DFG UL 121/14-1 - Berechnung des effektiven Verbundverhaltens durch Homogenisierung auf Basis von mikromechanisch gemessenen Materialeigenschaften
Berechnung des effektiven Verbundverhaltens durch Homogenisierung auf Basis von mikromechanisch gemessenen Materialeigenschaften
Im Projekt wird ein auf Homogenisierungsverfahren basierendes Konzept zur skalenübergreifenden Modellierung der Schädigung in Faser-Kunststoff-Verbunden auf drei Skalen - Mikro, Meso und Makro - verfolgt. In der ersten Projektphase wurde die Methodik entwickelt, um die Eigenschaften der Fasern und der Faser-Matrix-Grenzschicht auf Mikroebene zu bestimmen. Zur Charakterisierung dieser wurden Simulationen und experimentelle Ergebnisse von Einzelfaserfragmentierungsversuchen (SFFT) und Einzelfaserauszugsversuchen (Pullout) verglichen. Die viskoelastischen Eigenschaften der Matrix wurden ebenfalls identifiziert. In der zweiten Projektphase soll zunächst das ratenabhängige Schädigungsverhalten des Matrixmaterials im Abgleich mit Experimenten modelliert und parametrisiert werden. Damit ist das Verhalten aller Bestandteile des Verbundes bekannt. Aufbauend auf diesem Kenntnissstand wird das effektive Schädigungsverhalten von Faserverbunden auf Makroebene durch eine zweistufige numerische Homogenisierung bestimmt. Diese Homogenisierung basiert auf der Simulation von repräsentativen stochastischen Verteilungen von Faserfilamenten und -festigkeiten auf der Mikroebene sowie der Verstärkungsstruktur aus Rovings auf der Mesoebene. Sämtliche Simulationen werden begleitet von Experimenten, um Modellparameter zu kalibrieren und Voraussagen zu validieren. Neben den eingangs erwähnten Experimenten dienen Versuche an Mehrfaserproben der Validierung des Zusammenspiels von Matrix- und Grenzflächenschädigung auf Mikroebene. Die Homogenisierungsergebnisse werden an unidirektional und mehraxial verstärkten Proben validiert. Die vorgesehene Untersuchung ist grundlegender Natur. Die betrachtete Materialkombination (E-Glas und Epoxidharz) sowie die Verstärkungsgeometrie (Faserstruktur) sind beispielhaft. Die Ergebnisse sind dennoch von unmittelbarem Interesse für die Anwendung von Faser-Kunststoff-Verbunden. Im Vergleich zu Stahl oder Aluminium wird ihr Potential mangels Quantifizierung des Schädigungsverhaltens bisher schlecht ausgenutzt.
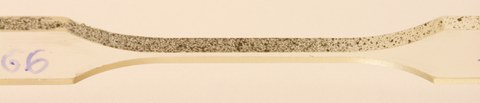
Probe für den Einzelfaserfragmentierungsversuch. In dieser Epoxidharz-Zugprobe ist ein einzelnes Glasfaserfilament eingegossen. Der Zugversuch anhand solcher Proben ermöglicht die Charakterisierung von Faser- und Grenzflächeneigenschaften, da die Faser aufgrund geringerer Bruchdehnung vor dem Matrixmaterial reißt.

Spannungsoptische Aufnahme während des Zugversuches.
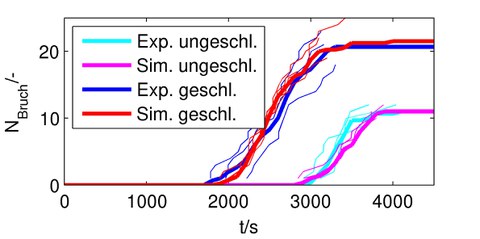
Entwicklung von Faserbrüchen in Experiment und Simulation anhand zweier Fasertypen. Je drei dünne Linien kennzeichnen einzelne Versuche bzw. Simulationen, dicke Linien die mittlere Faserbruchentwicklung.

Vergleichsverzerrung in der axialsymmetrischen Simulation von Einzelfaserfragmentierungsversuchen. Zum abgebildeten Zeitpunkt sind sechs Faserbrüche anhand von Überhöhungen der Vergleichsverzerrung an der unteren Seite zu erkennen.
Projektmitarbeiter
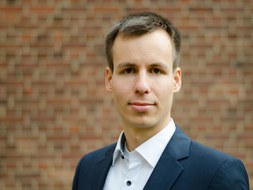
Dipl.-Ing. Joseph Goldmann
Eine verschlüsselte E-Mail über das SecureMail-Portal versenden (nur für TUD-externe Personen).
Professur für Numerische und Experimentelle Festkörpermechanik
Professur für Numerische und Experimentelle Festkörpermechanik
Besuchsadresse:
Zeunerbau, Zimmer 356 George-Bähr-Straße 3c
01069 Dresden
Projektleitung

Seniorprofessor
NameProf. Dr.-Ing. habil. Volker Ulbricht
Eine verschlüsselte E-Mail über das SecureMail-Portal versenden (nur für TUD-externe Personen).
Professur für Numerische und Experimentelle Festkörpermechanik
Professur für Numerische und Experimentelle Festkörpermechanik
Besuchsadresse:
Zeunerbau, Zimmer 352 George-Bähr-Straße 3c
01069 Dresden