HyTank
Test and simulation-based analysis of bonded joints for cryogenic applications and sustainability considerations for the joining process of a CFRP LH2 tank for commercial aviation
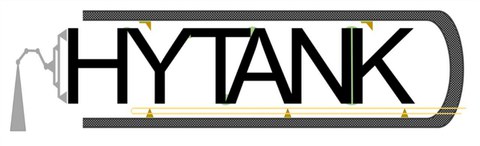
Project logo.
In order to be successful on the market in the long term, the German aviation industry must respond to the increasing demand for CO2-emission-free flying. Cryogenic hydrogen as a fuel in combination with a turbine or fuel cell-powered engine is a promising solution. In addition to research into new propulsion systems, intensive research must also be carried out into tank systems for liquid hydrogen, as mass-optimised storage is a key element in the implementation of emission-free flight.
The main objective of the HYTANK joint project is to make a significant contribution to the development of tanks made of carbon fibre reinforced plastics (CFRP) for cryogenic hydrogen storage in order to realise emission-free passenger aircraft. CFRP offers immense lightweight construction potential compared to available metallic tanks, which is of particular importance for aircraft with longer ranges. The HYTANK consortium therefore aims to develop resource-efficient processing and assembly methods for liquid hydrogen tanks made of CFRP and to implement and test them in production technology. TU Dresden is focusing on the experimental clarification and mathematical description of the influence of liquid hydrogen on the behaviour of the joining partners in the laminate thickness direction, the damage to the adhesives and the resulting bonded joints. The development of customised methods for tests in a cryogenic environment is the main focus here. In addition, the curing process of the adhesives is analysed with regard to its reaction kinetics in order to demonstrate the most energy-efficient process control possible. The joining process is evaluated in the consortium using LCA.
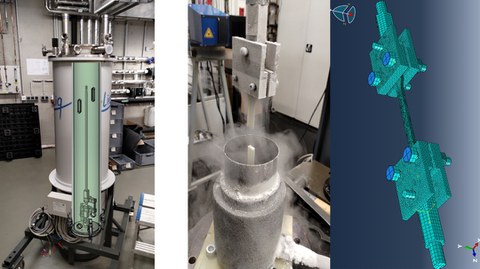
Cryostat for testing in LH2 (left), example: Tensile test in LN2 with digital model (right).
01.04.2023–30.06.2026
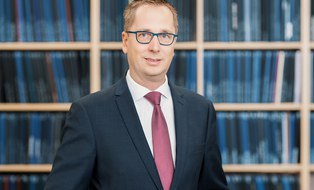
Chair of Lightweight Systems Engineering and MultiMaterial Design
NameProf. Dr.-Ing. habil. Maik Gude
Send encrypted email via the SecureMail portal (for TUD external users only).
Institute of Lightweight Engineering and Polymer Technology
Visitors Address:
DÜR, Floor 0, Room 71 Holbeinstr. 3
01307 Dresden
Deutschland
- Dr. Jörn Jaschinski (Testing Methods and Material Models|Thermoplastics Processing)
Publications Jörn Jaschinski | TU Dresden