achieved in the basic research area fully available to industrial users. The methodology provided has an extremely high potential for implementation in the challenging industrial environment, as it addresses two of the main problems faced by companies. On the one hand, the robustness of deep drawing processes is highly relevant because it improves the degree of utilization of materials, minimizes the production of scrap and prevents damage to cost-intensive tools. On the other hand, with high cost pressure and ever shorter time periods between evolutions and new product developments, it is critical to transfer these quickly and reliably into safe processes.
Contact: Christina Guilleaume
Development of a utilizable slip bending system for the flexible production of straight and defined curved profiles in one process
In cooperation with FAD GmbH, the Chair is developing a slide bending machine for the flexible production of straight and defined curved profiles. The aim is to develop a system technology that makes it possible for the first time to reproducibly produce profiles of almost any length and shape in a single process step. The modular system is designed to be flexible in use thanks to short changeover times and can therefore be quickly adapted to customer-specific requirements. Due to its planned size, the slip bending system requires only a small amount of space and is also suitable for mobile use on construction sites, which means that special profiles required at short notice can be produced directly on site. Thanks to the variable loading of both a single blank and a coil, any number of pieces can be produced effectively. The planned modular principle also enables the production of a wide range of profile families and therefore offers a broad spectrum of applications.
Contact person: Christina Guilleaume
Experimental investigation and modeling of heat transfer during press hardening
Growing environmental awareness and legal requirements on CO2 emissions have led to a steady increase in the importance of lightweight construction in the automotive industry in recent decades. Press hardening of high-strength boron-manganese steels has become a standard process in the production of safety-relevant car body components. In this process, the semi-finished products are first fully austenitized above the material-specific AC3 temperature. After heat treatment, the red-hot sheet is transferred directly into the tool. Parallel to the subsequent forming process, the workpiece is quenched in the tool. If a critical quenching rate is exceeded during this process step, a complete martensitic microstructure is formed, allowing tensile strengths of more than 1500 MPa to be achieved. The temperature profile in the process chain and especially in the quenching process is therefore essential for the final mechanical properties of the press-hardened components.
The aim of the research project is to develop a fundamental understanding of the heat transport mechanisms involved in press hardening and to model them.
Contact person: Christina Guilleaume
Extension of the evaluation limits for determining flow curves in the uniaxial tensile test beyond uniform strain
The new method for evaluating tensile tests makes it possible to use the measurement data at higher degrees of deformation to determine yield curves compared to the conventional evaluation method. This allows the material behaviour to be described more precisely in the form of the flow curve used in the simulation, without the increased costs and time required by complex characterization methods. The innovative evaluation approach pursued here can therefore significantly increase the informative value of the virtual process description, for example in FEA, without investing considerable additional testing effort in material characterization. In concrete terms, this leads to a more cost-effective and faster process design as the most important basis for resource-efficient component and process design. In addition, considerable cost savings can be made in the tool design of forming processes, as the improved mapping accuracy means that reworking can be avoided and the familiarization phase can be shortened.
Contact: Christina Guilleaume
Advanced, flexible production and logistics planning based on volume pixels and agile transport load determination - FeLoVox
One of the main reasons for the growing planning effort is the increasing interdependence of production and logistics. In order to do justice to the interactions between intralogistics and production in production planning, expert knowledge (both in terms of process control and the handling of software and, if necessary, hardware) or experience from research and industry is required. This tends to lead to higher personnel and software costs and possibly longer planning phases. The FeLoVox R&D project aims to counter these challenges and risks and, by developing an automated, integrated approach, reduce planning costs, increase the quality of results and thus enable a broad range of solutions for SMEs.
Contact person: Dr. Martin Erler
Automated production costing - AFK
The aim of the R&D cooperation project is to develop a technology for automated production costing in order to drastically reduce the effort involved in calculating planned times and production costs, which is always necessary in machining production. The aim is to achieve fully automated production costing. The technology should enable economical, reliable and highly efficient planning of machining production. The approach dispenses with the conventional manual methods of production costing and determines production costs directly and fully automatically from the CAD data already available for the components. The planned R&D project digitizes existing production engineering knowledge and applies it automatically to the existing data basis (CAD data). The solution offered enables companies without their own production costing department to draw on production engineering know-how.
Contact person: Dr. Martin Erler
Development of an automated design-accompanying manufacturability analysis based on CAD data - manufacturability analysis
The aim of the project is to develop a process for the automated and design-accompanying provision of information for the designer, which enables him to reduce the costs of machining the component he has designed during the design process. The designer has a special role to play in the product development process (PDP), as around 85% of all subsequent costs are determined during the design phase. Early detection of a design that is not suitable for production reduces the costs for the entire product sustainably and with little effort.
Contact person: Dr. Martin Erler
Development of a deterministic process model to determine the performance limits and cutting parameters for nano-polycrystalline diamonds as cutting/dressing material - nanoPD
The aim is to develop new ultra-precision tools with ultra-hard nano-polycrystalline diamonds as an innovative cutting material. This form of diamond, directly synthesized from graphite under high-pressure and high-temperature conditions without the addition of binders or sintering aids, significantly outperforms conventional diamonds thanks to its outstanding mechanical and chemical properties. Building on this, technical and technological developments are being made for the manufacture of turning and dressing tools with the aim of producing ultra-precision tools with a significantly longer service life and higher cutting edge sharpness. With the development of a deterministic process model, the most suitable technological parameters for various applications are to be determined mathematically and scientifically for the new tools in order to be able to offer tools and technology at the end.
Contact person: Dr. Martin Erler
AeroCut 4.0 - Development of an intelligent analysis and optimization system based on a digital process twin to increase productivity in the milling of complex components made of high-performance materials for the aerospace industry
Sub-project: Applications for the analysis and optimization of cutting processes based on cutting models and a digital process twin
The aim is to develop an intelligent analysis and optimization system that allows the specification of realistic production parameters. At the heart of the new system are digital process twins, which are generated for each real manufactured component and are therefore intended to represent the respective component-specific manufacturing processes as accurately as possible. This digital image is based on process data resulting from the machining process and is used in conjunction with planning data to forecast improved milling processes for LuR components made from high-performance materials.
Contact person: Dr. Martin Erler
BNNCut - "Development of innovative cutting tools made of nanocrystalline, binder-free boron nitride ("boron nitride nanocomposite" - BNNC) to improve the surface quality and extend the process limits
Sub-project: Technological investigation to determine the performance limits and cutting parameters of tools with BNNC as cutting material
Development of a tool system consisting of a BNNC blank and tool holder for longitudinal and transverse face turning. A cutting data recommendation is to be developed for the BNNC cutting material with the resulting tool life and quality specifications for different materials. The aim is to integrate a new cutting material from the semi-finished product to the product for various turning processes for precision machining.
Contact person: Dr. Martin Erler
KennSpan - "Development of software for the intelligent determination of machining parameters as a basis for planning and simulation systems for the development of performance reserves"
Sub-project: Development of an intelligent process for determining machining parameters
Force model-based planning and simulation systems are often unable to exploit their full potential due to a lack of characteristic values. The required characteristic values are not available as a database. This makes it necessary to develop a method for determining characteristic values as quickly and flexibly as possible to supply existing planning and simulation systems.
The aim of this project is to develop an automated determination of characteristic values for machining processes using an intelligent process. The "intelligence" is achieved using the machine learning method with artificial neural networks. The development is to be implemented, tested and validated as the software product KennSpan.
Contact person: Dr. Martin Erler
modAK - Development and use of novel tool concepts to increase the productivity of robust heavy-duty machining, taking into account the blank geometry and its effects
Sub-project: Development of the theoretical basis and experimental support for the implementation of sensor-supported clamping position correction and innovative tool concepts for turning operations
The aim of the project is to increase the productivity of heavy machining at GWS GmbH in the field of turning. With this machining step, an initial machining operation is carried out on cast and forged parts to achieve a workpiece geometry suitable for subsequent steps. The use of new support tools and tool concepts is required to improve problematic machining. First of all, a clamping position correction with sensor-supported blank detection for unbalance reduction is developed and implemented. Another aspect is the use of modular actuator tools. The resulting multi-bladed overall tool integrates adjustable infeed axes controlled in the cut. Automated detection of the out-of-roundness of the blank is intended to achieve an adapted cutting depth setting. As a third approach, the project is developing actively vibration-damped turning tools for heavy-duty machining. GWS GmbH is transferring the results to production and developing them further. These approaches should make machining at least 10 percent more effective.
Contact person: Dr. Martin Erler
ProViLK- Process chain virtualization in planning for the development of an integrated teaching and learning concept
The aim is to link the manufacturing fundamentals of production planning and execution. To this end, a study-accompanying concept for complex learning and work tasks for machining production is to be developed. A designed modular structure, supported by simulation software, enables the implementation of a self-directed and interdisciplinary acquisition of skills. The virtual learning environment is characterized by a strong practical orientation and long-term applicability.
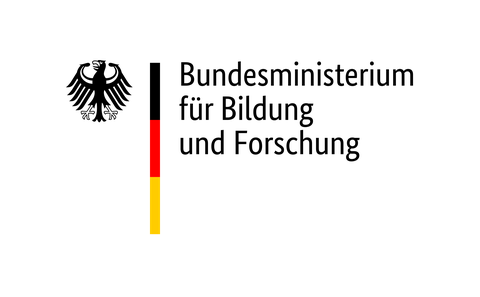
Das Projekt wird über das Hochschuldidaktische Zentrum Sachsen im Rahmen des Verbundantrages „Lehrpraxis im Transfer. Hochschulübergreifende fachspezifische Hochschul- und Mediendidaktik an sächsischen Universitäten“ durch das BMBF gefördert
Contact person: Dr. Martin Erler