Kondensatorentladungsschweißen an der Technischen Universität Dresden
Inhaltsverzeichnis
Das Kondensatorentladungsschweißen
Das Kondensatorentladungsschweißen (KE-Schweißen) ist ein Pressschweißprozess, zählt zum Widerstandsschweißen und wird meist zum Buckelschweißen, selten zum Widerstandspunktschweißen eingesetzt. Charakteristisch ist ein sehr hoher (bis 1000 kA) kurzer (< 15 ms) Schweißstromimpuls, der über eine transformierte Kondensatorentladung erzeugt wird.
Wesentliche Vorteile des KE-Schweißens sind:
- sehr kurze Prozesszeit:
- sehr kurze und lokale begrenzte Wärmeeinbringung
- geringe thermische Belastung der Bauteile und Elektroden
- geringer Elektrodenverschleiß
- kurze Taktzeiten
- sehr hohe Leistungsdichten
- geringe Netzbelastung und geringe notwendige elektrische Anschlussleistung
- sehr gute Reproduzierbarkeit
- hohe Prozesssicherheit
Dadurch ergeben sich folgende Anwendungsbereiche:
- Schweißen von wärmeempfindlichen Bauteilen (z. B: martensitische Stähle, Feinkornstähle, vergütete Werkstoffe (ohne nachträgliche Wärmebehandlung))
- Schweißen von Bauteilen mit großen Dickenunterschieden
- Schweißen großer Bauteilen ( Ringbuckel bis Ø 200 mm)
- Schweißen von Werkstoffen mit hoher elektrischer und thermischer Leitfähigkeit (z.B: Aluminium und -legierungen, Kupfer und –legierungen)
- Schweißen von Mischverbindungen (z. B. Stahl -> Messing) (Siehe Bild1)
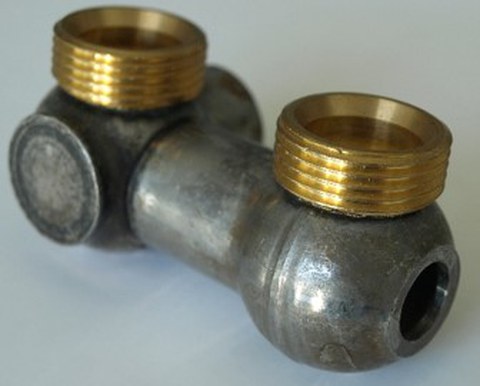
Bild 1: Anwendungsbeispiel des KE-Schweißens
Verfahrenstechnische Grundlagen
Das KE-Schweißen unterscheidet sich von anderen Buckelschweißprozessen hauptsächlich durch die Art der Schweißstromquelle und die daraus resultierende Stromform. Im Gegensatz zu herkömmlichen Wechsel- oder Gleichstromquellen wird die für das Schweißen notwendige Energie nicht während des Schweißens direkt aus dem Netz entnommen (was zu einer kurzzeitigen hohen Netzbelastung führt). Eine Kondensatorbatterie dient als Zwischenspeicher und wird zum Schweißen über einen Impulstransformator entladen (siehe Bild 2). Es entsteht ein impulsförmigen Gleichstrom mit hohem Spitzenwert von bis zu 1000 kA bei Schweißzeiten von 3-15 ms.
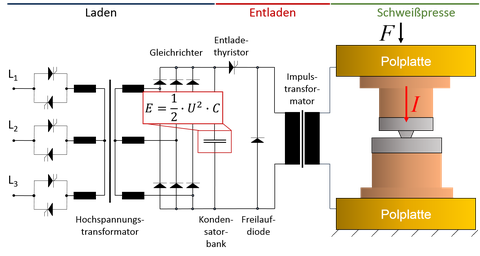
Bild 2: Schematischer Aufbau einer KE-Schweißanlage
Die einzustellenden Parameter sind die Elektrodenkraft und die Ladeenergie bzw. Ladespannung der Kondensatoren. Je nach Maschinenkonzept ist auch das Verändern der Kapazität der Kondensatorbank sowie der Transformatorübersetzung (meist nur durch Veränderung der Verdrahtung) möglich, um den Stromverlauf an die Schweißaufgabe anzupassen.
Nach dem Einlegen der Bauteile in die Schweißmaschine und dem Startsignal läuft werden die folgenden Schritte ausgeführt (siehe Bild 3):
- Schließen der Elektrode, Aufbau der Vorkraft, ggf. Bauteilkontrolle,
- Aufbau der Schweißkraft
- Zünden des Entladethyristors
- Stromimpuls mit Imax, Erwärmung der Fügezone,
- Nachsetzen der Elektroden
- Abkühlung der erwärmten Bereiche
- Öffnen der Elektroden, Bauteilentnahme
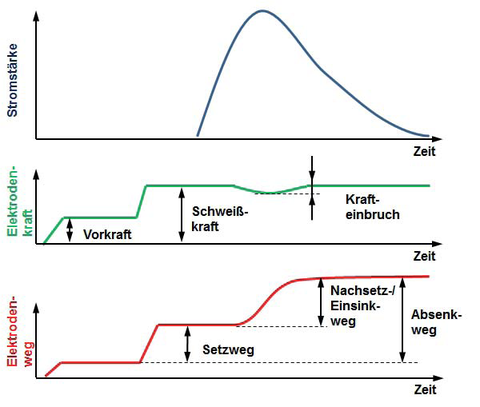
Bild 3: Ablauf des KE-Schweißens (schematisch)
Die Stromform (siehe Bild 4) wird durch die elektrischen Eigenschaften der Kondensatorentladungsschweißmaschine, die einen Reihenschwingkreis aus kapazitiven und induktiven Anteilen darstellt beeinflusst. Maßgebend sind:
- Kapazität der Kondensatorbank
- Ladespannung
- Übersetzungsverhältnis des Impulstransformators
- Widerstände und Induktivität im Primärkreis
- Widerstand der Fügestelle
Eine Steuerung der Schweißzeit und der Stromstärke, wie beim Schweißen mit Wechsel- oder Gleichstrom, ist somit nicht möglich.
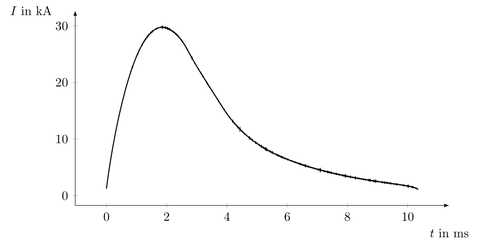
Bild 4: Stromform beim KE-Schweißen
Neues Prozessverständnis: Kurzzeitschweißen mit hoher Wärmestromdichte
Das Kondensatorentladungsschweißen zählt zu den Widerstandspressschweißverfahren. Das bedeutet, dass ein spritzerarmer Prozess erwartet wird, der eine Schweißlinse erzeugt. In der Realität treten jedoch fast immer Spritzer während des Schweißens auf und es werden häufig Schweißverbindungen ohne Schweißlinse erzeugt (siehe Bild 5).
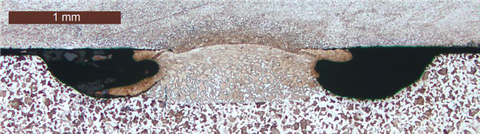
Bild 5: Schliffbild der Schweißverbindung eines Buckels
- Schließen der Elektrode, Aufbau der Vorkraft, ggf. Bauteilkontrolle,
- Aufbau der Schweißkraft → plastische Verformung des Buckels (Setzen), Ausbildung der Kontaktflächen und des Kontaktwiderstands
- Zünden des Entladethyristors → Beginn Stromfluss
- Ansteigende Stromstärke bis Imax, → sehr starke Wärmeentwicklung in der Kontaktzone, Metalldampfbildung, Aktivierung der Oberflächen im Kontaktbereich, Beginn der Erwärmung des Buckelvolumens
- Abklingen der Stromstärke → Abklingen der Metallverdampfung, zunehmende Erwärmung des Buckelvolumens, Entfestigung der Buckelmaterials, Elektrodenkrafteinbruch, Nachsetzen der Elektroden, plastische Verformung des Buckels, Ausprägung der Fügeverbindung, Abkühlung der erwärmten Bereiche
- Öffnen der Elektroden
Die Tatsache, dass die geforderte Festigkeit einer KE-Schweißung auch ohne ausgeprägte Schweißlinse erreicht wird, wird bisher oft nicht akzeptiert. Sie lässt sich jedoch leicht erklären, wenn das KE-Schweißen nicht nur als Widerstandsschweißverfahren aufgefasst wird, sondern auch als Kurzzeitschweißen mit hoher Wärmestromdichte (KShW). Entsprechend der Anlagenkonfiguration, den Schweißparametern sowie dem Bauteil stellen sich bei „langer“ Schweißzeit mit flacher Stromkurve ausschließlich ohmsche Erwärmungsvorgänge (Widerstandsschweißen) und bei „kurzer“ Schweißzeit mit hoher Stromkurve zusätzliche Metallverdampfung (KShW) ein. Bei der Überschreitung des Siedepunktes wird das Volumen durch die Expansion beim Verdampfen um ca. das 33 000-fache vergrößert (Vergleich Gasvolumen bei Verdampfungstemperatur mit Festkörpervolumen bei Raumtemperatur). Dies führt zu einer starken Beschleunigung des Metalldampfes nach außen. Oberflächenschichten (äußere Grenzschicht, Bild 4), die die Verbindungsbildung verhindern, werden aus der Fügeebene geschleudert und die Neubildung von Oxiden wird durch die reduzierende Wirkung des heißen Metalldampfes verhindert. Außerdem wird vorhandene Schmelze mitgerissen und herausgeschleudert. Die stoffschlüssige Verbindung in der Fügezone entsteht durch Aufeinanderpressen der aktivierten Flächen. Bei gleichzeitiger lokaler plastischer Verformung des Fügebereichs werden zusätzlich zur ausgebildeten Schmelze nicht aktivierte Oberflächenanteile aus der Fügezone gepresst.
Messungen in Verbindung mit Hochgeschwindigkeitsaufnahmen (siehe Video 1) zeigen einen Nachweis der Metalldampfentstehung. Es ist zu beobachten, dass kurz vor Erreichen des Strommaximums ein stoßartiger Auswurf von Mikrospritzer auftritt. Die Geschwindigkeit der Mikrospritzer kann anhand des zurückgelegten Weges mehrerer Spritzer innerhalb zweier, aufeinanderfolgender Bilder und der Bildfrequenz auf ca. 50 m/s (180 km/h) abgeschätzt werden. Diese hohen Geschwindigkeiten sind nur mit der Metallverdampfung, einhergehend mit der oben beschriebenen Volumenexpansion, erklärbar.
Hochgeschwindigkeitsaufnahme Einzelbuckel © Max-Martin Ketzel
Ansprechpartner
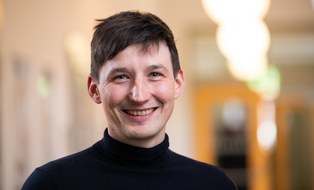
Wissenschaftlicher Mitarbeiter, SFI
NameHerr Dr.-Ing. Johannes Koal
Forschungsgruppenleiter Thermisches Fügen
Eine verschlüsselte E-Mail über das SecureMail-Portal versenden (nur für TUD-externe Personen).
Besuchsadresse:
Zeuner-Bau [ZEU], Raum 327D Helmholtzstraße 5
01069 Dresden
Deutschland