Mikro-Widerstandspunktschweißen & -löten
Table of contents
Untersuchungsschwerpunkte
Das ein- und beidseitige Widerstandspunktschweißen erhält im Bereich robuster bzw. hoch beanspruchter Sensoren eine zunehmende Bedeutung. Beim einseitigen Schweißen kann in direktes und indirektes Punktschweißen unterschieden werden (Abbildung 1). Die hohe Prozesssicherheit und die kurze Fertigungszeit bilden die Interessengrundlage und die thermisch belastbare Verbindung das Entscheidungskriterium. Im Detail sind Schwerpunkte drahtförmige Strukturen untereinander oder mit Blechstrukturen zu verbinden. Dabei treffen die vielfältigsten Materialien (Kupfer, Zinn, Eisen, Nickel, Platin, Gold, Silber) aufeinander. Ein Forschungsfokus liegt somit darin, neue Erkenntnisse zum Werkstoffverhalten zu gewinnen und prozessbeeinflussenden Faktoren zu erarbeiten. Eingesetzt werden derartige Sensorstrukturen u. a. in Motorräumen, bei Leistungsteilen der Elektromobilität sowie bei grundlegenden Aufgaben der Luft- & Raumfahrt.
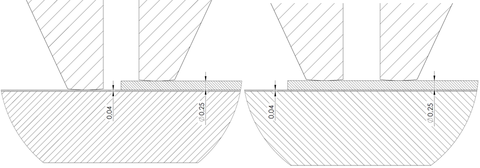
Abbildung 1: Direktes und indirektes Mikropunktschweißen
Anlagentechnik und konkrete Beispiele
Mit vier unterschiedlichen Schweißgeräten kann nahezu jede Mikro-Widerstandsschweißaufgabe realisiert werden. Der Strom lässt sich von 50 A bis 8000 A und die Kraft von 0,5 N bis 500 N pro Elektrode frei einstellen. Sollten größere Prozesskräfte benötigt werden, können diese zusätzlich über Druckluft ermöglicht werden. Jede Elektrode kann separat geführt und geregelt werden, wodurch einseitig zugängliche Punktschweißaufgaben und beidseitig zugängliche Schweißaufgaben durchgeführt werden können. Die Regelbarkeit des Stromes in Schritten von 0,1 ms erlaubt es auch empfindliche Werkstoffe zu verschweißen bzw. zu verlöten.
Neben zwei automatisierbaren Systemen (Abbildung 2), steht auch ein System für den mobilen Einsatz zur Verfügung. Mit zwei weiteren Systemen können beliebige Schweiß- und Lötaufgaben von reinem Experimentierumfang, bis Klein- oder Großserienfertigung abgebildet werden.
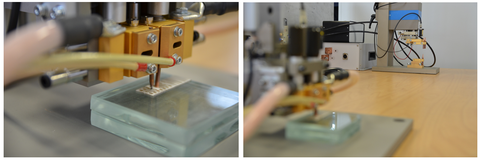
Abbildung 2: Anlagentechnik Mikroschweißen
- Druckkraftbereich von 0,5 N bis 500 N pro Elektrode (im statischen Druckbereich auch bis 6 bar möglich)
- Leistungsstufen von 50 A bis 8000 A
- Regelzeiten von 0,1 ms (10 kHz) oder 0,02 ms (50 kHz)
- Wahlweise Strom-, Spannungs-, Leistungs-
oder Temperaturregelung - Können als Inverter- oder Kondensatorentladungs- oder
als Induktions-Stromquelle eingesetzt werden - Flexibel als mobiles System oder Fertigungssystem konzeptionierbar
Ansprechpartner
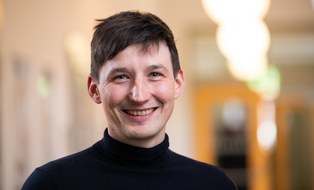
Scientist, IWE
NameMr Dr.-Ing. Johannes Koal
Research Group Leader of Thermal Joining
Send encrypted email via the SecureMail portal (for TUD external users only).
Visiting address:
Zeuner-Bau [ZEU], Room 327D Helmholtzstraße 5
01069 Dresden
Germany